A new type of tool changer now turns the specialist for large series into a flexible all-rounder, with which even small series and individual pieces can be produced economically.
Those who adapt the fastest win.

Article from | Faulhaber
In industry and logistics, robots generally handle monotonous tasks that they can repeat almost endlessly with steady precision. A new type of tool changer now turns the specialist for large series into a flexible all-rounder, with which even small series and individual pieces can be produced economically. The innovative TKX changer series from the IPR specialists features a motor from FAULHABER in the electric drive of the automatic changer.
The range of tasks that is being carried out by robots has become limitless. It includes gripping, holding as well as manipulations such as clamping and screwing through to foaming and welding. And when it comes to standardized mass production, specialized robots can be used, which perform the same tasks day and night. But many processes require flexibility, such as when it comes to batch size 1. This is also important to save on investment costs. The greater the range of tasks that a robot can carry out, the better.
This is where the TKX tool changer comes in. Mounted to the end of the robot arm, it is able to remove a variety of different tools from a rack. For example, it enables the robot to first grip and position a workpiece, then to process it with tools, and finally to check and document the quality with a contour sensor or a camera. For this, the adapter needs suitable feedthroughs for the corresponding tool functions. The TKX series offers all conceivable options here, plus several lateral screw-on surfaces for additional modules. But the main task of the tool changer is to securely lock the tool when it is picked up, and to quickly and consistently release the lock again when it is set down after use.
Pneumatic or electric?
Traditionally, many industrial applications use pneumatic power transmission for this process. Compressed air technology has proven itself over decades, and it is well suited not least for handling very heavy objects. But a pneumatic system requires compressors, lines, and its own control system with numerous mechanical components – a considerable investment in new systems. In industries with increased demands on cleanliness and hygiene, such as microelectronics or food, pneumatics are out of the question in many places because of the unavoidable emission of compressed air. And pneumatics are an absolute no-go in clean rooms.
IPR – Intelligent Peripherals for Robots in Eppingen has seen a significant trend towards the use of electric drives instead of pneumatic ones: "In addition to the hygienic safety, electric motors are much more flexible in use. Unlike compressed air connections, power sockets are available almost anywhere. In newly built industrial plants, pneumatic systems are generally no longer installed. For cobots and smaller robots as well as for decentralized locations, the electric version is almost always the better solution."
The fact that the electric drive is a real alternative to pneumatics today also has something to do with motor technology, explains Roman Batz, development engineer at IPR: "Great strides have been made in recent years. For our applications, we basically need a lot of power with very small dimensions. FAULHABER offers motors that can easily hold their own compared to pneumatic drives."
Open, close, hold
Holding up is also meant quite literally here: The currently most powerful electric model in the TKX series, the TKE 300, is suitable for handling objects weighing up to 300 kilograms. In metal processing, heavy loads such as cast blocks or large forged parts, are handled by robots. The pulling force of their overall mass then acts upon the locking ring in the TKX changer. The torque supplied by the motor in standby mode would actually be enough for safe holding. But to ensure particularly reliable fixation, IPR also installed self-retaining kinematics, which were developed in-house.
A brushless motor from the FAULHABER BXT family provides the driving force for opening, closing, and holding. With its external rotor technology, it achieves a ratio of torque to weight and volume that is unrivalled on the market. This power density is one of the prerequisites for the unique selling point of the new product family from IPR, which Roman Batz describes as follows: "The TKX series are the first tool changers on the market that are available on the same platform with both pneumatic and electric drives – we also have a manual version in the product range. This means that the entire range of accessories can be used with all drive types without retooling. And switching to electric operation is also quite easy. This opens up new possibilities for robotic automation."
Reliable and easy to combine
The TKE changers will be available in seven sizes for handling workpieces from 3 to 300 kilograms. The electric variant of the product family thus covers a wide range of applications, from lightweight robots to stationary applications. The dimensions of the BXT motors used are adapted to the application. "The range of sizes and the large selection of suitable gears for the optimum reduction in each case was an important criterion for us," explains Roman Batz. "Robots should be able to achieve seven-digit cycle numbers without maintenance. So only a brushless motor with the highest possible processing quality can be used. It should be easy to control and manage without additional control – the integrated speed controller takes care of that. Last but not least, the components have to be able to withstand temperatures of up to +80°C."
IPR procures all micromotors from FAULHABER. "We started working together many years ago, long before my time," says the development engineer. In addition to the unique quality of the products, other aspects play an important role for him: "It starts with the very simple design of motor-gear combinations on the FAULHABER website. It takes just a few clicks to get a comprehensive overview. The technical details are very well documented, and when it comes to precisely calculating the finer points – efficiency, power consumption, temperature development over time, etc. – I always get the support I need."
The drive experts from Schönaich
FAULHABER is specialized in the development, production and deployment of high-precision miniaturized and miniature drive systems, servo components and drive electronics with up to 200 watts of output power. This includes putting into effect customer-specific packaged solutions as well as an extensive range of standard products, such as Brushless Motors, DC-Micromotors, Encoders and Motion Controllers. The FAULHABER trademark is recognised worldwide as a symbol of high quality and reliability in complex and demanding application areas, such as medical technology, factory automation, precision optics, telecommunications, aviation and aerospace, and robotics. From the powerful DC-motor with a continuous torque of 200 mNm to the filigree micro drive with an outer diameter of 1.9 mm, the FAULHABER standard range can be combined in more than 25 million different ways to create the optimum drive system for a particular application. At the same time, this technological construction kit is the basis for modifications which allow to configure special versions to meet the specific needs of customers.
www.faulhaber.com
The content & opinions in this article are the author’s and do not necessarily represent the views of RoboticsTomorrow
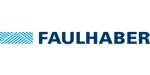
FAULHABER MICROMO
Since 1961, FAULHABER MICROMO has partnered with OEMs to deliver high precision, high performance, custom micro motion system solutions to markets such as medical, robotics and automation in North America. FAULHABER MICROMO's tradition of innovation started decades ago in Germany. The groundbreaking invention of the FAULHABER coreless winding started it all for a market that produces millions of motors today. How can the FAULHABER MICROMO team help you deliver your next innovation to market first? Learn more about MICROMO's solutions for the most demanding applications, our diverse motion products and technologies, online ordering, Engineering and R&D teams, Clean Room Assembly, Machining Center and other services at our Clearwater, FL facility at https://www.faulhaber.com.
Other Articles
Walking naturally with artificial foot
Testing drive systems virtually - Simulink library for development and digital twin.
At least 60 million strokes
More about FAULHABER MICROMO
Comments (0)
This post does not have any comments. Be the first to leave a comment below.
Featured Product
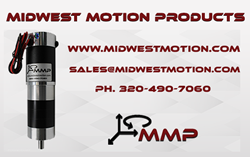