By automatically tracking and monitoring objects and interactions in real-time, RTLS offers unparalleled insights and efficiencies that significantly impact the bottom line. Particularly noteworthy is how RTLS enhances the management and navigation of mobile robots.
Transforming Fleet Management for Mobile Robots with RTLS
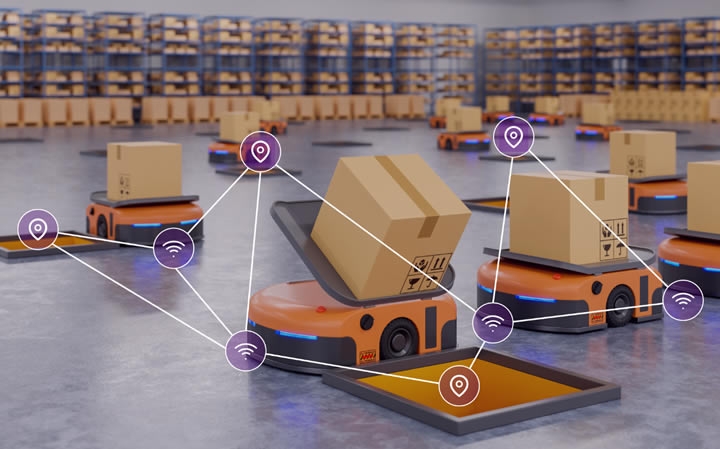
Michelle Schlechtriem | Meili Robots
In the fast-paced world of warehousing and manufacturing, efficiency and accuracy are key to maintaining profitability and competitive advantage. One technology that is rapidly transforming these sectors is Real-Time Location Systems (RTLS). By automatically tracking and monitoring objects and interactions in real-time, RTLS offers unparalleled insights and efficiencies that significantly impact the bottom line. Particularly noteworthy is how RTLS enhances the management and navigation of mobile robots, optimising fleet management systems and revolutionising traffic control within industrial environments.
What Is RTLS?
RTLS leverages a combination of hardware, software, and communication technologies to determine and relay the precise location of tagged assets or personnel within a defined area. This system employs tags that transmit signals to a network of sensors placed throughout the environment. The collected data is processed and displayed, providing real-time visibility of asset locations and movements.
The Impact of RTLS on Mobile Robots
Mobile robots, including automated guided vehicles (AGVs), are increasingly integral to modern manufacturing and warehouse operations. RTLS significantly enhances their capabilities by providing precise, real-time location data, which is crucial for effective fleet management and traffic control.
Optimised Navigation Control
RTLS enables mobile robots to navigate more freely within factories and warehouses. Unlike traditional systems that require pre-programmed routes, RTLS allows robots to dynamically avoid obstacles and optimise their paths on-the-fly. This flexibility not only increases operational efficiency but also enhances the safety of the working environment by reducing the likelihood of collisions.
Enhanced Traffic Control
Managing the movement of multiple robots within a confined space can be challenging. RTLS provides real-time data on the location and movement of each robot, allowing for sophisticated traffic control mechanisms. This ensures smooth and efficient flow of robots, preventing bottlenecks and reducing downtime.
Increased Operational Efficiency
By providing precise location data, RTLS helps streamline the operations of mobile robots. Robots can be directed to the most efficient routes, reducing travel time and energy consumption. This optimisation is particularly beneficial in large warehouses and manufacturing facilities where travel distances can be significant.
Safety and Collision Avoidance
RTLS enhances the safety of mobile robots by enabling advanced collision avoidance systems. Robots can detect and avoid other robots, stationary objects, and even human workers. This not only protects valuable equipment and inventory but also ensures the safety of personnel working alongside these robots.
Benefits of RTLS-Enhanced Fleet Management
A fleet management system equipped with RTLS capabilities is crucial for overseeing the operation of multiple mobile robots. These systems collect and analyse data from RTLS sensors to provide a comprehensive view of robot activities and overall fleet performance.
-
Real-Time Monitoring: Fleet management systems with RTLS provide real-time monitoring of all mobile robots. This enables immediate detection of issues and quick response times, minimising disruptions to operations.
-
Predictive Maintenance: By continuously tracking the performance and condition of robots, RTLS data can be used to predict when maintenance is required, preventing unexpected breakdowns and prolonging the lifespan of the robots.
-
Data-Driven Optimisation: The wealth of data collected by RTLS allows for in-depth analysis and optimisation of robot operations. Fleet managers can identify patterns and trends, making informed decisions to improve efficiency and productivity.
-
Scalability: RTLS makes it easier to scale up operations by adding more robots to the fleet. The system can seamlessly integrate new robots, ensuring they operate efficiently within the existing infrastructure.
