As a relatively new addition to site operations, standards and data on AGV safety are still developing, but some AGV manufacturers are going above and beyond the minimum requirements to help ensure accident-free operations.
Forklift Safety: AGVs to the Rescue
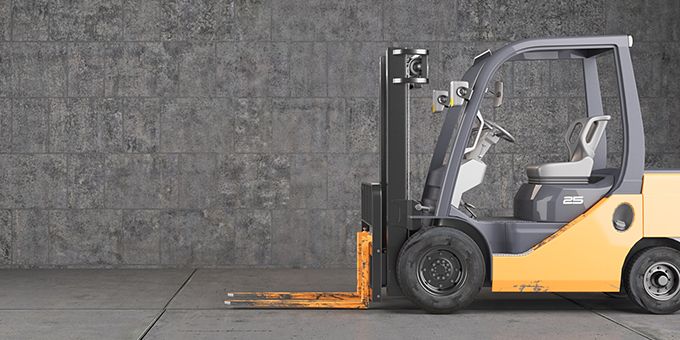
Jaume Martinez, Country Manager | Kivnon USA
In the USA, forklifts were the source of 70 work-related deaths in 2021 and 7,290 nonfatal injuries involving days away from work in 2020. Most fatalities are caused by being crushed by a forklift, either as it falls, possibly due to an unstable load or driver error, or between the forklift and a hard surface or another forklift. Other safety concerns for manual operations include fatigue increasing risk of human error, and injury from improper or repetitive lifting.
The number of forklift-related incidents is a worry for companies and comes with a significant price tag and loss of productivity. Indeed, incidents can lead to damaged products, reduced employee productivity, fines, penalties, and increased insurance costs. However, using automated guided vehicles (AGVs) in forklift applications is proving to offer a much safer alternative and one that has other benefits over and above enhancing safety.
As a relatively new addition to site operations, standards and data on AGV safety are still developing, but some AGV manufacturers are going above and beyond the minimum requirements to help ensure accident-free operations.
Beyond safety
Before delving deeper into forklift AGV safety, let’s first consider the other benefits these machines offer in many industries, including warehousing, manufacturing, retail, and food & beverage applications. The primary reason most companies look to invest in AGVs is productivity. AGVs can operate 24/7, do not tire or make mistakes, and provide a significant uplift in the efficiency of a site’s intralogistics. They never call in sick, suffer from repetitive strain injuries, and do not present recruitment issues. They carry out mundane and laborious tasks and free personnel to carry out more value-add tasks for the business. Indeed, their benefits and return on investment can make a real difference to a company’s operations.
Ensuring safety
Regulations (and, common sense) demand that AGVs include safety sensors and devices to avoid and proactively prevent safety incidents. Safety sensors detect if a person, other vehicles, or an obstacle is on the AGVs path. For forklifts, however, safety measures should go much further. Some of the big risks to a forklift’s operations include unstable loads and errors within the process or a vehicle that is overly complex for the required task, increasing the risk of human errors.
An incorrectly positioned load may fall resulting in damaged goods, risks to personnel, and even the possibility of the vehicle toppling over. It makes sense, therefore, to add additional sensors around the forks and lifting area. These can provide data about whether the load is positioned correctly, and whether it is safe to proceed with the mission. As well as providing alerts about any problems, data can also be collected and analyzed to understand any underlying issues with the lifting process and identify any corrective actions that will increase operational safety.
It is critical that the type of AGV selected is suitable for the process and loads it will handle, but it should be simple to operate. Although many AGVs are available with various ‘bells and whistles’, more complex vehicles require a higher level of operator skills and training. Selecting only the necessary functions and specifications to meet the application needs will make it easier for operators and, with less to go wrong, increase the reliability of the AGV. Of course, it will also mean a more economical solution.
Make more use of data
Data from AGVs can provide deeper insights into operations. Alongside alerts and information about potential issues during an operation, collecting and analyzing data from the AGV will help identify where vehicles are slowing or stopping more frequently, reducing overall operational efficiency. Managers can then identify why these issues are occurring and take action to optimize process steps.
Summary: Greater safety does not mean you need to spend more on your AGV
The number of AGVs being used in forklift applications is rapidly increasing because of the benefits they offer in terms of safety, efficiency, and reliability. However, if you are looking to embark on an AGV project, take the time to understand exactly what your process needs (and what it doesn’t) and look for a solution that has been designed from the outset with safety in mind. Additional safety features, such as load sensors, should not be optional for forklift applications but, beyond this, vehicles that are robust, simple to operate, and based on a core, proven standard design will offer better value for money and increased reliability. If different options from the ‘standard’ are required, these can be added on – but make sure you are not paying for something you do not need that will unnecessarily complicate your project. Ultimately, a simple and robust AGV will enhance safety, reduce the risk of errors, keep operations running smoother, and provide a faster return on investment.
About Jaume Martinez
Jaume Martinez is Country Manager at Kivnon USA, an industrial engineer, and MBA with extensive experience in Automation. He started his career as an international sales engineer, helping automate some of the biggest car plants in Europe.
The content & opinions in this article are the author’s and do not necessarily represent the views of RoboticsTomorrow
Comments (0)
This post does not have any comments. Be the first to leave a comment below.
Featured Product
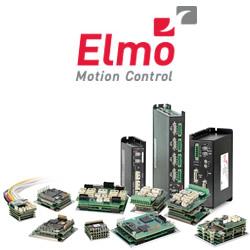