The system uses motors from the FAULHABER CR series, which has graphite commutation, a very robust type of commutation suited to high power applications. The motors also feature extremely powerful neodymium magnets and a high copper content rotor, delivering supreme power.
How Micromotors Are Helping Eliminate Inefficiency in EV Charging
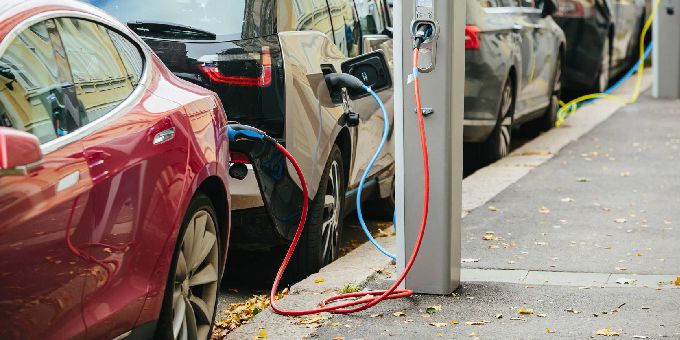
Stewart Goulding, Managing Director | EMS
According to Zap-Map, there were more than 1,135,000 plug-in electric and hybrid vehicles on UK roads as of January 2023. As the ban on new diesel engines approaches, we’ll soon all be swapping gas for electricity. But bulky cables and charging infrastructure could cause a nuisance on our streets. So, should we start exploring other electric vehicle (EV) charging options? Here, Stewart Goulding managing director of planetary gearhead supplier EMS, explores the role drive systems could play in EV charging.
To keep up with rising numbers of EVs on our roads, more charging stations must be integrated into infrastructure. In fact, in 2022 the Government pledged £1.6 billion in order to reach a target of 300,000 public EV charging points by 2030. But charging stations in city centres can be an eyesore, and long cables can be a trip hazard on pavements and in people’s garages. So, what are the options?
Contactless charging
Contactless inductive charging offers one solution to the typical visual and mechanical annoyances of charging. The wireless charging technique involves a transmitter coil embedded in the garage floor or road surface, and a receiver coil in the bottom of the vehicle. Electricity from the grid runs through the transmitter coil, which generates a magnetic field. The magnetic field then induces current in the receiving coil, thus charging the vehicle’s battery.
However, even contactless charging comes with disadvantages. In order to embed the coils in the floor, the ground has to be opened up and then refinished, causing inconvenience and visual defects. In addition, without a wire to transfer the power, the maximum output is currently around three kilowatts (kW) in most cases, resulting in long charging times. Furthermore, a significant portion of the power is lost during charging compared to plug-in cables, and this is magnified if the car is not parked precisely over the coil.
An automated solution
Fortunately, it is possible to avoid both the annoyance of long cables and the inefficiency of contactless charging. Instead, a small, sleek and flat charging structure can be fixed onto the floor. The structure can be as little as six centimetres (cm) high, providing an inconspicuous solution.
Similar to contactless charging, the vehicle must be parked over the charging structure, but its position doesn’t need to be as exact. This is because a retractable, automated arm then extends out of the structure with a connector placed at the end, which seeks its counterpart on the car’s underbody.
The two components seek and connect by exchanging information via encrypted wireless communication. An ultrasonic system ensures the arm accurately finds its target. Within less than 15 seconds, the connection is established.
The connector is a conical-round current carrier, and can therefore make full contact even if the car is not parked in the optimal position. As long as the connector is within a range of 50 centimetres squared (cm2), the car can be parked at any angle and still get connected. The technology can handle up to 100 kW direct current (DC), making charging time just one hour.
Perfecting the system
The system uses motors from the FAULHABER CR series, which has graphite commutation, a very robust type of commutation suited to high power applications. The motors also feature extremely powerful neodymium magnets and a high copper content rotor, delivering supreme power.
EMS is the sole UK supplier of FAULHABER motors, and also has a selection of complementary planetary gearheads available. Adding a planetary gearhead reduces the motor speed and increases the torque, making the motor run at a higher and more efficient revolutions per minute (rpm).
The electric car market is growing rapidly, but charging difficulties are limiting its potential. Automated charging techniques avoid the inconvenience of bulky cables in typical plug in methods and the inefficiency of contactless charging, therefore helping to accelerate EV adoption.
The content & opinions in this article are the author’s and do not necessarily represent the views of RoboticsTomorrow
Comments (0)
This post does not have any comments. Be the first to leave a comment below.
Featured Product
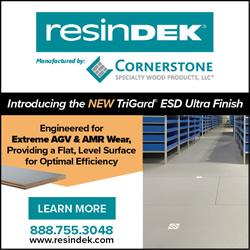