Drone technology continues to advance depending on specific applications. For this article, we’ll be looking at compact drones used in a variety of applications that need continuous and autonomous inspection of chimneys, shafts, and tanks.
Article from | maxon precision motors inc
Flybotix was founded in 2019 by engineers who have worked in robotics and drone technology for many years. Cofounders Samir Bouabdallah and Alexandre Cherpillod have been following the development of drone technology and based their products on the need for indoor inspection. Their goal is for the operation to cost as little as possible when it comes to human safety as well as down time of the process.
Flybotix ASIO drone is suitable for confined-space inspection in a wide variety of industries including sewer management, hydro power plants, oil & gas, and chemical plants. Samir Bouabdallah has worked in drone technology for over twenty years and finds that the field continues to be challenging and exciting.
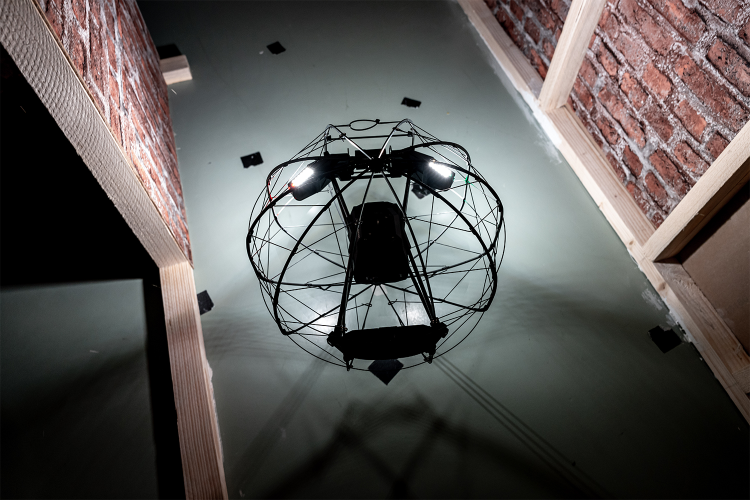
In the early 2000’s, Lithium Polymer batteries became readily available, which provided electric drones with a much longer flight-time, making them more practical for real world missions. Roughly at the same period, the community transitioned from brushed to brushless DC motors, for which the higher torque and increased reliability were key to the popularity of quadcopter designs. Once the stabilization problem of quadrotors was solved, the community moved to GPS-based position control, then quickly to vision-based navigation.
With the acceleration of technology, there are always advancements that can be used to innovate next generation devices. When Flybotix decided to focus on in-house, tight location flight, they found that quadcopters were not going to work. The smaller the footprint, the less stable the craft. This led them to consider other options. They decided on a helicopter approach where only two rotors are needed, allowing them to decrease the size and the weight of the craft while increasing its stability.
Next Generation Challenges
Critical to the industrial market today is the drive toward digitization and integration. Products for industrial use are needing to have an increased number of sensors of varying types to better detail inspection data for analysis.
As industrial applications continue to broaden, reliability and robustness in a wider field of environments also becomes a critical factor. Drones need to have their own lighting system, camera system, and sensor base while maintaining stability and a long flight time. Add to these future forward capabilities the addition of artificial intelligence to create a fully autonomous device, and the challenges can quickly multiply.
The Impact on Flybotix
Flybotix continues to upgrade its drone, exploring ways to integrate the electronics as well as keep their drone safe under difficult conditions. The more complex the system gets, the more it has to have the right interfaces with the electronics onboard. Presently, the Flybotix ASIO lightweight drone uses a patented propulsion system to carry an oblique lighting system, a true 4K, 12-megapixel camera, and a radiometric infrared imagery system. The system has an extended flight time of up to 24 minutes—one of the most important specifications of an inspection drone.
Artificial intelligence will continue to play an increased role in navigation, reducing the need for human intervention. Along with AI, miniaturization will continue to allow the company to make inroads into a broader range of applications than ever before. The ability to autonomously fly in and around machinery whether packaging and production or high-speed assembly systems is expected to change the inspection capabilities of many companies.
Suppliers play a very important role in the availability of components and services. Reliable suppliers must be able to guarantee more than just product delivery, but must guarantee high quality with regard to products, processes, and pertinent certification. A complete indoor inspection system consists of ASIO Explore post-processing software, the ASIO Flight application, and the ASIO Drone.
Precision Motor Collaboration
Partnerships with the right companies are key to any advancement in technology and the ASIO Flybotix drone is no different. When looking for the right motors for the drone, they were unable to find the best solution through a search for off-the-shelf motors. This was particularly true for the high-performance motors they needed for the rotors of the ASIO drone.
Flybotix decided to work with maxon to help in developing the best motor for the ASIO project where they would provide a motor that addressed the specific needs of the project, as well as future innovations as they were developed. maxon is involved with the EPFL (based in Lausanne, Switzerland), one of the major universities in Europe whose mission includes education, research and innovation. As part of the innovation lab, maxon is able to open themselves to new concepts, new projects, and new markets, expanding their potential and expertise in the industry.
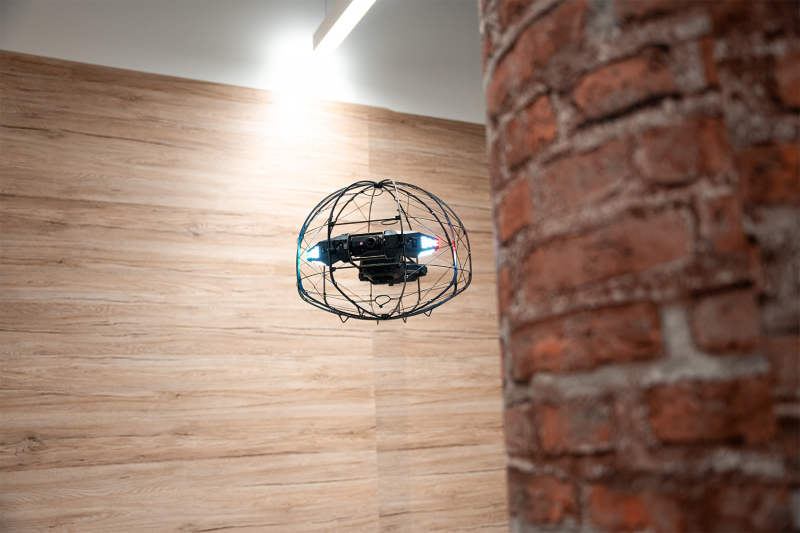
The content & opinions in this article are the author’s and do not necessarily represent the views of RoboticsTomorrow
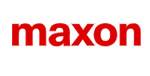
maxon group
maxon is a leading supplier of high-precision DC brush and brushless servo motors and drives. These motors range in size from 4 - 90 mm and are available up to 500 watts. We combine electric motors, gears and DC motor controls into high-precision, intelligent drive systems that can be custom-made to fit the specific needs of customer applications.
Other Articles
Automate 2025 Q&A with maxon group
Understanding Torque and Speed in Electric Motors
How Parvalux Is Helping to Develop the Next Generation of Conveyor Systems
More about maxon group
Comments (0)
This post does not have any comments. Be the first to leave a comment below.
Featured Product
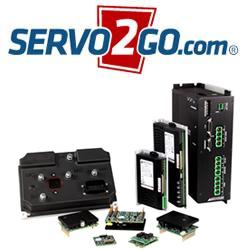