Currently in the Písek location, 14 MiR robots are deployed. 7 of them, heavy duty MiR robots, mainly MiR600s, work in the area of finished goods, bringing empty pallets to the assembly lines and picking up full pallets to the logistics area.
FORVIA

Case Study from | Mobile Industrial Robots - MiR
FORVIA Faurecia is a global leader in the automotive technology industry. With 266 industrial sites, 39 R&D centres and 114,000 employees in 35 countries, Faurecia is a top ten global automotive supplier. As one of the manufacturing facilities in the Czech Republic, Faurecia Clean Mobility Písek focuses on exhaust systems production for a wide range of customers, mainly Volvo, Daimler and PSA. The site in Písek has been in operation since 2006 and currently employs around 500 people.
In order to continually increase its competitiveness, Faurecia Clean Mobility has been running different digital projects, including installations of mobile robots technology in logistics operations. Besides Písek, the mobile robots technology has been implemented also on other production sites in the Czech Republic, France, Italy and Portugal.
Issue & solution
Before the project has been initiated, the logistics on the shop floor relied mostly on manual processes, forklifts and stackers equipment, without any automation. As the matter of fact, a risk of human injuries or industrial diseases has been quite high, and the company decided to automate the most heavy and dangerous processes. The principal goal was to bring technology that increases both a level of safety and productivity.
There was a number of other requirements, an important condition for selection of the right vendor was its global presence, as the automatization and digitalization project in Forvia runs over the world. Complexity of the autonomous technology was another convincing point, including wi-fi connectivity, independent mapping and fleet software, all providing big opportunities for automation. And finally the level of service and maintenance provided from Mobile Industrial Robots, which is standardly very high.
MiR robots for 24/7 automated workflows
Currently in the Písek location, 14 MiR robots are deployed. 7 of them, heavy duty MiR robots, mainly MiR600s, work in the area of finished goods, bringing empty pallets to the assembly lines and picking up full pallets to the logistics area. The second area, where MiR250 robots operate, is supplement of components from warehouse to assembly lines. The robots in the plant work 24 hours a day, 7 days a week, covering all three shifts operation.
One of the most challenging applications was handling monoliths that are brought from warehouse to assembly lines with karakuri top module ensuring full automaton of unloading that helps to reduce routine work content on the line and increase productivity. When the robot unloads monoliths in the production, it automatically picks up waste materials simultaneously. Another highly specific application connected to the company’s digitalization efforts is cooperation of robots with a strapping machine, where robots stop on the way from assembly line to finished goods logistics area.
MiR Fleet software is used to organize missions and together with using internal script helps to optimize the logistics flow to the lines and between the lines. All the communication with doors, gates, the strapping machine etc. is fully automatic without any need of operators’ assistance. A target for the next year is to integrate MiRFleet into the company’s ERP system.
Benefits
Easy to use, easy to program
When people started to work with robots, they needed to learn how to cooperate and quickly understood a way they help them with everyday workload. In the beginning, it was quite new and hard to imagine for them to operate robots. Anyway, they quickly adopted to actively use robots to get all tasks done.
“We are now operating 14 robots in everyday use,” said Benjamin Paillusson, PC&L Improvement Leader in Faurecia Clean Mobility Písek. “As any other automation technology, it needs some supervision, anyway operation of MiR robots is very smooth and fully autonomous. From time to time, we just need to bring an improvement, but basically the technology does not need any human intervention.”
Instead of heavy tasks with manual loading and unloading materials and finished goods, employees on the shop floor can now focus on more valuable activities like supervision, being in the production, or programming robots. “The MiR interface is really user friendly, the way of building mission is very easy made through building blocks instead of code lines. Thus, it is understandable enough even for people without previous programming experience,” added Benjamin.
Return on investment less than 2 years
MiR mobile robots provide the customer with full autonomy enabling to easily set up new routes without additional magnetic tapes or other external guidance necessary for using other intralogistic technologies. The MiR robots and people can work well together, as robots are smart and can recognize people on the shop floor and they can stop or bypass people, which are around without decreasing the robots’ efficiency because the robot avoids bottlenecks..
“Mobile robots help us to bring more discipline to the shop floor and make our production processes more stable and reliable, especially important is stability for operating all three shifts. What we appreciate most on robots is their autonomy, meaning they move freely on the shop floor without any specifically needed equipment,” added Martin Horáček.
General benefits of deploying MiR mobile robots span into three main areas. The first is improved safety by eliminating forklifts on the shop floor. The second one is increased productivity in all areas of operations. And last but not least, it is return on investment into MiR robots: in Faurecia Písek the payback was less than 2 years.
“Our next automation plans are quite ambitious, as there are new locations to deploy MiR robots next year. In 2023, another big complex project here in Pisek called “Warehouse 4.0” is planned that fully automate materials flow from warehouse to production and from production to warehouse. Once completed, it will secure components delivery from warehouse to all 16 production lines by 10 MiR robots,” concluded Martin Horáček.
The content & opinions in this article are the author’s and do not necessarily represent the views of RoboticsTomorrow
Comments (0)
This post does not have any comments. Be the first to leave a comment below.
Featured Product
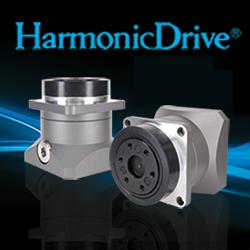