No matter what caused the flooding there will be damage to equipment in your facility. With quick, proper post-flood treatment, you can minimize the damage. We will walk you through the necessary steps to handle your robots after they have been exposed to standing water.
Robot Recovery – Flood Damage
Article from | Motion Controls Robotics, Inc.
In the aftermath of a flood, total robot recovery can be a daunting task. Water damage, especially from contaminants in floodwaters, can severely impact the delicate components within these machines. One crucial aspect of this recovery process is ensuring that all parts, particularly sensitive ones like printed circuit boards (PCBs), relays, joints, and actuators, are thoroughly cleaned and dried. Proper handling and maintenance of these components are vital to prevent long-term damage and ensure the reliable operation of your robotic equipment.
For the best results, it is highly recommended to contact a FANUC Certified Servicing Integrator, such as Motion Controls Robotics Inc. (MCRI), to be onsite for the cleanup. Their expertise will ensure that your robotic components, especially those that have been submerged in water, are handled with the utmost care and precision. This guide provides detailed steps and best practices for cleaning and drying these critical parts, helping you bring your robotic systems back to life effectively and safely.
No matter what caused the flooding there will be damage to equipment in your facility. However, with quick, proper post-flood treatment, you can minimize the damage. We will walk you through the necessary steps to handle your robots after they have been exposed to standing water.
Emergency Robot Recovery – Important First Steps
- The first step is to secure the area. Make sure to safely remove all power sources to prevent
injuries and further electrical damage to the equipment. The sooner you can remove power to the equipment the better the results. If you can predict the flooding, remove power before water overwhelms the area. This step can honestly save you millions of dollars in water damage over your entire facility.
- Once water is exposed to equipment and raw materials, floodwater may contain contaminants such as oils, grease, or production related chemicals. Prior to discharging the water, local regulations should be evaluated to ensure the proper disposal methods. You can also consult your company’s EHS expert to determine the best way to clear the water from the area.
- As you begin the clean-up, remember not to open cabinets and units until the water has been removed from the area.
- If possible, start actively draining the water to reduce damage. This can be done with pumps, wet/dry vacuums, and/or directing water to unobstructed drains or down channels to an exit. For the best results, also bring in dehumidifiers and fans to reduce moisture in the air. For optimal final drying of components, designate a closed-off area equipped with dehumidifiers to place the equipment.
- Once the water has been taken care of, start the procedure of cleaning up the robot system.
- It is highly recommended to have a FANUC Certified Servicing Integrator on site, if possible, during the clean-up process but definitely during the start up to get your machine back-up and running.
Keep in Mind
- When cleaning the system make sure to properly document all equipment with photos and tag or mark cables to reconnect them correctly later.
- Using a drying oven will give you the best results in the recovery of your robot. Drying ovens focus on removing moisture by circulating hot air around the items placed inside them. This is crucial in preventing corrosion, electrical failures, and other future moisture-related issues.
Drying Ovens can be purchased from specialized equipment suppliers like Grainger who can provide detailed specifications and customer support to help you choose the right model.
Robot Recovery Instructions
Start by locating and removing batteries and visible cables
Battery and Cables
Removing & Cleaning
Disconnect battery cables from units and PCBs (Printed Circuit Boards) as soon as possible. Flooded batteries can cause rust and irreparable damage to the PCB circuitry.
Remove all cables before washing. Wipe away any excess water from the cables using a dry cloth. If possible, disassemble the connectors to access and clean inside them with a neutral cleaner like dish soap and warm water. Use a soft nylon brush or a toothbrush to gently scrub the connectors, focusing on areas with visible dirt or contaminants. If possible, rinse connectors, do not get water in the housings or cable strands.
Drying
Hang the cables with the connector at the bottom to dry.
Restoring
While removing the batteries is essential to protect the hardware, removing the batteries will result in loss of robot data. This data can be restored quickly by uploading the robot backup. If you do not have robot backup, you can contact your servicing integrator. Servicing integrators will run a backup before they do annual PMs.
Printed Circuit Boards
Cleaning
PCBs need to be cleaned and dried carefully to prevent corrosion and damage.
- If possible, wear an antistatic wrist strap to prevent electrostatic discharge that can damage components. Start with some compressed air to blow away any loose dirt, water, or debris from the surface of the PCB.
- Next use a soft nylon brush dipped in pure Isopropyl alcohol to gently scrub the PCB, focusing on areas with visible dirt or residue. Be careful not to apply excessive force that might dislodge components.
