Competitive intralogistics requires extensive automation, something that is inconceivable without micromotors. Drive systems from FAULHABER prove their ability to perform here during sorting, transporting and with robotics solutions.
Drives for Speed in Intralogistics

Article from | Faulhaber
Suitable transport structures in intralogistics are a prerequisite in all industries in order to be able to withstand competitive pressure in the future. An increasing number of work steps involved in storing items in warehouses as well as retrieving these items and preparing them for dispatch are being taken over by automatic storage and retrieval machines, driverless transport systems and intelligent logistics robots. To speed up the processes, flexible systems that work reliably around the clock are needed here. Such logistics solutions are often driven by high-performance micromotors.
The demands that modern intralogistics place on the used drives are high: In many instances, they must be capable of releasing tremendous forces under extremely confined conditions, also work reliably in continuous or stop-and-go operation, and oftentimes they must also perform highly precise positioning tasks. The speed also plays an important role, after all, many thousand orders need to be processed every day in large warehouses. Drive systems from FAULHABER have often demonstrated their performance here during sorting and transporting as well as with storage and retrieval. Thanks to their modular design, the motors can be combined with a variety of high-resolution encoders for precise positioning tasks and with high-performance gearheads for high torque requirements. There are also compact motion controllers that can either be integrated in the drives or arranged externally.
Powerful handling with finesse
Autonomously driving and self-contained logistics robots are a critical component of "Intralogistics 4.0". They are used both for storage as well as removal and dispatch preparation. They optimize material flow, relieve employees and replace, e.g., conventional lift trucks or pallet trucks. Autonomous picking robots that allow individual objects to be precisely accessed are one example. A typical picking robot comprises a lifting column and gripper. As a drive unit, it contains, e.g., BX4 series brushless DC-servomotors with integrated motion controller and planetary gearhead. When used in the gripper, this combination ensures precise positioning during storage or retrieval – all during continuous operation with constant load changes.
Yet the complete drive unit weighs only about 300 grams. This means that no counterweight is required even when the gripper is fully extended. With a diameter of only 32 mm and a length of 85.4 mm, the brushless DC-servomotors are also very compact. This makes it possible to design the gripper very flat, allowing it to also pick up packages that are stored just above ground. Expensive storage areas can thus be optimally used. Thanks to the brushless commutation system, the motors are long-lasting and reliable. They deliver high torques and, with the balanced rotor, are very quiet running. With the integrated current control, the torque demands are limited and the drive is reliably protected against overload.
Compact drives for rapid start/stop operation
Graphite-commutated DC micromotors of the CXR series combined with matched gearheads have also proven themselves in handling tasks. Their commutation system is very robust and is especially well suited for dynamic, high-performance applications with fast start/stop operation as is required in many handling systems as well as with automatic sorting, e.g., in cases where switches are used to change routes on transport paths.
Thanks to their linear characteristics, the DC motors are also easy to control. Combined with high-resolution encoders, this makes them ideal for precise positioning tasks. High-quality neodymium magnets and the proven Faulhaber winding ensure a high power density in a compact design. They can thereby be installed directly in the handling elements. In spite of their small size, they can lift considerable weights there.
Flexible through production
Automated guided vehicles (AGV) are the means of choice when it comes to ensuring flexible transport in production processes. Among the most important requirements for the used drives with in-house material transport systems are availability, speed, flexibility and – often – low space requirements. The current consumption also plays a role in ensuring that the battery of the vehicles is as long lasting as possible. For example, brushless DC-servomotors of the BP4 series are suitable to drive the wheels, whereby the motor power can be transferred to the wheels via planetary gearheads and drive belts. The motors operate with high efficiency: their innovative winding technology allows for a high copper content and keeps losses to a minimum thanks to high winding symmetry.
Encoders of the IE3-1024 series are built right onto the servomotors for precise position detection. The magnetic incremental encoders, which are available with different resolutions, feature an indexing channel for referencing a revolution of the drive shaft as well as a standardized, electronic encoder interface. The resolution, direction of rotation, index width, and index position can be flexibly adapted to the application. A motion controller controls the servomotors. Such drive systems are also used for mobile robot platforms, which move about completely autonomously in industrial halls without a preinstalled guidance system. Above all, their high power density is particularly evident in the wheel modules.
