In collaboration with robotics expert, TM Robotics, its South American partner Questt has developed an innovative vial packaging solution that addresses the limitations of manual processes and elevates productivity and performance for life sciences production lines.
Robotic solutions for pharmaceutical packaging - Automated system addresses key limitations of manual processes
Case Study from | TM Robotics
The pharmaceutical, biotechnology, veterinary and life sciences industries are subject to unique challenges where accuracy and efficiency are essential. This applies to all stages of production —including end of line packaging. Though automation use is increasing, many production lines still use human operators to pack products. In collaboration with robotics expert, TM Robotics, its South American partner Questt has developed an innovative vial packaging solution that addresses the limitations of manual processes and elevates productivity and performance for life sciences production lines.
The inherent risk of human error, potential contamination and the demands of regulatory compliance place considerable pressure on packaging operations in life sciences and related industries. Moreover, manual processes often struggle to maintain the precision, speed and consistency required to meet market demands. Traceability concerns and the complexities of quality control present further drawbacks. With the industry demanding high throughput and agility, automated packaging solutions offer an ideal solution.
To address the shortcomings of manual packaging in these sectors, Questt, a South American partner of global robotics supplier TM Robotics, has developed a market-first automated solution. Driven by the need for smarter, faster and more accurate vial packaging, Questt designed its QPack-1 robotic packaging machine as a complete solution.
Enhancing operations with industrial robots
Questt’s QPack-1 machine uses both six and four-axis industrial robots to package vials using continuous movement and automatic feeding. This monobloc turnkey machine system integrates two robots in a single unit, each performing distinct tasks, and the machine has a small footprint, allowing it to be integrated even into smaller spaces.
Operators can program the machine to package a predefined number of vials into a custom thermoformed transparent plastic box. The first robot positions the box in the workspace, while the second transfers vials from the production line using a vacuum attachment to fill it. As pharmaceutical products are also required to come with an enclosed brochure, the first robot can insert this brochure before the box is closed and it moves to the next stage of the production line.
TM Robotics supplies the two robots used in the machine. Both are from Japanese robot manufacturer, Shibaura Machine, formerly known as Toshiba Machine. The first, a TVL700 six-axis robot, is lightweight and vertically articulated, designed to optimise productivity in handling and assembly applications. With a reach of 700mm and a 4 kg payload, it offers exceptional versatility. In the Questt monobloc packaging machine, its speed and accuracy enable efficient box loading and unloading in the workspace. The second robot, a THL400 SCARA robot, has an arm length of 400mm and a payload capacity of up to 5 kg, allowing it to handle varying vial quantities as needed. With cycle times of 47 seconds, it completes tasks swiftly and precisely, meeting the demands of a busy production line.
Boosting productivity with smarter processes
The Questt QPack-1 packaging machine addresses one of the most pressing drawbacks of the manual packaging processes — inconsistent and inefficient throughput. In one production line, the machine was found to be able to package up to 7,200 vials in an hour. When the same process was carried out manually, workers packaged around 2,000 vials in an average working day, highlighting the significant productivity improvement when automating this process.
The QPack-1 also uses cutting-edge pneumatics from Festo and a highly intuitive Siemens programmable logic controller (PLC) to oversee packaging operations. It offers a user-friendly interface and touchscreen capability, enabling easy process adjustments and real-time performance monitoring. The PLC's simplicity streamlines programming, requiring minimal experience to operate the system. Coupled with the machine's relatively straightforward installation and setup, integration into an existing production line is remarkably straightforward, despite the advanced robotics involved.
The Siemens system further enhances process traceability and reliability by using advanced technology to detect errors and respond promptly. Equipped with sensors and cameras, it identifies missing or misplaced products, or faults in the industrial robots. Upon recognising a fault, the system issues a warning and halts production until the operator addresses the issue, immediately allowing potential problems to be recorded for traceability and resolved with minimal downtime or further impact on production.
Production processes in life sciences, pharmaceuticals and veterinary manufacturing are also subject to stringent regulatory frameworks to ensure safety, efficacy and quality of all products. Given the nature of these industries, complete transparency and validation are imperative. The QPack-1 is CE-certified, and additional validation can be conducted to meet required medical industry standards, including Installation Qualification (IQ), Operational Qualification (OQ) and Performance Qualification (PQ), ensuring that the machine operates as intended.
The next generation of packaging systems
To further improve on this offering, Questt is currently developing an advanced solution that builds upon the current capabilities of the QPack-1 packaging machine. At present, the machine loads vials into separately manufactured pre-formed blister packages. Questt’s new machine will integrate packaging production into the same unit for a fully cohesive solution. Through the incorporation of a thermoforming unit, the next iteration of the machine will produce the box, fill it with vials and heat-seal the package, enabling the entire process to be completed in-house. Using a single solution will save time, reduce costs and enhance overall productivity. Additionally, sealing the packages will allow any damage or tampering to be easily detected before distribution.
The limitations of manual packaging in the life sciences industries are evident, but the Questt QPack-1 robotic packaging machine effectively addresses the inefficiencies and inconsistencies associated with manual packaging.
By incorporating industrial robots, advanced technology, and an intuitive PLC, this automated system significantly improves precision, speed and traceability. The solution offers an ideal alternative to manual packaging that not only enhances productivity but also aligns seamlessly with the industry's commitment to quality, safety and compliance.
To find out more about industrial robot systems from TM Robotics and its global distributor network, visit the website here.
The content & opinions in this article are the author’s and do not necessarily represent the views of RoboticsTomorrow
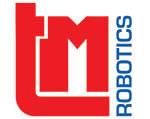
TM Robotics (Americas) Inc
TM Robotics, in partnership with Shibaura Machine, formerly known as Toshiba Machine until 1st April 2020, offers a comprehensive range of industrial robots ideally suited for high-precision assembly, machine loading/unloading and material-handling applications that can be dust proof, clean room, or IP65/67. The company's extensive product line starts with a Cartesian solution available in thousands of combinations from single actuators to four-axis solutions; six-axis solutions that can include precise vision-control; and a complete range of SCARAs from low cost to the industry-leading SCARA with 1200-mm reach that can carry up to 20 kgs. TM Robotics sells and services robots throughout Europe, the Middle East, India, Russia, and Africa, as well as North, Central, and South America, from headquarters in Hertfordshire, England and Elk Grove Village, IL, USA. For more information, visit www.tmrobotics.com or follow us on Twitter, LinkedIn and YouTube.
Other Articles
Giving lens cleaning cloths a robotic hand - Robotic automation for textile processing
Investing in the UK’s injection moulding sector - The case for all-electric machines and robotic integration
Automating pick-and-place in food manufacturing
More about TM Robotics (Americas) Inc
Comments (0)
This post does not have any comments. Be the first to leave a comment below.
Featured Product
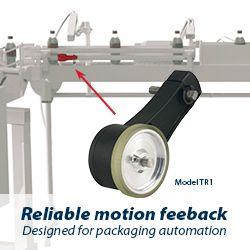