Forvia, one of the world’s leading automotive manufacturers, completes a successful AGV installation at its factory in Paraná, Brazil.
Kivnon AGVs Drive Efficiency for Forvia

Thierry Delmas, Managing Director | Kivnon
Automated guided vehicles (AGVs) are rapidly becoming adopted in industries around the world. With heavy parts to transport, the automotive sector is an ideal setting for their use. AGVs offer many benefits, including enhanced safety, lower risk of human error, reduced risk of injury, and increased efficiency and productivity through 24/7 operations. As Forvia learned, selecting a simple and reliable solution is the easiest path to achieving automation goals.
At its Paraná factory, Forvia used manually driven tractors to move parts on trolleys from its warehouse to production lines. In its quest to increase safety by removing all forklifts and tractors from its production areas and to ensure it kept pace with the market by adopting new technology, it looked to an AGV solution for its inbound material logistics processes. It selected two heavy-duty Kivnon K11P trolley transporters.
Application
The plant had to transport the necessary “inbound” parts to one of four aisles for various production process steps. The automotive parts that can weigh up to 1.6t need to be located in the correct location of the warehouse, manually attached to a tractor, and driven to the respective aisle.
Challenges
With heavy materials and busy production lines, transporting parts to the right areas was becoming complicated. The tractors were also operating in areas where personnel were working, which presented a safety risk.
Forvia had previously embarked on an AGV installation but found that the machines were too complex and operated at the limits of their load specification. The result was less than a reliable system requiring frequent resetting and constant intervention from operators. Unsurprisingly, the team at Forvia was tentative about trying other AGV options.
Forvia’s pathway to a better AGV experience
Forvia was naturally skeptical based on its previous experiences. A proof of concept was required, and a trial was implemented for testing the K11P AGV using a demonstration model, and employees were informed of the new system and the benefits, making it clear that AGVs were there to support their work rather than replace workers.
Following the AGV installation on site, the complete application was commissioned to prove its capability as an efficient, versatile, and robust solution for transporting heavy loads. The trial was highly successful and resulted in Forvia acquiring more new AGVs for its plant.
The final installed solution
“The automotive sector is committed to automation, and Forvia is always seeking to implement best practices,” comments Thomaz De Aquino Macedo, PC&L Manager Quatro Barras.”
The two new AGVs were installed and tested in the “inbound” logistics area over two weeks, with engineers working around Forvia’s production schedule. Personnel in the warehouse prepare trolleys and a conveyor train ready for transportation. They select which aisle the AGV needs to deliver to and prepare another train in a different area while one of the AGVs carries out its mission. Following installation, the system was fine-tuned, and the AGV supplier advised of recommendations to improve the safety and efficiency of the inbound logistics process.
Luciano Citelli, PC&L Improvement at the plant, says, “With the implementation of this new technology, we aspire to improve safety and optimize the logistics process. We are always considering only the best for the staff and our facility.”
The installed AGVs are designed to handle heavy loads (up to 3t) and for safety and simplicity. They use line-following navigation and automatically stop if a person or obstacle is in the way. It takes around 10 minutes for the parts to reach the production lines from the moment they are ordered, which helps optimize productivity.
“Working daily with the AGVs is a very straightforward and practical thing,” advises Taimo Luiz Cordeiro Fracaro, one of Forvia’s logistics operators. “The materials arrive at the chain swiftly, preventing the tug driver from being overloaded.”
The personnel at the plant in Paraná are pleased with the way the AGV system is operating and are intending to look at other areas where they can automate logistics processes.
“The purpose of the AGV system is to improve our manufacturing process,” concludes De Aquino Macedo. “Going forward, we intend to implement such systems in other logistics areas.”
The content & opinions in this article are the author’s and do not necessarily represent the views of RoboticsTomorrow
Comments (0)
This post does not have any comments. Be the first to leave a comment below.
Featured Product
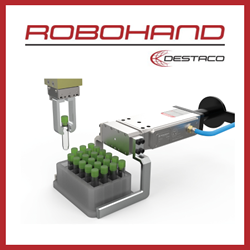