Mobile robots are more than mere devices; they embody intelligence, communication capabilities, and mobility. The primary function is to transport goods, but it operates within the broader context of a business strategy.
Maximizing ROI for Mobile Robots: A Systems Strategy

Thierry Delmas, Managing Director | Kivnon
Increasingly, manufacturers are leveraging compact mobile robots such as AGVs and AMRs to address intralogistics staff shortages, typically seeing a return on investment (ROI) within 6 to 24 months. However, by integrating mobile robots as components of a cohesive production system rather than standalone devices, businesses can maximize the gains at unprecedented levels.
Mobile robots are more than mere devices; they embody intelligence, communication capabilities, and mobility. The primary function is to transport goods, but it operates within the broader context of a business strategy, following precisely programmed sequences that span the entire value chain, including receiving, warehousing, picking, assembly, output, delivery, and more.
Each system is tailor-made, requiring customization for the specific needs of each plant. This is especially true for companies with multiple global locations, as each may have unique technical, mechanical, or regulatory requirements. Tailoring a system necessitates a detailed review of local requirements, how machines communicate with central control stations, with one another, and with other system components and data management applications.
Critical to preserving the benefits of tailor-made operations systems and an overall systems strategy is the adoption of standards. Standards such as those advanced by the International Standards Organization, the American National Standards Institute and the Japanese Ministry of Land, Infrastructure, Transport and Tourism cover many aspects of AGV operation, including electrical connections, fire protection, occupational health and safety, machine safety, and electromagnetism, often within specific industries. Systems adhering to such standards are easier to install, because little or no additional programming is necessary to integrate with other plant systems. Reprogramming is much easier as well.
Empowering the End User
The journey towards systems thinking should begin well before the AGV is shipped. The buyers should discern how much the potential vendor embraces a holistic systems approach. Do they show a comprehensive understanding of the role of intralogistics in your business success? Can they manage regional variations? Are they up to date on IT and communication standards? Are they conversant with navigation technologies?
It contrasts with vendors who see themselves primarily as device builders. Without in-house AGV implementation expertise, you may need to engage a systems integrator specializing in mobile robotics systems.
The vendor must provide a systems perspective, equipping customers with the technology, services, and software necessary for setting up the system for maximum long-term payback worldwide. A consistent training program for the customers helps them to take full ownership of the AGV and its systems and adapt to their evolving business needs independently.
The goal is for customers to quickly scale from managing a single robot to overseeing a fleet, ensuring they are well-prepared through discussions, training, and videos on how the AGV fits within their overall plant systems.
AGVs Don’t Bite
Early adopters might not be comfortable taking too much ownership of their systems. The fear of managing mobile robots due to perceived risks is unfounded; they are designed to be user-friendly and safe to maneuver in their surroundings. Basic operation training can demystify the technology, encouraging hands-on interaction.
By becoming comfortable with maintaining and adapting mobile systems manufacturers can reduce costs and more closely align operations with business strategies. Monitoring and data collection by vendors can further inform on system performance and business impact, supporting continuous improvement and alignment with strategic goals.
Reaping the Benefits
Viewing AGV installations as part of an integrated system rather than isolated devices significantly enhances operational efficiency and strategic effectiveness. The few benefits that we have seen include:
• Integrates with business processes, allowing smoother operation, fewer bottlenecks, and greater alignment with production needs.
• Improves scalability and flexibility, making it easier for the plant to meet production needs that change over time,
• Enriches the data ecosystem, enabling analysis that can optimize routes, improve scheduling, reduce idle times, and predict maintenance needs, thereby increasing overall efficiency and reducing downtime
• Enhances safety and reliability by enforcing safety protocols and reliability measures and encouraging the implementation of comprehensive safety systems that protect both the AGVs and human workers
• Informs AGV deployment decisions, allocating resources cost-effectively
• Integrates with other technologies, such as Warehouse Management Systems (WMS), Enterprise
Resource Planning (ERP) systems, and other automation technologies, streamlining information flows across the enterprise
The automotive industry is probably farthest along the scale of the system, driven in part by just-in-time manufacturing industries. However, food and beverage, retail, and other industries are following suit. Adopting a systems perspective with mobile robots enables organizations to maximize their potential, contributing more effectively to overall business objectives, including reducing costs, speeding turnaround times, improving product quality, and overall customer satisfaction.
Thierry Delmas, in his role as Managing Director at Kivnon, has an outstanding 30-year international track record in key sectors such as robotics, automotive and energy. His collaborative and goal-oriented approach to clients' strategic objectives has led to successful results. With strong expertise in these industries, Delmas stands out as a committed leader in finding innovative solutions to drive business growth and success.
The content & opinions in this article are the author’s and do not necessarily represent the views of RoboticsTomorrow
Comments (0)
This post does not have any comments. Be the first to leave a comment below.
Featured Product
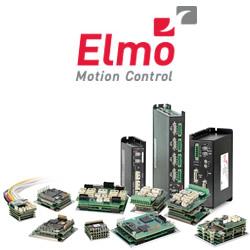