This article aims to dissect the trends within the four major categories of industrial robotics: SCARA robots, collaborative robots (cobots), gantry robots, and articulated robots.
Trends in Industrial Robotics to Watch in 2024

Nthatisi Hlapisi | MacroFab
With 2024 just around the corner, the global industrial robotics market is growing quickly. Market volume is expected to surpass 45 billion USD by 2028, with a growth rate of approximately 3.83 percent annually. In modern manufacturing and automation, this expansion is reshaping the landscape.
In particular, advances in artificial intelligence, machine learning, and sensor technology, along with advances in data analytics, enable robots to perform tasks of increasing complexity and variety.
As robotic technology advances, there is a growing interest in automation, which is being driven by global labor shortages and a need for sustainable manufacturing. Also, the decreasing cost per robot makes automation more accessible and economically viable.
Further, post-COVID-19 and amid geopolitical tensions, countries are boosting investments in robotics to facilitate the reshoring or nearshoring of manufacturing. Together, these elements fuel the growth of the industrial robotics market.
This article aims to dissect the trends within the four major categories of industrial robotics: SCARA robots, collaborative robots (cobots), gantry robots, and articulated robots. Each category, with its unique features and capabilities, is contributing to the overall growth of the industrial robotics sector.
Emerging Trends in SCARA Robotics
Selective Compliance Articulated Robot Arms (SCARA) are high-precision robots that excel at performing fast, repetitive, and exact point-to-point movements. They mainly appear in assembly processes, machine loading tasks, and laser engraving operations.
The market size of SCARA robots is projected to reach over 12 billion US dollars in 2024, underscoring their growing importance in the industrial sector. Trends driving this growth include the following.
SCARA with AI and IoT
Leading the charge in AI advancements are methods like particle swarm optimization (PSO), genetic algorithms (GA), and neural networks. These sophisticated algorithms are revolutionizing how SCARA robots are controlled, offering unprecedented levels of optimization and adaptability.
For instance, particle swarm optimization gives the robot stable convergence characteristics, while neural networks adapt robots to varying conditions by learning from past data and patterns.
Meanwhile, IoT in SCARA robots enhances their interconnectivity and remote control capabilities. Also, IoT-enabled data analysis predicts maintenance needs, reducing downtime.
Emerging Trends in Collaborative Robots
Collaborative robots, often referred to as "cobots," are a type of robot designed to work alongside humans in a shared workspace. They are hailed as part of Industry 5.0 which combines people’s creativity and craftsmanship with the efficiency of robots.
However, their quick movements and the handling of potentially dangerous tools can be a safety concern. This risk becomes even more pronounced during system failures, where the unpredicted behavior of these robots might lead to serious accidents.
Here are some key trends of collaborative robots:
Advancements in Collaborative Robot Safety Features
The industry is witnessing a surge in virtual reality (VR) educational initiatives aimed at fostering safer interactions between humans and cobots. These VR programs simulate real-world scenarios, allowing workers to gain hands-on experience in a risk-free virtual environment.
Furthermore, cobots are advancing in contact avoidance and detection, increasingly employing computer vision and deep learning. These technologies enable them to recognize and navigate around obstacles and co-workers more effectively. By training with datasets of simulated collision scenarios, cobots are learning to predict and prevent potential accidents, enhancing workplace safety.
Wider Adoption in Small and Medium Enterprises (SMEs)
The growing trend of cobots in SMEs is largely due to their distinct advantages over conventional industrial robots. Cobots stand out for their cost-effectiveness and flexibility, making them more accessible and suitable for SMEs.
Moreover, unlike traditional robots, which often require significant capital investment, dedicated spaces, and complex setups, cobots are designed for easy integration into existing production lines.
Additionally, the emergence of lean integrators plays a pivotal role in this trend. These specialists collaborate with SMEs to tailor cobot solutions to their specific requirements. These tailored solutions not only improve operational efficiency but also avoid the need for major capital investments.
