The future of aluminum exoskeleton robot technology holds great promise in the medical rehabilitation industry.
Exploring the Future of Machined Exoskeleton Technology in Medical Rehabilitation
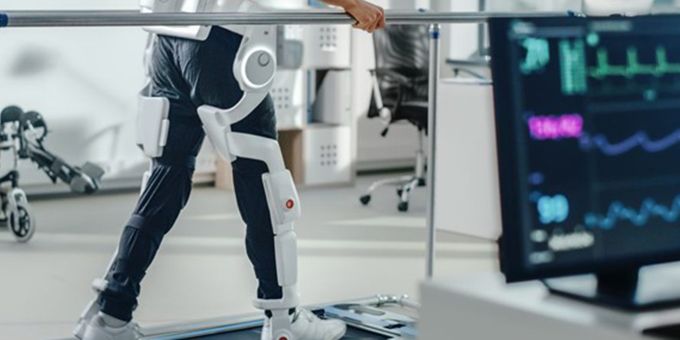
Article from | WAYKEN Rapid Manufacturing
Every year thousands of people suffer from neurological damages due to accidents or other unforeseen events. Many rehabilitation devices are used to tackle this and bring back the patients to the life circle.
The exoskeleton technology is a similar type of solution, which is revolutionizing the medical rehabilitation process in this modern era. In this aluminum exoskeleton robot technology, we have two categorizing differences, one is passive and the other is active. The active approach employs actuators, which convert hydraulic, pneumatic, and electric energy into mechanical movements. However, the passive one is just like an assistant to the user.
These devices are getting popular day by day. Engineers and scientists are working on their designs, materials, and customization so that these devices can be more beneficial and easy to use for the rehabilitation process.
Choosing Appropriate Materials
The selection of suitable materials is the most crucial factor, that will define the overall comfortability, sustainability, and effectiveness of these exoskeleton robots. To make these robots more comfortable in operations the designers are always focused on choosing materials that are lightweight, cost-effective, and comfortable for users.
Most parts that are attached or touched to the body surface of the user are made from silicon, Silicon is a lightweight material, and silicon-molded parts are soft and resemble the skin structure of the human body. Moreover, Nitinol which is a self-adopting composite, is famous for its ability to reform into to predetermined shape upon exposure to specific stimuli. This property makes the exoskeleton robot joints mold themselves into specific shapes as per the anatomical behavior changes.
Graphene which is another quite common material, mostly used in sensors and electronic circuits. The use of graphene in sensors and control units gives more real-time data in rehabilitation exercises so that the AI will improve its response to the movements. Graphene also has good structural integrity, for that reason it will be useful to withstand the repetitive stresses of rehabilitation exercises.
Lastly, strength to weight ratio is the main focus of every engineering design. The designers are tackling it by using carbon fiber-based aluminum alloys. This will not only make the robots lightweight but also perfectly balance the strength to weight ratio so that the exoskeleton does not impose unnecessary strain on the wearer. To attain high structural integrity, finite element analysis and other similar structural analyses were performed to get the best strength to weight ratio.
Ergonomic Design for better Biomechanical compatibility
Human anatomy is a complex thing to understand, as the behavior and the nature of the human response change with age, body weight work stress, and outdoor temperature.
However, a deep understanding of articulated joints can be the key to attaining biomechanical compatibility. With the help of kinematics analysis of body motion, designers meticulously tailor joint angles and degrees of freedom which will be exactly alike the human body movements. With the integration of actuators and motors with the effective proximity of force sensors the engineers will be able to get effective feedback on the body movements of any person.
The engineers and designers are then able to create an exoskeleton machinery that is comfortable for the wearer. This combination of Artificial intelligence and machinery can be able to synchronize the exoskeleton's movements with the user's intended actions.
To make the Ergonomic Design more effective, a futuristic approach is the implementation of Electromyography (EMG) sensors. These sensors can catch the electric pulse motion of the human limb so that the machine responds more quickly to the task. The advanced haptic feedback with this mechanism enhances the user's proprioception and provides him a nuanced sense of their limb's position within its exoskeleton part.
Achieving Better Robotic Assistance
Control assistance in aluminum exoskeleton robots is continuously evolving. These robots are not only assisting patients for rehabilitation purposes but also providing an intuitive collaboration with the user so that they can quest for enhanced mobility and rehabilitation purposes.
To obtain the desired results a critical element is inertial Measurement Units (IMUs) which play a pivotal role, in collecting real-time data on the orientation and acceleration of various body segments. This data is further analyzed based on intricate algorithms, utilizing sensor fusion techniques, so that the engineers can improve user intentions and exoskeleton part response time.
Secondly, the usage of force and pressure sensors in these robots provides a bidirectional communication channel. During the motion of the exoskeleton robots, these sensors judge the force exerted by the exoskeleton and, reciprocally, enable the exoskeleton to sense the user's interactions with their environment. These sensors also equipped with an advanced haptic feedback system which fosters a more intuitive connection between the user and the robotic system.
Keeping this data set in mind if we talk about control systems in these robots, in modern machines, these data sets help to train the machine learning algorithms. Which will empower the exoskeleton to learn and adapt to the individual's unique gait and rehabilitation requirements. This will be a game changer if we talk about providing personalized and effective assistance.
Customization For User Comfortability
The use of Customization and personalization in the aluminum exoskeleton robots provides an intricate engineering solution, that not only helps in the rehabilitation process but also caters to the psychological needs of the patients.
These components are designed as per the anatomy, behavior, and muscular response of the human body. These components are designed such that they can be changed, upgraded, and removed as needed. For instance, changing joints or structural frames with time, or an increase in the weight of the user is something that can be more soothing.
With the implementation of 3D printing technology, the world of customization is revolutionized. The exoskeleton components can be designed, fabricated, and analyzed on precise anatomical dimensions of the user. For instance, the stiffness of specific joints can be tuned such that they perfectly optimize the synergy between the exoskeleton and the user's musculoskeletal system.
The future of aluminum exoskeleton robot technology holds great promise in the medical rehabilitation industry. With the implementation of these technologies and continued enhancement in exogamic designs and material selection, these devices ultimately improve the lifestyle of individuals with mobility impairments.
The content & opinions in this article are the author’s and do not necessarily represent the views of RoboticsTomorrow
Comments (0)
This post does not have any comments. Be the first to leave a comment below.
Featured Product
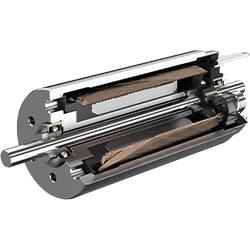