The multi-coupling system helped Eaton cut down on the time needed for switching hoses and connections by almost 40 percent.
Multi-couplings reduce down time and improve efficiency
Case Study from | Staubli Corporation
THE PARTNER
The Eaton Corporation is one of the world’s leading providers of energy management solutions that help customers use electric, hydraulic, and mechanical energy efficiently, safely and sustainably.
APPLICATION
Mold temperature control
The challenge
Eaton’s French headquarters specializes in injection molding to produce plastic components of all forms and surfaces including structures that require millimeter-accuracy for clients in the building construction industry. However, their prior cooling system for their molding machinery required employees to switch couplings one at a time, leading to excessive downtime in the molding process and lost productivity.
The solution
Stäubli presented Eaton with a centralized solution: a multi-couplings module allowing for the simultaneous connecting or disconnecting of 12 hoses at one time. Not only does this apparatus feature a user-friendly lever for quick connecting and clamping to speed up the cooling cycle and increase productivity, but also ensures a guaranteed leak-free connection.
The result
The multi-coupling system helped Eaton cut down on the time needed for switching hoses and connections by almost 40 percent. Since this solution’s implementation, Eaton’s French facility has also seen a decrease in coolant spills – eliminating the need for absorbents, reducing the risk of slips or falls and limiting their need for coolant consumption.
The content & opinions in this article are the author’s and do not necessarily represent the views of RoboticsTomorrow
Comments (0)
This post does not have any comments. Be the first to leave a comment below.
Featured Product
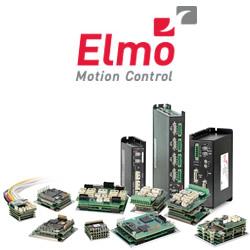