New Subsea Drill Passes Schilling Robotics Factory Acceptance Testing
Schilling Robotics, LLC, experts in subsea systems, and Gregg Marine, Inc., experts in drilling and geotechnical testing services, announced today the successful completion of their Factory Acceptance Testing on their new Seafloor Drill. Gregg will begin field testing of their drill in the waters offshore of Vancouver, British Columbia this July.
DAVIS, Calif., Jun 28, 2011 (BUSINESS WIRE) -- Schilling Robotics, LLC, experts in subsea systems, and Gregg Marine, Inc., experts in drilling and geotechnical testing services, announced today the successful completion of their Factory Acceptance Testing on their new Seafloor Drill. Gregg will begin field testing of their drill in the waters offshore of Vancouver, British Columbia this July.
The Seafloor Drill was conceived by John Gregg, president of Gregg Drilling, Inc. He approached MARL Technologies and Schilling Robotics to bring his concept into reality. MARL was able to provide the drilling platform, and Schilling engineered the controls, power systems, and subsea packaging for the system. "This is one of the first platforms commercially available to truly compete with traditional geotechnical drill ships, and the only one to utilize patented wireline technology," said Gregg. "The design and durability of this platform will save companies on cost, increase accuracy, and offer a positive environmental impact. The system is rated to 3,000msw and with the initial tooling, will drill up to 500ft (150m) under the seabed. This is the first seabed drilling unit to combine this much power and drilling precision on the seabed." Combined with Gregg's 3000msw rated DeepCPT and 6m One-pass Drill, the Seafloor Drill will benefit oil and gas companies, mineral and mining companies, as well as scientific organizations. Gregg feels that in the future with additional tooling capacity the unit will be capable of exceeding 200m.
"We are proud to again partner with Gregg Marine for the engineering and assembly of their Seafloor Drill system. This is the first of four systems that Gregg will build, and it is changing the landscape of drilling and core sampling technology," said Tyler Schilling, president and CEO of Schilling Robotics, LLC. "We are excited to be a part of the innovation and global applications that Gregg is implementing," said Schilling.
The Drill will be used for geotechnical surveying and core sampling, but its design flexibility also allows Gregg to change the tools downhole for additional activities. Utilizing patented wireline technology through a license from Williamson Technologies, Gregg will be able to switch out the drill head and perform Cone Penetration Testing (CPT) to determine strength parameters in soft soils. Other tools are being developed, such as a downhole vane shear test and geophysical tools to give 3D modeling capabilities. Gregg's seafloor drill will revolutionize the industry with the capability to offer all of these technologies within one platform.
About Schilling Robotics, LLC
Schilling Robotics is a leading global, deep-ocean robotics company founded in 1985. Schilling is headquartered in California U.S.A. and has regional offices in Texas, U.S.A., Aberdeen, U.K., and Singapore. Since late 2008, FMC Technologies, Inc. has held a 45% interest in Schilling. FMC Technologies, Inc. /quotes/zigman/282674/quotes/nls/fti FTI -2.73% is a leading global provider of technology solutions for the energy industry. FMC Technologies designs, manufactures, and services technologically sophisticated systems and products, such as subsea production and processing systems, surface wellhead systems, high pressure fluid control equipment, measurement solutions, and marine loading systems for the oil and gas industry. Further information about Schilling Robotics can be found at www.schilling.com .
About Gregg Marine, Inc.
Since 1985, Gregg Drilling & Testing, Inc. has been widely recognized as a leader and innovator in drilling, sampling, and subsurface investigation, providing clients in industry and government with the highest quality services. Gregg set the standard among drilling companies through the pursuit of one simple goal: To provide clients with high-quality, innovative services performed in a timely and cost-effective manner.
Gregg Marine, Inc. was formed from the existing marine division of the company, to focus specifically on meeting the increasing demand for quality offshore drilling and sampling services. In addition to offshore geotechnical drilling, Gregg Marine leverages Gregg Drilling's extensive experience developing state-of-the-art cone penetration and direct-push technologies, including the 3000msw rated DeepCPT system. It's our ability to combine cutting-edge equipment, advanced technologies and innovative thinking that sets Gregg apart and allows us to provide exceptional performance and value time after time. Gregg is headquartered in Signal Hill, California U.S.A., and has regional offices in Martinez, California, East Palo Alto, California, and Livingston, Texas. Further information about Gregg can be found at http://www.greggdrilling.com/index.html
About MARL Technologies
MARL Technologies Inc. is a custom design/ build drill manufacturer specializing in geotechnical drills. We work collaboratively with each client to create equipment exactly suited to their needs. MARL Technologies was incorporated in 1977, and is founded on geotechnical experience that goes back to 1959. In addition to regularly serving clients in the United States and Canada, MARL Technologies has designed and built equipment for the hostile climates and challenging drilling conditions of the Arctic, Antarctic, Middle East, Asia and South America. Streamlined, powerful and modern, MARL Technologies products deliver excellent performance, enhanced safety, ergonomics, and value. Further information about MARL can be found at http://www.marltechnologies.com/about.html
Featured Product
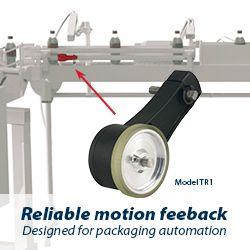