As anyone in the know can tell you, machine tending is incredibly important to the manufacturing process. A well-functioning manufacturing workflow relies on machinery consistently being loaded and unloaded with parts or materials.
Why Letting the Machines Do the Tending Will Open the Door to the Next Industrial Revolution
Daniel Pintar, Global Segment Leader for Machine Tending | Universal Robots
Did you know that the average commercial jet airliner is made up of over 350,000 individual parts? To make these parts, whether metal or plastic, one process is essential: machine tending.
As anyone in the know can tell you, machine tending is incredibly important to the manufacturing process. A well-functioning manufacturing workflow relies on machinery consistently being loaded and unloaded with parts or materials. When done well, machine tending increases productivity and yields – driving down the cost of production over time.
Without machine tending, production would grind to a halt. Advancement in manufacturing will rest on optimizing this crucial task.
The next industrial revolution
Here collaborative automation has a vital role to play. Already integral to Industry 4.0, greater automation of machine tending – more specifically collaborative robotics – will help manufacturers transition to Industry 5.0.
Industry 4.0, or the so-called fourth industrial revolution, saw manufacturers integrating new technologies into their production facilities and throughout their operations. Industry 5.0 builds on this, using R&D to transition to a more sustainable, human-centric and resilient industry.
The European Commission sees Industry 5.0 as playing a vital role in providing solutions to challenges for society, including the preservation of resources and climate change.
The future of manufacturing and the transition to Industry 5.0 rests on ensuring machine tending benefits from both human skill and automated consistency, something collaborative robots (cobots) are specifically designed for.
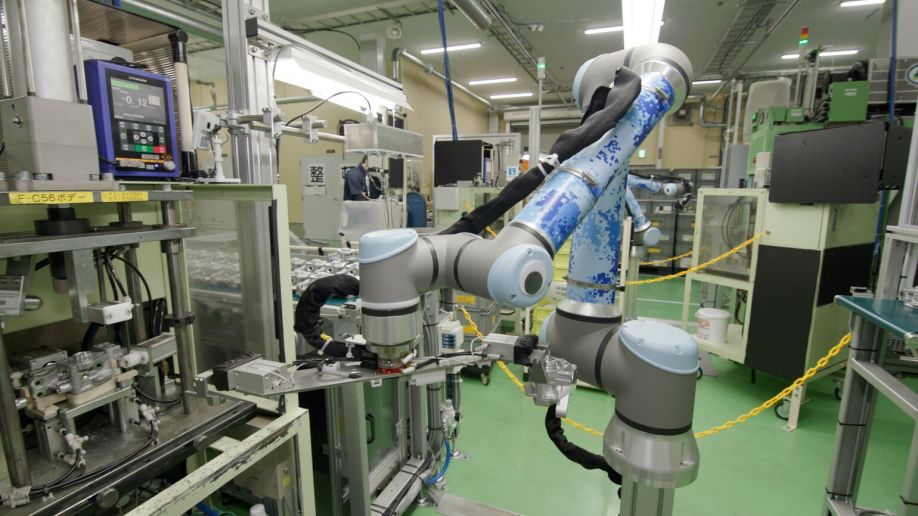
Working alongside the machines
For decades, the repetitive and physically demanding task of machine tending has been performed by human machine operators. This must change. Not only can manual machine tending be unsafe, but it is also not scalable.
Machine tending tasks are often performed in small working spaces, involving aggressive cutting fluids and sharp edges. Often providing the perfect recipe for worker accidents. In addition, these tasks, performed for hours on end, with little natural light, also take a mental strain. Due to these less than favourable conditions, few people are clamouring to do this type of work.
Using collaborative robots – or cobots – for machine tending applications can help to solve these issues. Cobots can be programmed to reduce contact in a defined space, enabling them to work seamlessly alongside humans and new generation cobots can effectively perform the extremely precise work required in machine tending. Offering up to six degrees of movement – and in some cases seven – cobots have the “human touch” necessary.
In some cases, automation of machine tending is already enabling real-time monitoring and analysis for manufacturers, as well as predictive maintenance and remote operation, improving overall efficiency, productivity, and profitability.
There are countless examples of businesses that improved their productivity thanks to automating vital parts of their manufacturing processes. Japanese automotive OEM Aido Industry has doubled its productivity in three years and Bernacki Industrial Services has successfully reduced the cost of man-hour production per precision part it produces.
In addition, we’re also seeing AI being applied inside the machines. By analysing data from sensors and other sources, plant operators can identify patterns and trends to help improve efficiency and reduce downtime.
Improvements across the board
We know that human cognitive power and analytical capabilities remain irreplaceable. However, collaborative automation will help manufacturers to meet the demands for greater mass personalisation and hyper-customisation. Automation in machine tending will allow greater flexibility for more adaptable production in a parametric and generative design.
With cobots able to take over the tedious machine tending tasks, workers are freed to do more valuable and rewarding tasks. At the same time we see a possibility of longer machine tending shifts, as minimal human supervision is needed. This could mean the growth of 24/7 factories, as manufacturers obtain a consistent source of output with factory downtime being practically wiped out. For regions battling low growth and productivity the notion of non-stop factories is an attractive one.
Matthew Thompson, Commercial Manager, Cobots Online, has seen first-hand how cobots can revolutionise the way smaller UK manufacturers approach machine tending: “It’s often a given that huge companies will have automation, but as an integrator of cobots, our passion lies in making automation accessible for all. This means unlocking the benefits of automation for those who didn’t even think it was an option. Cobots are perfect for machine tending. They’re adaptable and flexible, meaning they can perform various tasks effectively and affordably. This technology is key to keeping regional manufacturers competitive and in business, especially when talent is scarce.”
The next industrial step forward will rest on a greater collaboration between people and machines. Applying this approach to machine tending will help to build a sustainable and resilient manufacturing sector. Not only will this improve the working lives of those employed in factories, by enabling them to focus on higher-value tasks, it will also help companies to optimise their operations and expand production.
The type of collaborative automation that can transform machine tending is vital for the transition to Industry 5.0. Without it, many manufacturing businesses risk being left behind.
The content & opinions in this article are the author’s and do not necessarily represent the views of RoboticsTomorrow
Comments (0)
This post does not have any comments. Be the first to leave a comment below.
Featured Product
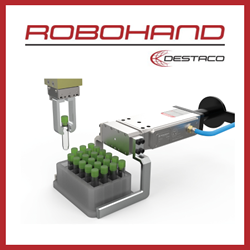