A lot of power in a very small space
If there is limited installation space for wheel drives in the axial direction, the high-torque flat motors of the BXT series are often an option. Thanks to innovative winding technology and an optimised design, the motors are just 14, 16 and 21 mm in length but deliver torques up to 134 mNm, within a diameter of 22, 32 and 42 mm respectively. For precise speed control or in the case of high requirements on positioning accuracy, diameter-compliant magnetic encoders or speed controllers are now fully integrated into the housed motor variants, whereby the drive is increased by just 6.2 mm. Speed control is performed by the digital Hall sensors integrated in the motors. Thus, a wide speed range from 200 rpm to 10,000 min -1 is available. The compact drive combination is ideal for space-critical applications and simplifies installation and commissioning. The matching metal planetary gearheads of the GPT series too are characterised by a short design, high torque and extremely fine graduations of the numerous reduction ratios.
You can find further information on this topic at: www.faulhaber.com/logistics-robot/en
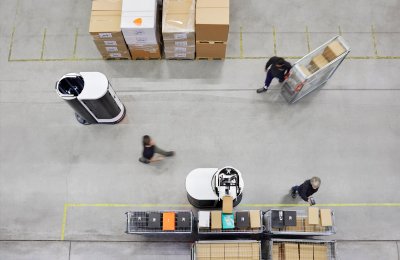
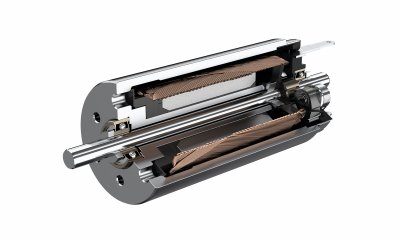
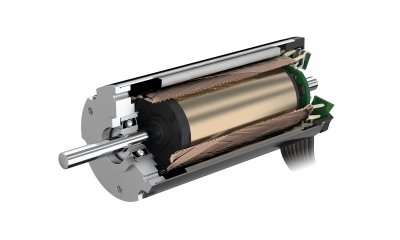
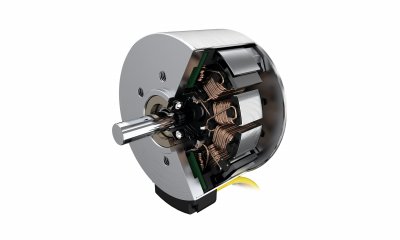
FAULHABER is specialized in the development, production and deployment of high-precision miniaturized and miniature drive systems, servo components and drive electronics with up to 200 watts of output power. This includes putting into effect customer-specific packaged solutions as well as an extensive range of standard products, such as Brushless Motors, DC-Micromotors, Encoders and Motion Controllers. The FAULHABER trademark is recognised worldwide as a symbol of high quality and reliability in complex and demanding application areas, such as medical technology, factory automation, precision optics, telecommunications, aviation and aerospace, and robotics. From the powerful DC-motor with a continuous torque of 200 mNm to the filigree micro drive with an outer diameter of 1.9 mm, the FAULHABER standard range can be combined in more than 25 million different ways to create the optimum drive system for a particular application. At the same time, this technological construction kit is the basis for modifications which allow to configure special versions to meet the specific needs of customers.
The content & opinions in this article are the author’s and do not necessarily represent the views of RoboticsTomorrow
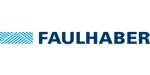
FAULHABER MICROMO
Since 1961, FAULHABER MICROMO has partnered with OEMs to deliver high precision, high performance, custom micro motion system solutions to markets such as medical, robotics and automation in North America. FAULHABER MICROMO's tradition of innovation started decades ago in Germany. The groundbreaking invention of the FAULHABER coreless winding started it all for a market that produces millions of motors today. How can the FAULHABER MICROMO team help you deliver your next innovation to market first? Learn more about MICROMO's solutions for the most demanding applications, our diverse motion products and technologies, online ordering, Engineering and R&D teams, Clean Room Assembly, Machining Center and other services at our Clearwater, FL facility at https://www.faulhaber.com.
Other Articles
Walking naturally with artificial foot
Testing drive systems virtually - Simulink library for development and digital twin.
At least 60 million strokes
More about FAULHABER MICROMO
Comments (0)
This post does not have any comments. Be the first to leave a comment below.
Featured Product
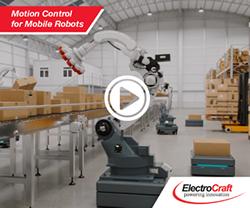