US-Manufactured Nanopositioning Stage for Super Resolution Microscopy, Material Science
High-precision motion control solutions for high-resolution microscopy & imaging, new from PI
PI (Physik Instrumente), a global leader in nanopositioning motion control for life sciences, semiconductor, and photonics, offers a series of piezo-flexure controlled nanopositioning stages for high-resolution microscopy and material science applications. The P-545 PInano® piezo stage family is engineered for nanometer scale accuracy, high stability, and high scanning speed, by PI's US design and manufacturing team in Hopkinton, MA.
Performance-Driven Design for Ultra-Fine Control at the Nanoscale
Built to provide motion control performance with stability and resolution at the nanoscale, P-545 PInano® piezo stage family integrates state-of-the-art, space-tested piezoelectric drive technology and offers a choice of position feedback sensors for nanometer precise measurements: Capacitive, non-contact sensors are available as well as highly sensitive piezoresistive strain gauge sensors. Both types provide sub-nanometer resolution, while capacitive sensors are the preferred choice when it comes to maximizing linearity and long-term stability.
Features and Benefits of the PInano® Nanopositioning Stage Family
Includes High-Performance Motion Controller: a digital servo piezo controller / driver with USB, TCP/IP, RS-232, and high-resolution analog interfaces is included, along with a software suite and LabView drivers.
Combines with Manual Stages and Long Travel Motorized Stages.
Multi-Axis Flexibility: supports up to three axes of motion (X, Y, Z), in one low profile design, making it adaptable for complex positioning needs in a compact package.
Special High-Speed Version: a direct-drive variant with a high-power driver/controller is specifically designed for the fastest response times in particle-tracking applications.
Sub-Nanometer Resolution: leveraging advanced piezo actuators, the P-545 delivers nanoscale positioning resolution and repeatability.
High-Bandwidth: capable of rapid and precise movements with millisecond response times, and high scanning rates, critical for high-throughput applications.
Compact Footprint: ideal for applications where space is limited, offering easy integration into larger systems or confined setups.
Closed-Loop Control: equipped with high-resolution position sensors, the P-545 stage delivers stability and repeatability with active feedback control.
Combination with Long-Travel Inverted Microscope Stages
The PInano® piezo nanopositioning stage family easily combines with motorized long-travel microscope stages, such as PI's new U-781 inverted microscope stage and M-545 manual microscope stages.
Applications and Use Cases - Optimized for Imaging and Beyond
The P-545 PInano® stage's closed-loop control and high-speed mechanics make it highly suitable for a variety of applications, including those requiring smooth, multi-axis motion with high stability, as well as highly dynamic tasks. Its advanced feedback system enables reliable positioning accuracy, scanning speed, and stability over extended operation periods, supporting applications such as biological imaging, semiconductor inspection, photonics testing, particle tracking, 3D imaging, and super-resolution microscopy.
The P-545 PInano® piezo stage is available for immediate order in a range of configurations to meet diverse nanoscale application needs. Options include XY or XYZ axes, standard or high-speed versions, and feedback via capacitive measuring sensors or piezoresistive sensors, allowing for customization based on specific performance and application requirements.
More information:P-545 PInano® series
Request a demo:Schedule with a PI Engineer
Learn more:Microscopy applications
Industries Served
Microscopy, Material Science, Semiconductor Test and Metrology, Photonics
Featured Product
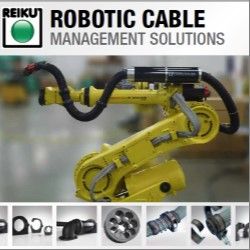
REIKU's Cable Saver™ - The Most Versatile Modular Robotic Cable Management Solution
REIKU's Cable Saver™ Solution eliminates downtime, loss of revenue, expensive cable and hose replacement costs, maintenance labor costs. It's available in three sizes 36, 52 and 70 mm.
All of the robots cables and hoses are protected when routed through the Cable Saver™ corrugated tubing.The Cable Saver™ uses a spring retraction system housed inside the Energy Tube™ to keep this service loop out of harms way in safe location at the rear of the Robot when not required. The Cable Saver™ is a COMPLETE solution for any make or model of robot. It installs quickly-on either side of the robot and has been tested to resist over 15 million repetitive cycles.
REIKU is committed to providing the most modular, effective options for ensuring your robotic components operate without downtime due to cable management.
www.CableSaver.com