Optical components play a key role in the optimal performance of today’s cobots, allowing them to see and respond to their environment in real-time and ensuring that they operate safely and effectively.
What is a Cobot? Bridging the Gap Between Robots and Humans
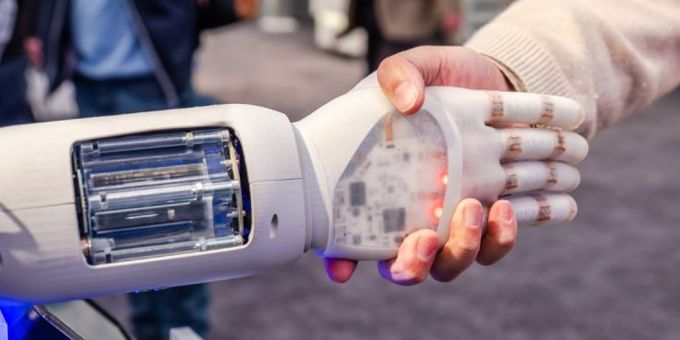
Article from | Knight Optical
As we reflect on history, we can observe numerous systems with resemblances to robots. In fact, some concepts of robotics and artificial intelligence (AI) are speculated to date back to ancient times. The resourceful Ancient Greeks, for instance, created sophisticated automated puppet theatres1, while the Ancient Egyptians devised ingenious mechanical operating systems embodied in figurines2. Fast-forwarding to the present era, significant progress has been made since the days of Ancient Greece and Egypt. Nevertheless, it is evident that the fundamental mechanics of some contemporary systems bear similarities to those of antiquity.
What stands out is the recurring feature among these ‘robots’ – their ability to imitate human movements, expressions, and behaviour, with the goal of aiding us. As technology has progressed, the mimicking of these robots has become increasingly lifelike, with some even resembling and conversing like humans. Although some of them are colossal industrial structures confined within securely fenced areas, there has been a new trend in robotics that involves humans and robots collaborating as partners, known as cobots.
What Is a Cobot?
Collaborative robots, more commonly referred to as cobots, operate in conjunction with humans to perform tasks. By working alongside humans, cobots facilitate the completion of tasks in a more efficient and rapid manner, and their usage can prevent errors typically caused by human mistakes, thereby enabling companies to expedite their processes.
What’s The Difference Between a Robot and a Cobot?
In addition to the difference previously mentioned, where industrial robots typically operate behind barriers or in cages to prevent harm to humans, cobots and robots also vary in terms of their degree of autonomy.
For example, many traditional robots are often programmed to operate independently, carrying out a specific set of tasks in a highly controlled environment. Cobots, on the other hand, are designed to be more flexible and adaptable to changes in their environment. They are often equipped with sensors that allow them to detect the presence of humans so that they can adjust their behaviour accordingly. For instance, if a human worker approaches a cobot while in operation, the cobot might slow down or stop moving altogether to avoid any collisions.
Another difference between the two lies in their level of complexity. Robots can be highly specialised and require much more technical expertise to programme and operate. On the other hand, cobots are designed to be more user friendly and accessible to a broader range of users.
Overall, the main distinction between robots and cobots is that robots are typically designed to operate independently, while cobots are designed to work collaboratively with human workers in a shared workspace.
Industries: What is a Cobot used for?
Thanks to all these benefits and their increasingly profitable versatility, cobots are being widely adopted by many sectors throughout the globe.
These include:
Manufacturing: to perform repetitive or hazardous tasks, such as assembly, painting and packaging, for example
- Healthcare: for healthcare for tasks such as dispensing medication and delivering food and supplies to patients
- Agriculture: here, they can be used for harvesting, planting, and spraying
- Logistics: for jobs such as palletising, sorting, and transporting goods
- Food and beverage: for packaging, quality control, and mixing
- Retail: to restock shelves and assist customers
- Construction: for bricklaying and painting.
The Future of Cobots
According to IDTechEx, the use of cobots is set to rise in material-handling and automotive sectors3. As the technology company explains, many automotive companies are turning to cobots due to the typical, expensive downtime associated with traditional robots. According to IDTechEx’s findings, “An automotive manufacturer’s downtime cost per hour could be more than US $2m per factory”. Cobots offer these companies the opportunities to minimise downtime and provide safer side-by-side operation in an often smaller, more flexible manner.
Putting Theory into Practice
Numerous reports in 2023 have revealed the extensive utilisation of cobots in manufacturing settings. One notable instance showcases the use of cobots for repetitive screw-driving tasks. Catherine Leclerc, a representative from Robotiq Inc – a company specialising in cobot solutions and Plug&Play components – spoke to Assembly magazine, stating that cobots have become indispensable in this field because of labour shortages and frequent employee turnover4. She elaborated on how cobots enable manufacturers to access automation solutions without requiring excessive space on the production line.
Cobot adoption is further evidenced by recent news of a partnership between two prominent robotics companies. Rapid Robotics and Universal Robots (UR) are collaborating to increase the deployment of cobots to North American customers. UR, a Danish cobot manufacturer, will supply Rapid Robotics with collaborative robot arms to create cobot work cells. The partnership will leverage the strengths of both companies, including UR’s rapid shipment record5 and Rapid Robotics’ advanced AI and vision systems, to pave the way for a promising future of high-performance cobots.
How Are Optical Components Used in Cobots?
Optical components play a key role in the optimal performance of today’s cobots, allowing them to see and respond to their environment in real-time and ensuring that they operate safely and effectively.
Here, optics are employed for several typical roles, such as for:
- Cameras: to provide visual feedback to the control system, allowing it to see and respond to its environment. Here, they can also be used for quality control and inspection tasks.
- Lenses: used to focus light and can be found in cameras, laser sensors, and other optical systems within cobots. Different types of lenses are used depending on the specific application of the cobot in question.
- Laser sensors: use laser beams to detect the distance, position, or shape of objects in the cobot’s environment. They are often used for precision positioning and navigation.
- Light curtains: utilise a series of light beams to create a so-called curtain that detects when an object or person enters a defined area. They are normally used as part of a cobot’s sought-after safety feature to prevent collisions with humans.
- Projectors: used to display visual information, such as work instructions or safety warnings, to the cobot operator.
Why Choose Knight Optical for your Application?
Discerning customers rely on Knight Optical not only for the premium quality of our output and in-house state-of-the-art Metrology Laboratory and QA Department’s capabilities but because – as well as a range of Stock Optics (available for next-day dispatch) – we also offer our optics as Custom-Made Components.
With over three decades’ experience under our belt and a host of long-standing world-renowned customers on our books, we are proud to have worked on some of the most ground-breaking innovations.
FOOTNOTES
- https://www.nature.com/articles/d41586-018-05773-y
- https://egyptindependent.com/ancient-egyptians-invented-first-robot-4000-years-ago-study/
- https://www.idtechex.com/en/research-article/cobots-on-the-rise-for-the-automotive-and-material-handling-industries/28754
- https://www.assemblymag.com/articles/97577-screwdriving-with-cobots
The content & opinions in this article are the author’s and do not necessarily represent the views of RoboticsTomorrow
Comments (0)
This post does not have any comments. Be the first to leave a comment below.
Featured Product
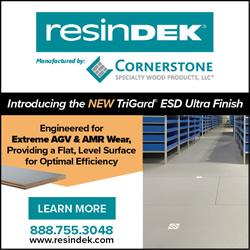