The industry is coming off a record year in sales. It’s likely that we’ll see a small slowdown the remainder of this year due to customer inventories, but it’s expected to be short-lived. Overall shipments since the pandemic have continued to grow.
Industrial Robotics Evolving the Factory Floor
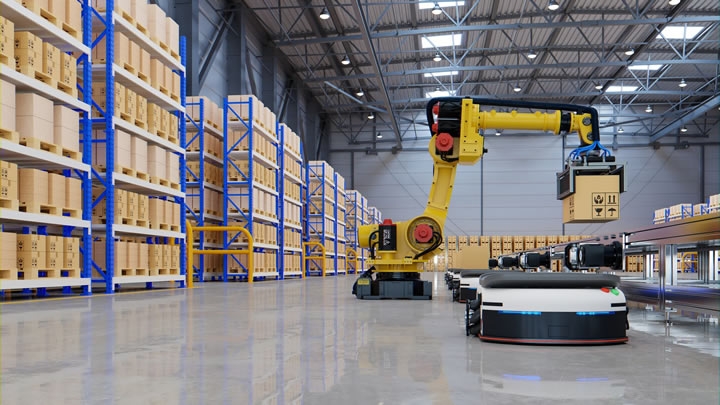
Eric Halvorson, senior marketing technology manager – automation & control, | DigiKey
While robots have been in factories since the 1960s, their roles and capabilities have evolved significantly over the years. Early robots primarily handled tasks like moving objects. Today, robots, especially collaborative robots known as cobots, work alongside humans. They are capable of performing complex tasks and are designed to operate in close proximity to human workers. This collaboration enhances workplace efficiency, safety and productivity, creating a more integrated and effective manufacturing environment.
Since robots were introduced, there has been scepticism about their role. Similarly, during the Industrial Revolution there was a fear of machines taking people’s jobs. While the Industrial Revolution profoundly reshaped the workforce, moving many workers from farms to industrial and manufacturing roles, it did not eliminate the necessity for labour.
We’re now experiencing another shift in roles and responsibilities, this time with cobots working alongside humans. Despite people’s fears, we’re seeing cobots supporting the work of humans and opening doors, not taking away jobs. Today’s cobots can perform menial tasks, allowing a factory worker to take positions that are more complicated, require problem-solving skills, and are overall higher quality. These jobs are usually more fulfilling and come with higher pay.
Continued Market Growth of Robotics
During the COVID-19 pandemic, robots played an important role. When workers couldn’t be on-site, robots maintained production lines and performed tasks that were critical for keeping essential businesses operational. Sales of robots significantly increased, and people learned how to best utilize robotics in factories.
Even though workers are back in factories, today's cobots are working alongside them. Fewer people are pursuing jobs in factories, especially low-skill and low-paying jobs, which creates opportunities for collaboration.
The worldwide manufacturing industry is very competitive, and we’re facing labour shortages, increased competition and strong consumer demand. To help solve these challenges, more European and North American manufacturers have brought robots onto their factory floors. This has also given these manufacturers a competitive advantage. Robots empower factories to achieve a high level of consistency. In a factory, they can ensure a bottle is filled to exact specifications, caps are consistently sealed, and labels are perfectly aligned with precision every single time. With automated programming, concerns over human error affecting consistency or quality are almost entirely eliminated.
Plus, robots don’t require many of the investments that human workers do. For example, robots don’t need to sleep, don’t get sick time or benefits, and are not worn out at the end of a 12-hour shift. All these factors play a role in the overall efficiency we find with robots.
Robots can level the playing field in factories while also creating higher-quality jobs for workers, contributing to the continued market growth.
The Versatility of Cobots and Robots
We’re starting to see many industries utilize robotics, everything from consumer electronics to pharmacy to shipping and logistics. I’m also excited about the potential in the hospitality industry. Cobots are now responsible for everything from flipping burgers at fast-food restaurants to taking orders and delivering food at sit-down establishments to handling housekeeping tasks at hotels. The case uses will continue to expand as cobots become more mainstream.
Part of the reason robots can support so many industries is because of their adaptability. There are seemingly endless ways to configure a robot to make it work for whatever task it needs to perform, just by switching out the end-of-arm tooling (EOAT). One robot can pick up packages, handle delicate fruit or deliver food on a tray, all just by making relatively easy adjustments. Plus, robots can be reprogrammed over and over to keep meeting demands.