Drying
Use more compressed air to blow away excess isopropyl alcohol and ensure the PCB is completely dry, paying special attention to hard-to-reach areas under components. Then place in the drying unit at 140°F (60°C) for 1 hour. If this is not available, air dry in a clean, dust-free environment. It’s crucial to ensure the PCB is completely dry before applying power.
Once fully dry and inspected, reassemble the PCB into its housing or system, ensuring all connectors are properly reattached.
Robot Recovery for Relays
Cleaning
If relays contain water, open the case and clean inside. If the case cannot be opened, you will need to replace the relay. To clean relays, wear an antistatic wrist strap to prevent electrostatic discharge that could damage the relay components.
Use a soft nylon brush dipped in isopropyl alcohol to gently scrub the internal components of the relay, such as contacts and coils. Be thorough but gentle to avoid damaging delicate parts.
Drying
Use compressed air to blow away excess isopropyl alcohol and ensure all components are thoroughly dry, especially around the contacts and coils. Allow the relay to air dry completely in a clean, dust-free environment. Ensure no moisture remains before reassembly.
Transformers
Cleaning
Use neutral detergents and soft cloths or brushes to clean the exterior of the transformer, especially around electrical terminals.
Drying
Thoroughly dry using a controlled temperature drying oven. For Servo Transformers dry at 248°F (120°C) for 8 hours. Then Use a 500V Megohm meter to measure insulation resistance between coils and metal parts. It should be 10 Megohms or more. If it has not reached this level, then continue to dry.
Motors
Cleaning
Servo motors and other types of motors that must be cleaned and checked for water ingress. These cannot be disassembled by the customer. If water is visible inside the motor cover, remove the cover to release the water and clean around the feedback assembly. Check for water damage in encoders and replace if necessary.
Drying
Once the motors have been cleaned of visible debris, dry the Servo Motors at 176°F (80°C) for 12 hours (remove pulse coder first). After the 12 hours, Measure insulation resistance between motor windings and ground. It should be 10 Megohms or more. Continue drying if needed.
Motor Drive Units
Use flowing water to clean the units. Do not submerge them during cleaning. Let the units air dry.
Joints and Actuators
Cleaning
Cleaning and drying joints and actuators, especially after exposure to floodwaters, is a delicate process. Carefully disassemble and clean each joint and actuator to remove any contaminants to ensure smooth movement and prevent future rusting. These components are critical for the precise movement and functioning of robots.
If possible, carefully disassemble joints and actuators to access all parts. Document how components are assembled for accurate reassembly. Rinse the components with clean water to remove loose dirt and contaminants. Mix a neutral detergent with water. Using a soft nylon brush or toothbrush, gently scrub the components to remove any adhering dirt, oil, or debris. Pay special attention to connectors and small crevices. Rinse all parts thoroughly with clean water to remove any detergent residue. Avoid submerging electrical components entirely.
Drying
Wipe down components with a dry, soft cloth. Compressed air can also be used to reach the smaller crevices. Parts can be air dried by placing them so water will drain naturally.
Control Units and Sensors
Robots have various sensors and control units that must be cleaned and recalibrated to ensure proper functioning. Use delicate cleaning methods for sensitive sensors and control units to avoid damaging the components.
Grippers and End Effectors
In most cases these components will probably not be affected by the flood, but in certain cases you will also need to inspect, clean, and dry components to maintain the robot’s ability to handle and manipulate objects accurately.
Robot Recovery – Starting-up the Robot
Once all components are dry and insulation resistance is adequate, reinstall the unit. Confirm all connections and wiring from your documentation, then power up and check operation. Watch carefully for abnormal smells or smoke and turn off the power if issues arise.
If the robot is not able to recover through basic cleanup and drying, it probably incurred some irreparable damage. A FANUC Servicing Integrator can come in and run troubleshooting protocols to find the component(s) that may need replaced and order and install those replacements to limit your overall downtime. Many common parts are available quickly from FANUC’s warehouses in Michigan.
By prioritizing the recovery care of your robots, you safeguard not only the equipment but also the future continuity of your production processes.
The content & opinions in this article are the author’s and do not necessarily represent the views of RoboticsTomorrow
Comments (0)
This post does not have any comments. Be the first to leave a comment below.
Featured Product
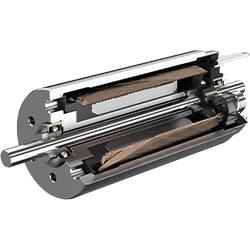