Stretch currently unloads boxes autonomously at the Hermes Fulfillment center, while Spot supports predictive maintenance by inspecting fire exits and structural changes and detecting air and gas leaks.
Stretch and Spot: Increasing Operational Efficiency and Making Warehouse Work Safer
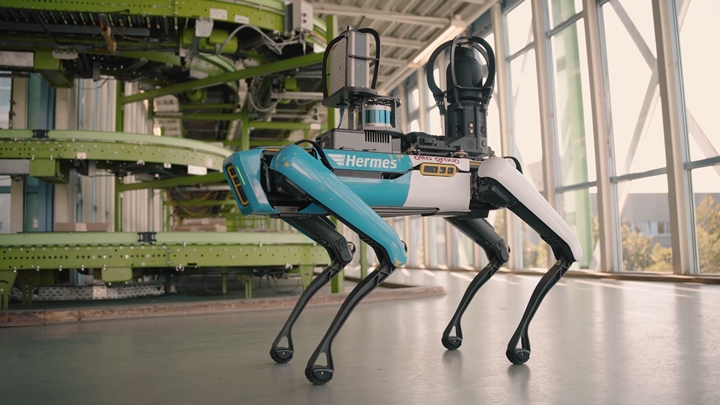
Q&A with Jojo Winsor, Project Engineer | Boston Dynamics
Tell us about yourself and your role with Boston Dynamics.
At Boston Dynamics, I am responsible for deploying Stretch robots to customer sites. This involves working closely with customers to understand their sites and needs, forming a deployment strategy for each site, and managing the installation of the off-robot safety system(s) that allow Stretch to safely unload boxes in the warehouse environment. My background is in mechanical engineering and prior to Boston Dynamics I worked on a variety of exciting projects in aerospace, defense, sensor integration, and underwater robotics.
Give us some background on Otto Group and the use case utilizing Boston Dynamics robots.
Otto Group, a global leader in e-commerce, deployed Boston Dynamics' Stretch and Spot robots to enhance logistics and safety. Stretch currently unloads boxes autonomously at the Hermes Fulfillment center, while Spot supports predictive maintenance by inspecting fire exits and structural changes and detecting air and gas leaks. This is the first-ever deployment of both Spot and Stretch in the same facility and the debut deployment of Stretch in Europe. The use of these robots is expected to expand to over 20 Otto Group sites by 2025.
What challenges did Otto Group face with traditional warehouse operations that these robots are now solving?
The Hermes logistics center needed to improve operations and maintain high safety standards in accordance with Germany’s national standards and directives from the European Union regarding occupational safety and health in the workplace. Stretch was able to tackle the grueling and labor-intensive job of unloading heavy cases so that employees could take on more valuable assignments. Spot’s ability to run autonomous missions also provides additional safety by monitoring fire exits and identifying small structural changes in storage racks. This resulted in higher efficiency, reduced physical strain on workers, and ensured safety compliance.
Can you provide examples of how these robots have begun improving operational efficiency at Otto Group's warehouses?
Stretch has reduced the time and physical strain required for labor-intensive tasks. It is equipped with an adaptive gripper, which can handle many package types and accommodate irregularities and damage, streamlining operations. Spot drives efficiency by regularly collecting thermal images, conducting acoustic vibration detection, reading analog gauges, and detecting ultrasonic air and gas leaks. These inspections improve worker safety, reduce unplanned downtime, and save energy costs.
With peak holiday season approaching, how are Stretch and Spot robots helping Otto Group prepare for fluctuating volumes and demands?
Peak holiday season means a significantly increased workload and often longer hours for employees due to the demand for fast shipping and warehouse services. Stretch can help manage these fluctuating shipping volumes by automating package unloading. Where people may need to take breaks or change shifts, Stretch can work continuously for up to 16 hours, accelerating the unloading process and allowing workers to perform other tasks required during this busy time. This automates unloading speeds, making it easier to schedule shipments, and increases predictability in the warehouse, which is necessary during the holiday season.
How do these robots improve safety and make warehouse work more attractive for employees?
Stretch automates physically demanding unloading jobs, lowering the risk of injuries often associated with overexertion from lifting and lowering heavy objects. Also, because trucks and shipping containers aren’t often temperature-controlled, Stretch can step in so employees no longer need to experience that discomfort. On the other hand, Spot performs regular safety checks to detect common issues in the facility. Since manufacturing facilities are already facing labor shortages, allowing Spot to take on the dull and monotonous tasks frees up employees to focus on other tasks that may be more enjoyable.
What can we take from this use case, and what is the future of warehouse operations?
Automation is the future of warehouse operations. It will allow facilities to manage varying demands with more predictability and efficiency, streamline processes, and establish safer work environments. Robots like Spot and Stretch are transforming warehouse operations by automating dull, dirty, and dangerous tasks and reinforcing safety. This is the first case of Spot and Stretch being used together in the warehouse, and it highlights how the warehouse industry is evolving and moving further towards automation.
Jojo Winsor, Project Engineer at Boston Dynamics is responsible for deploying Stretch robots to customer sites. This involves working closely with customers to understand their sites and needs, forming a deployment strategy for each site, and managing the installation of the off-robot safety system(s) that allow Stretch to safely unload boxes in the warehouse environment. Prior to Boston Dynamics, she worked on a variety of exciting projects in aerospace, defense, sensor integration, underwater robotics, and most recently as a Field Applications Engineer at Humatics.
Jojo has a degree in Mechanical Engineering from the University of Connecticut and enjoys traveling, spending time outside and cooking (rarely following a recipe).
The content & opinions in this article are the author’s and do not necessarily represent the views of RoboticsTomorrow
Comments (0)
This post does not have any comments. Be the first to leave a comment below.
Featured Product
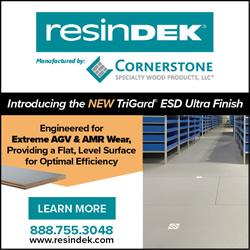