Applications and Use Cases
For new users of mobile robots who are unsure how they can adapt Autonomous Mobile Robots (AMRs) to their operations without disrupting current productivity, RTLS offers a seamless solution.
Integrating RTLS with Human-Driven Trucks
By linking RTLS to human-driven trucks through our universal fleet management system Meili FMS, companies can ensure a smooth integration of AMRs into their existing workflows. RTLS technology can track both human-driven forklifts and AMRs, providing a unified view of all movements within the warehouse.
Seamless Coexistence of Manual and Automated Processes
The seamless integration facilitated by Meili FMS and our RTLS partners ensures that manual and automated processes can coexist without hindrance. The system continuously monitors the location and movement patterns of all vehicles, allowing for real-time adjustments to routes and tasks. This dynamic coordination minimises downtime and bottlenecks, ensuring that the introduction of AMRs does not disrupt existing operations.
Gradual Introduction of AMRs
One of the significant advantages of this integration is the ability to introduce AMRs gradually. Companies can start with a few robots, using Meili FMS and RTLS to optimise their movement and ensure they operate efficiently alongside human-driven trucks. Over time, as the system proves its efficiency and reliability, more AMRs can be added without a substantial overhaul of existing processes.
Flexibility and Reliability
The integration of RTLS with human-driven trucks through Meili FMS offers a safety net for companies. In the event of any issues with the AMRs, human drivers can quickly adapt and maintain productivity. This flexibility is crucial for companies that rely on consistent, uninterrupted operations.
Integrating RTLS with human-driven trucks using Meili FMS provides a robust framework for adopting AMRs. It ensures a smooth transition, enhances safety, optimises efficiency, and allows for gradual implementation, all without compromising current productivity. With Meili FMS, companies can confidently navigate the shift towards automation, leveraging real-time data and intelligent fleet management to create a harmonious and efficient warehouse environment.
Enhanced Safety in Warehousing
Leveraging real-time data, Meili FMS and RTLS help optimise routes for both AMRs and forklifts. This means that all vehicles in the warehouse take the most efficient paths, reducing travel time and increasing overall productivity. The ability to monitor and analyse traffic patterns enables continuous improvement — both in terms of efficiency and safety.
As many users of mobile robots may know, forklift accidents and collisions with mobile robots can lead to significant safety concerns and financial losses. Especially for users of large robot fleets with multiple intersections with different types of trucks and robots, traffic jams caused by collisions are not uncommon. By using RTLS, warehouses can enhance the safety protocols for mobile robots, ensuring they operate in safe zones and follow designated paths, reducing the risks of accidents significantly. For instance, if a particular section of the factory floor becomes congested, the system can reroute robots to maintain productivity and prevent delays.
Meili FMS integrates RTLS data to provide precise tracking and real-time adjustments, facilitating better traffic control. This ensures that human-driven and automated vehicles can navigate the same space without interference, significantly enhancing safety. The system's ability to anticipate and prevent potential collisions through continuous monitoring makes the warehouse environment safer for all.
Conclusion
The implementation of RTLS in fleet management systems for mobile robots is a game-changer for warehousing and manufacturing operations. By providing real-time data and optimising navigation and traffic control, RTLS enhances efficiency, safety, and operational flexibility.
At Meili Robots, we are committed to helping our customers achieve these benefits through our universal fleet management system Meili FMS. We have partnered with Wipelot, a leader in RTLS technology, to integrate their state-of-the-art solutions into our platform. This collaboration ensures that our customers can leverage the power of RTLS to enhance their fleet management capabilities.
By combining Meili FMS with Wipelot's RTLS, we provide a comprehensive solution that offers real-time monitoring, predictive maintenance, and data-driven optimisation. This partnership allows us to deliver unparalleled efficiency and safety improvements, enabling our customers to stay ahead in today’s competitive landscape.
For companies looking to achieve operational excellence and long-term success, investing in an RTLS-enhanced fleet management system with Meili Robots and Wipelot is a strategic move. As industries continue to evolve towards smart factories and integrated IoT solutions, our combined expertise and innovative technologies stand out as transformative forces in the field of mobile robot fleet management.
The content & opinions in this article are the author’s and do not necessarily represent the views of RoboticsTomorrow
Comments (0)
This post does not have any comments. Be the first to leave a comment below.
Featured Product
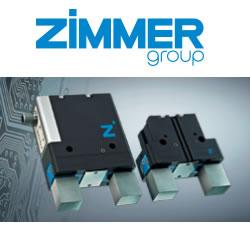