Cobots Supporting the Human Workforce
As I’ve mentioned, robots aren’t replacing human labour but rather supporting it. The most common thing I hear is that people are worried robots are taking jobs away from people. With the rise of artificial intelligence (AI), those concerns have intensified. However, there will always be a role for people: the problem solvers, the strategic thinkers, the innovators. These roles will not be replaced by robots but rather supported by them.
While robots have reshaped the job market and somewhat reduced the demand for low-skilled workers, they have also created new opportunities. This includes emerging roles such as robot designers, programmers, and maintenance technicians, again highlighting a shift towards skilled positions and greater opportunities for workers.
One of the best ways cobots can support their human counterparts is in dangerous situations. They are being utilized in sectors where human safety is at risk. By deploying cobots in hazardous environments, we eliminate the need for human exposure to danger. This shift frees up human resources and enhances productivity and safety.
Another example where cobots are being utilized to support their human counterparts is in Amazon warehouses. Cobots transport products directly to pickers, the people responsible for moving products, instead of requiring pickers to retrieve items from shelves manually. This saves time, reduces steps, and minimizes the physical strain associated with heavy lifting. By handling these tasks, cobots help conserve workers' energy and lessen daily wear and tear on their bodies.
Barriers to Bringing Robotics into Factories
Several factors may deter companies from adding cobots or robots into their workforce. These include available space, suitable applications, budget constraints and deciding what type of robot to get all play a role.
For smaller factories and businesses, investing £30,000-45,000-60K in robotics is cost-prohibitive. Although more affordable options are emerging, such as the Igus ReBeL robot, manufactured in Germany and priced around £5,400, cost remains a significant barrier for many.
Additionally, understanding the full spectrum of considerations is a challenge. Automation is complex and programming robots is important in order for them to perform tasks. This creates a need for skilled workers. There is also upkeep and maintenance to consider. Factors like floor space requirements and energy consumption also contribute to the decision-making process.
Safety is paramount when integrating cobots to work alongside humans. Compliance with safety regulations, including those outlined in ISO/TS 15066 for collaborative industrial robots, ensures that robots are introduced into workplaces safely and responsibly.
This is why it’s smart for anyone thinking about robotics to hire an integrator or consultant who can walk them through the entire process, understand the regulations and share realistic budget numbers.
To help overcome the barriers to introducing robotics, DigiKey offers not only the necessary products but also our TechForum, online support, tailored design solutions and an integrator directory on our website.
Mobile vs. Fixed Robots
There are various types of robots tailored to meet specific needs. An integrator can help determine what type of robot makes the most sense. Fixed robots, as their name suggests, remain stationary and are best for tasks such as assembly and inspection. In contrast, mobile robots navigate predefined routes using scanners and LiDAR (Light Detection and Ranging) technology, moving materials around. These robots can handle palletizing, depalletizing and tasks like warehouse garbage collection. Additionally, we're seeing the integration of fixed robots on AMRs (autonomous mobile robots), enabling them to lift items from surfaces and load them onto themselves.
The Future of the Robotics Market
In the next five years, robotics will be a regular part of our daily lives.
Robots' role in manufacturing will continue to expand, and they’ll be able to take on more responsibilities and tasks. The adoption of EOAT robots, equipped with specialized attachments at their extremities, will play an important role in the growth of the market. These robots excel in precise tasks such as gripping, assembly and welding, and can switch attachments based on the specific task at hand.
AI will also expand the use of robots. They will need less programming and be able to do more tasks by learning from experience. AI will enable robots to navigate complex environments and perform complicated tasks more efficiently.
The industry is coming off a record year in sales. It’s likely that we’ll see a small slowdown the remainder of this year due to customer inventories, but it’s expected to be short-lived. Overall shipments since the pandemic have continued to grow. The industry is forecasting a 16 percent compound annual growth rate from 2024 to 2031, with expected growth of nearly $100 billion in revenue.
The potential with robotics is endless, making this an exciting time to be involved in the industry.
Eric Halvorson is a senior marketing technology manager for automation and control at DigiKey. DigiKey is recognized as the global leader and continuous innovator in the cutting-edge commerce distribution of electronic components and automation products worldwide, providing more than 15.6 million components from over 3,000 quality name-brand manufacturers.
The content & opinions in this article are the author’s and do not necessarily represent the views of RoboticsTomorrow
Comments (0)
This post does not have any comments. Be the first to leave a comment below.
Featured Product
