PPT Vision adds JAI cameras to enhance M-Series embedded machine-vision line
Industrial machine-vision camera manufacturers JAI (San Jose, CA, USA) and PPT Vision (Bloomington, MN, USA) have announced that JAI's CM-140GE-UV ultraviolet (UV) camera and CM-030GE-RH remote-head camera models will be incorporated into PPT's M-Series embedded machine-vision system lineup.
Industrial machine-vision camera manufacturers JAI (San Jose, CA, USA) and PPT Vision (Bloomington, MN, USA) have announced that JAI's CM-140GE-UV ultraviolet (UV) camera and CM-030GE-RH remote-head camera models will be incorporated into PPT's M-Series embedded machine-vision system lineup. Other JAI cameras may be added at a later date.
The 1.4-Mpixel (1392 x 1040 pixels), 16-frame/s CM-140GE-UV utilizes the shorter wavelengths of UV light to capture fine surface details or to image items that radiate light below the visible spectrum, which can support semiconductor inspection, biomedical analysis, and other sophisticated applications.
The integration of the JAI UV camera into the M-Series family enables customers to leverage the power of an industrial-grade UV camera with an embedded vision system. The cameras standard GigE Vision interface can be connected to the M-Series processing unit with up to 100 m of standard Ethernet cabling.
The CM-030GE-RH camera features a 17-mm-diameter, 46-mm-long remote imaging head connected to the main camera body by a flexible 2-m cable, and is designed for applications involving limited space and/or high-speed repetitive motion, such as pick-and-place machines, pipe inspection, or "industrial endoscopy" tasks. Pixel resolution of the remote head camera is 656 x 494, with a rate of 120 frames/s and a standard GigE Vision digital interface.
Featured Product
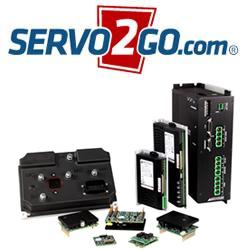