Leveraging advanced technology and robotics to scale operations and focus employees on complex or specialized activities while improving safety and increasing operational efficiency.
BP is Improving Safety and Efficiency by Using Robotics to Inspect Offshore Sites Remotely
Case Study from | Formant
In 2020, BP set out to reach net-zero emissions by the year 2050 while simultaneously boosting employee safety and operational efficiency. BP is committed to leveraging advanced technology and robotics to find new ways to remove employees from potentially hazardous situations and improve the efficiencies of remote locations.
The challenge
Utilizing people’s strengths and augmenting their experience with the robot’s capabilities.
Optimizing the resources deployed to offshore sites and maximizing each site visit is key to improving operational efficiency and reducing the carbon footprint. To do this, BP needed to offload some of the mundane tasks of onsite employees and more effectively analyze data collected during inspections and investigations, ensuring that they were prepared with the parts and expertise needed when an onsite visit was required.
Free employees from dangerous tasks
The simplest tasks, conducting rounds or analyzing a leak in a hard-to-reach location, are inherently more complicated on an offshore rig. Leveraging robotic technology to remove some of the danger from mundane tasks or conduct more in-depth investigations can dramatically improve the safety of employees.
Identifying problems and abnormalities earlier
Though human senses are powerful, leveraging advanced technology, you can extend the ordinary senses to include detecting gasses, collecting thermal and infrared readings, and so much more. This adds valuable insight and a level of consistency that aids in predicting and proactively responding to possible failures.
Improve the efficiency of remote sites
Having basic diagnostics and issue details before being deployed to the site empowers operators to come prepared with the tools and expertise they need. This requires access to review inspection footage and analyze all data collected remotely, so they have as much information as possible prior to arriving.
The solution
Scale operations by leveraging onsite robots to conduct routine inspections and centralizing the expertise needed to review and respond to the findings.
BP combined the mobility and dexterity of Boston Dynamics’ Spot with Formant’s command center software to enable the organization to centralize its operations and allow experts to monitor many remote sites effectively. Operators can now remotely operate Spot and review and analyze the site data in context as if the expert was onsite even though they are hundreds or thousands of miles away. Using Formant to remotely command and control Spot has provided BP a way to consistently collect more environmental data and identify failures earlier, resulting in increased employee efficiency, improved safety, and a reduced number of onsite visits required.
Remote command and control of Spot
The Formant data and operations platform allowed BP to maximize the value of their investment in Spot by removing the need to have an employee directly operate it from just a few feet away. Formant remote operations also provided BP with economies of scale, allowing one operator to inspect and manage robots in a number of locations. The operator can control the PTZ camera on Spot to zoom in and read gauges, inspect corrosion, and inspect and quantify potential leaks. Formant also collects the data from additional sensors added to Spot, like methane levels, providing a comprehensive view of the environment and providing valuable contextual data to assist in diagnosing and remediating issues found.
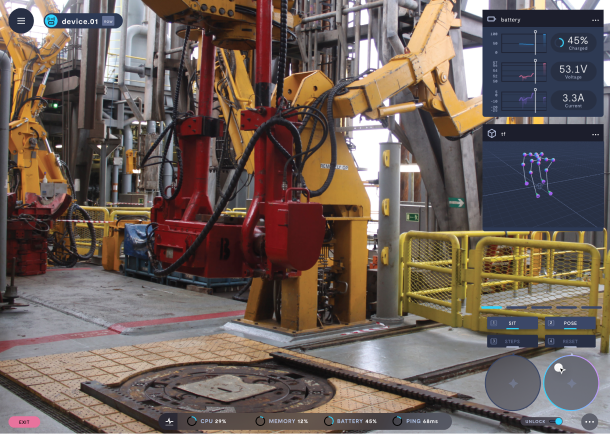
Remote collection and review of data
Centralizing domain expertise while having access to detailed inspection data from many remote sites provides BP a new level of operational efficiency. BP uses Formant to collect, consolidate, and visualize all the data obtained during an inspection in a single dashboard. Formant ingests the robot telemetry, video, audio, as well as any data that comes from additional sensors mounted on Spot, such as methane detectors, thermal, infrared, ultraviolet, and hyperspectral data. Viewing all data feeds together, in context, enables operators to compare data that would not normally be contained in a single location. Formant’s timeline navigation provides a simple and easy way to review and dive into particular moments of interest, even tagging an event to share with team members.
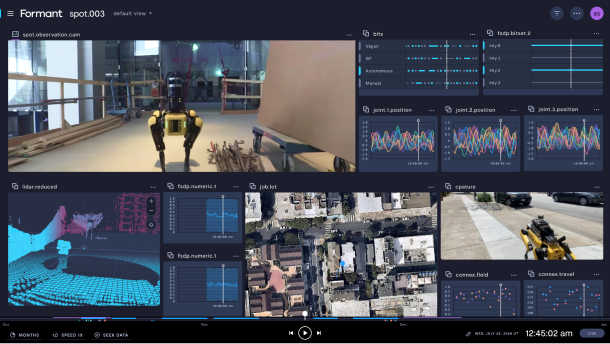
Remotely diagnose and optimize onsite visits
A critical aspect of BPs solution is the ability to remotely review inspection and investigation data collected to proactively diagnostics and root-cause issues and events. Having all inspection data available for remote review empowers the operations team to be as prepared as possible prior to arriving on site. They can ensure they bring any parts or expertise required to address the issues. By having this data before they initially deploy, they are eliminating steps, and possibly multiple onsite visits, that add to the costs and carbon footprint to maintaining these offshore sites.
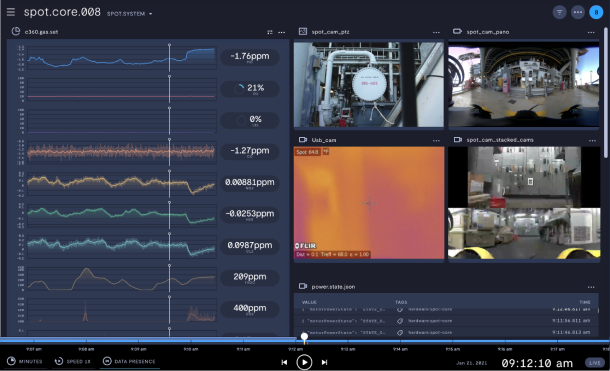
The outcome
Using onsite robots to conduct routine investigations allowed BP to centralize the expertise to review and analyze the findings - improving efficiency and reducing operational costs.
Organizations with remote or dangerous sites can leverage robotics to conduct routine site inspections or investigate issues in a scalable and cost-effective way. Robots can collect a wider variety of metrics and feed the data, video, and sensor readings to a centralized location where experts can easily review the data from multiple sites. Formant allows organizations to optimize onsite and centralized resources while minimizing the costs associated with unnecessary onsite visits.
The content & opinions in this article are the author’s and do not necessarily represent the views of RoboticsTomorrow
Comments (0)
This post does not have any comments. Be the first to leave a comment below.
Featured Product

Robotmaster® 2024
Program multi-robot cells and automatically solve robotic errors with ease. Hypertherm Associates announces a new version to its robotic programming software. Robotmaster 2024 addresses key market trends including the support for programming multiple robots in a single work cell and the demand for automatic trajectory optimization and robotic error correction.