Motus Labs was built around the concept of innovation in the robotic gear solutions space, & we’re constantly looking for ways to improve the customer experience and the performance of our robotic gears. This idea is even further supported by our recent gear solution design.
The Innovation Behind the Orbital Flex™ Design Gear Solution
Article from | Motus Labs
THE ORBITAL FLEX™ DESIGN GEAR SOLUTION ORIGIN STORY
The idea of the Orbital Flex™ Design was born the way most ideas at Motus Labs are – through listening to the needs of our clients. We had heard time and time again that our clients wanted gears with:
- Zero backlash
- Low noise
- High torque density
- Flexibility in the materials
They also wanted these features to not interfere with the robotic gear’s performance. While these desired specifications may have seemed like a tall order for a team of engineers, Motus Labs was up for the challenge.
One day the idea, for what is now called the Orbital Flex™ Design (OFD), popped into the head of our Chief Technology Officer, Carlos Hoefken, and like any good brainstorm, it was quickly drawn onto a napkin to avoid being forgotten. He wanted to prioritize making a better performing, simpler gear solution design with less noise while utilizing existing components and machine elements. He had come up with exactly how to do that! Once the design was solidified, prototypes were made and testing began.
THE DESIGN
OFD is a patented design that will provide a high torque, zero backlash gear solution. The technology utilizes the concept of a mismatched outer and inner ring which forces it to create a ratio that leads to inertia, torque and speed advantages. The OFD bearing flexes on a compliance flexure and allows the cup (the inner gear part) to mesh with the outer gear part. As it goes around there are less teeth on the inner than the outer which is what forces the ratio.
Think of it almost like a little cone sitting inside of a larger cone. The points meet while the parts rotate and the mutating part of that design goes through the flexible component. The compliance flexure allows a flexible cup to orbit around the ring.
Having a compliance flexure is what allows the cup to do the flexing around the ring. That’s an important part of the gear motion technology because by putting this reduction in place, the torque can be wrapped up while also allowing for better speed and control.
Bringing a rigid cup and compliance flexure into the design instead of a flexible cup is what allows for the zero backlash benefit. This is different from other technologies because the compliance flexure allows the rigid cup to have more strength. The compliance flexure then becomes the limiting factor on life and torque as opposed to the cup or bearings.
THE BENEFITS OF THE ORBITAL FLEX DESIGN FOR OUR ROBOTICS CLIENTS
The benefits of the OFD were mostly driven by the needs of our robotic gears market. The most common requests were for a gear solution that was low to zero backlash as that is an important element of precision in use cases.
Next, we wanted to be sure we could increase the torque. Our goal in our current development is to move the needle to create twenty to thirty percent more torque density.
Another important feature of the OFD is the way in which it changes the methodology of its life. Where the failure point used to be the bearings, it’s now the compliance flexure. Determining the life and flexibility of the compliance flexure is a simpler process, which allows us to do more rigorous testing to extend life.
The content & opinions in this article are the author’s and do not necessarily represent the views of RoboticsTomorrow
Comments (0)
This post does not have any comments. Be the first to leave a comment below.
Featured Product
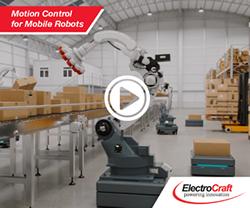