Mecademic’s plug-and-play micro-automation robots are designed for precision applications in areas such as component manufacturing. To give its robots the required sense of touch, Mecademic has focused on perfecting the use of force torque sensors from Bota Systems.
Mecademic robots achieve sense of touch with Bota sensors
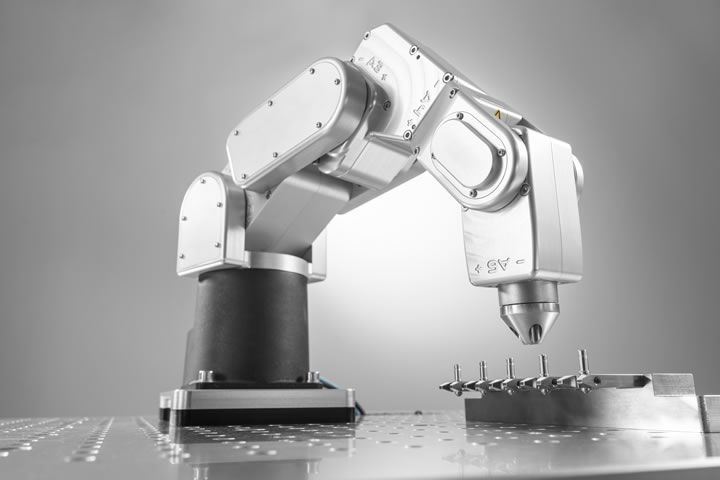
Case Study from | Bota Systems
Human beings have five innate senses that enable them to deal with the environment around them. Interestingly, industrial robots typically rely on just a single sense: sight.
“For most standard robotic applications, ’vision’ is more than sufficient, however, fine precision tasks, such as the assembly of small parts or micro-polishing, require robots to also have a sense of touch,” says Dr. Martin Wermelinger, Head of Robotics at Bota Systems. “The sense of ’touch’ gives robots the haptic feedback needed for complex, delicate jobs.”
This need for a highly accurate sense of touch has been recognised by Mecademic, a Canadian robotics company that designs and builds some of the world’s smallest and most precise industrial robots. Mecademic’s plug-and-play micro-automation robots are designed for precision applications in areas such as component manufacturing, optics and photonics, electronics, and medical devices.
To give its robots the required sense of touch, Mecademic has focused on perfecting the use of force torque sensors from Bota Systems.
Precision applications
Gabriel Boucher, Application Specialist at Mecademic, explains, “Applications requiring force torque sensing are becoming increasingly common across many industries. Initially, the trend started with cobots (collaborative robots), however, our current industrial robot customers want to use force torque sensors because their applications are becoming more and more sophisticated – and because our robots are extremely versatile and can be used to do basically anything imaginable.”
Bota’s sensors are used with Mecademic’s robots in precision applications such as polishing and finishing, for example jewellery diamond polishing. More generally, these sensors find uses wherever there is a changing environment and where items need to be found or contact with them avoided.
Bota’s MiniONE, MiniONE Pro, and Medusa six-axis force torque sensors are installed on Mecademic’s robots, which due to their extremely compact dimensions are a perfect match. Mecademic’s customers frequently also take advantage of the sensors’ EtherCAT communications protocol, further aiding their integration into various production systems.
“Other industries where force torque sensors are finding their niche are watchmaking, optics and electronics assembly applications, where robots need to pick up and place tiny, lightweight, fragile parts,” adds Wermelinger.
Easy to integrate and use
Boucher also has personal experience with force torque sensors from other vendors, commenting, “My issue with sensors from other vendors is that they predominantly utilize external control boxes, whereas Bota has everything, including onboard computing, integrated in a single package and all that is necessary is to hook it up via a single cable to the controller, and you’re set.”
It is very common to see vendors providing force torque sensors that are neatly ‘pre-integrated’ on their robots, which is intuitively quite appealing, however, this approach generally compromises on accuracy. As Boucher adds, “As a rule, an integrated force torque sensor is not going to provide the same level of accuracy as a calibrated external sensor. This improvement in accuracy is a deciding factor wherever metrology plays an important role –when weighing something or measuring a force. Bota Systems also offers calibration certificates for applications where required.”
Mecademic also works with system integrators, such as NEXT robotics and Horosys SA, and both companies regularly design in Bota’s sensors when engineering highly complex systems. NEXT robotics is located in Germany and covers the German speaking countries in Europe, while Horosys SA is located in Switzerland and addresses mainly, but not only, the French speaking customers.
A Bota sensor can be mounted anywhere on the tool, and it is not limited to flanges. “The key takeaway is that Bota’s sensors are easy to integrate, and everything is simple to use, which saves substantial time, both for experienced integrators as well as less advanced users,” says Boucher. “For less experienced clients that simply want to buy a complete robot with a force torque sensor, this ease-of-use factor is a huge benefit, which is further underscored by Bota’s responsive after-sales support and the comprehensive example applications.”
Looking ahead: remote control applications
In regard to future developments, Boucher says that Mecademic is seeing a strong growing trend in collaborative remote-controlled robot systems. This essentially means that instead of automating the entire production process, the customer automates certain parts, whilst allowing a worker to control the robot for others, typically certain final production steps which are too complex or sensitive for reliable automation. “For the worker to effectively control the robot, for example with a joystick, they need precise haptic feedback on the force applied by the robot,” says Boucher. “This requires a force torque sensor.”
“We've had customers who've bought our robots with force torque sensors specifically for these kinds of applications,” says Boucher. “Having force feedback provides next-level control to human workers, who are very good at doing such small assembly tasks precisely because they receive excellent tactile feedback.”
“Presently, we see people carrying out many tasks by hand, for example, working with optical fibres, which is insanely difficult to automate,” says Boucher. “The potential lies in having the robot pick up and place an item into position, and the human operator completing the operation manually.”
Conclusions
“Mecademic’s compact robots utilizing Bota’s sensitive force torque sensors provide customers with precise haptic feedback,” says Wermelinger. “This noticeably improves the speed and accuracy of many challenging production tasks.”
Boucher concludes, “We have used cameras to give robots the sense of sight and now with force torque sensors we are giving them a real sense of touch, bringing them up to an entirely new level of capability.”
The content & opinions in this article are the author’s and do not necessarily represent the views of RoboticsTomorrow
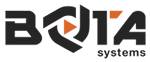
Bota Systems AG
We give robots the sense of touch - Bota Systems' vision is for robots to work and move safely and as naturally and freely as human beings. As a developer and manufacturer of multi-axis force-torque sensors, torque sensors, and custom sensors, we strive to provide the best force-torque sensing solutions and user care experience. Our team of robotics, software and mechanical engineers continually develops highly-integrated and advanced sensors to support a wide range of applications.
Other Articles
Understanding Force Sensors: How They Work and Measure Force
Painting Robots: Benefits, Applications, and Sourcing Tips
More about Bota Systems AG
Comments (0)
This post does not have any comments. Be the first to leave a comment below.
Featured Product
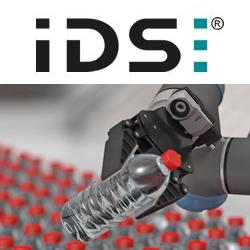