Emerging Trends in Gantry Robots
Gantry robots, also known as cartesian or linear robots, typically consist of a rigid framework resembling a gantry. This structure supports linear motion in at least two directions, often on an overhead grid, allowing the robot to cover a large work area.
Expanded Use of Digital Twins with Gantry Robots
A digital twin is a virtual model of a physical system, such as a gantry robot. Integrating digital twins with gantry robots enables real-time monitoring, simulation, and analysis of their performance in a virtual environment. This integration allows for better planning, predictive maintenance, and optimization of robotic operations, making the manufacturing process more efficient and cost-effective.
Emerging Trends in Articulated Robots
Articulated robots are a type of industrial robot that feature rotary joints, allowing them to move with multiple degrees of freedom. This design provides them with a high level of flexibility and precision. One significant trend is closely linked to the rise of the Industrial Internet of Things (IIoT):
Integration with the Industrial Internet of Things (IIoT)
A significant trend in articulated robotics is the integration with IIoT. This convergence allows for enhanced data collection and analysis, leading to improved efficiency, predictive maintenance, and real-time decision-making. Connecting these robots to a network of devices and sensors allows for deeper insights into production processes,
optimizing operations, and minimizing downtime. The marriage of articulated robotics with IIoT technology marks a significant advancement in industrial automation.
Crucial to this integration is the role of sophisticated PCBA manufacturing. PCBAs form the fundamental building blocks within these robotic systems, acting as the electronic backbone enabling complex functionalities.
Increasing robotic complexity has also increased demand for high-precision and highly reliable PCBAs. This symbiotic relationship is a testament to how quality electronic manufacturing drives innovation in robotics.
Cross-Sector Trends
Certain trends transcend the above sub-robotics categories, reflecting broader shifts in the future of robotics across all sectors. Here are some of them:
1. Increased Adoption of Refurbished Robots: Companies are switching to refurbished robots as a cost-effective solution. This trend not only reduces expenses but also promotes a more sustainable approach to industrial automation. Refurbished robots offer similar functionalities as new models but at a fraction of the cost, making advanced technology accessible to a wider range of businesses, including smaller enterprises.
2. Energy Efficiency and Sustainability: There's a growing emphasis on making robots more energy-efficient and eco-friendly. Manufacturers concentrate on designing robots that consume less power by using lightweight materials and
optimizing robot movement. This shift is driven by both environmental concerns and the desire to reduce operational costs in the long term.
3. More Intuitive and User-Friendly Interfaces: The complexity of robotic systems is being counterbalanced by more intuitive and user-friendly interfaces. This evolution makes it easier for a broader range of workers to operate and interact with robots, reducing the barrier to entry and enhancing productivity.
4. Advancements in AI and Self-Learning Robots: AI in robotics is reaching new heights of sophistication, with a notable increase in the use of self-learning robots. These advanced robots can adapt to new tasks and environments, improving efficiency and reducing the need for constant human oversight.
5. Rise of Service Robots: Service robots are broadly classified into commercial and personal categories. Commercial service robots operate in industrial settings, addressing efficiency needs and labor shortages. Personal service robots, used in households, automate tasks like vacuum cleaning. Both categories are gaining traction, reflecting an increased adoption of robotic assistance in various sectors.
Conclusion
Key trends in industrial robotics like IIoT integration, the rise of collaborative robots, and the adoption of AI are reshaping manufacturing and production.
These advancements are steering industries towards smarter, more efficient operations.
For businesses to remain competitive, adapting to these technological changes is essential. These trends are changing the face of industrial automation, signaling a new era of efficiency and innovation.
The content & opinions in this article are the author’s and do not necessarily represent the views of RoboticsTomorrow
Comments (0)
This post does not have any comments. Be the first to leave a comment below.
Featured Product
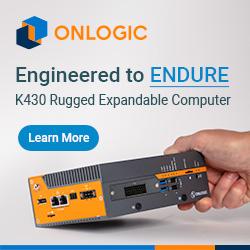