The aim of the MHP study was to demonstrate the advantages of process-integrated charging points using inductive point charging systems such as Wiferion over conventional charging zones using a real-life optimization scenario in a medium-sized production company.
MHP study proves it: Wireless charging increases productivity of AGVs by 50%
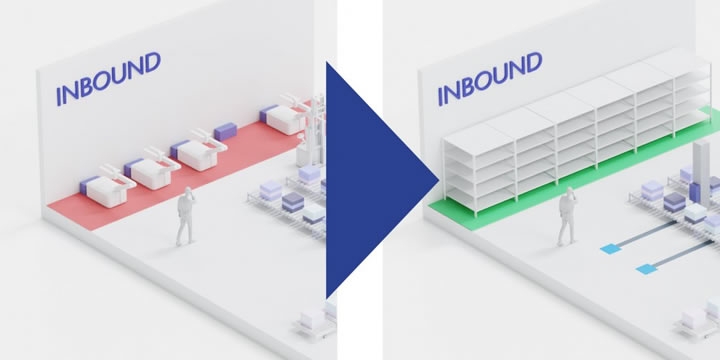
Case Study from | Wiferion
A recent study by MHP – A Porsche Company in collaboration with PohlCon impressively demonstrates how the use of inductive charging can increase the productivity of automated guided vehicles (AGVs) in logistics by up to 50 percent. These results underline the transformative effect of this technology on increasing efficiency in modern production logistics.
Efficiency gains through wireless charging infrastructure
As automation in production logistics progresses, companies are faced with the challenge of maximizing the efficiency of automated guided vehicles (AGVs). Until now, these systems have often been charged in separate charging zones, which leads to unproductive downtimes. The aim of the MHP study was to demonstrate the advantages of process-integrated charging points using inductive point charging systems such as Wiferion over conventional charging zones using a real-life optimization scenario in a medium-sized production company.
in-process charging increased the productivity by 50%
The study compared two charging strategies: a traditional variant with separate charging zones and an innovative method in which charging points were integrated directly into the production process. The result was clear: in-process charging increased the productivity of the AGV fleet by an impressive 50%. A second scenario assumed a constant throughput. Here, the fleet size was reduced by 30%, resulting in significant cost savings.
Significant increase in efficiency
For companies, this means a significant increase in production efficiency, a drastic reduction in operating costs and optimized use of space – decisive competitive advantages in an increasingly automated environment. The simulation showed that in-process charging can save 30 m² of floor space originally blocked by charging areas and convert it into storage space. In the specific case study, a high-bay warehouse with approx. 290 m² of storage space can now be built.
Avoids more than 5,000 hours of downtime
With the introduction of wireless charging technology, companies can reduce their vehicle fleet, optimize the use of their resources and at the same time increase safety in the workplace by minimizing unnecessary traffic and cross-contact. The charging strategy saves 1,300 km of travel each year, avoids more than 5,000 hours of downtime due to charging breaks and prevents 10,900 cross-contacts between employees and vehicles.
“The study by MHP and PohlCon provides convincing evidence that wireless charging is not just a technological gimmick, but a real efficiency driver in modern production logistics,” says Julian Seume, Director of Wiferion – a PULS business unit, commenting the results. “Companies that implement this ground-breaking technology not only secure immediate productivity gains and cost reductions, but also position themselves as pioneers in the next wave of automation.”
At the Mobile Robotics Summit on October 9 and 10, 2024 in Düsseldorf, you can convince you live of the advantages of implementing wireless charging for mobile robot systems in company processes.
The content & opinions in this article are the author’s and do not necessarily represent the views of RoboticsTomorrow
Comments (0)
This post does not have any comments. Be the first to leave a comment below.
Featured Product
