As the existing robotic automation could only handle boxes of consistent size and with certain conditions, there was a limit to realize full automation in reality. It stems from the fact that the robot could not take boxes of irregular sizes.
Random Depalletization
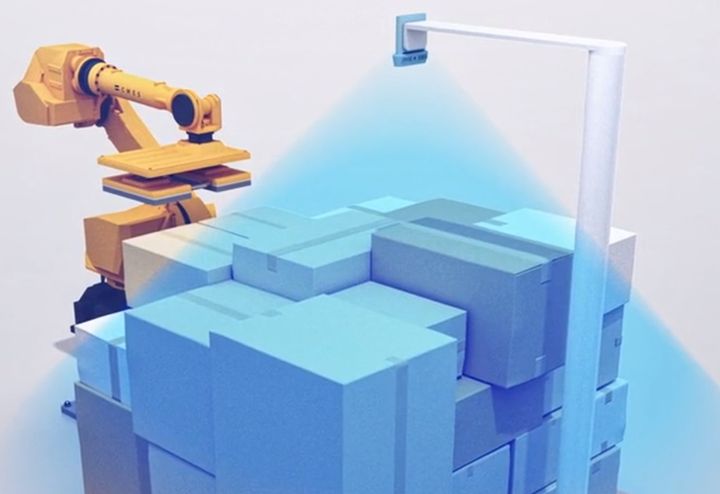
Case Study from | CMES Robotics Inc.
Korea's e-commerce industry has grown by 250% in the last eight years, and the total market size is expected to reach 120 billion dollars as of 2020. The gross revenue of top e-commerce groups in 2020 increased by more than 45% on average compared to the previous year. In particular, online consumption compared to offline has multiplied because of the COVID-19 pandemic, so e-commerce orders in the first quarter of this year increased by more than 50% compared to the same period last year.
Meanwhile, e-commerce companies are struggling to come up with a way to handle orders that have risen sharply to over 130,000 per day. It is because the pandemic not only requires strict prevention management of the working environment but also limits the density of the workforce on the shop floor. Also, high staff turnover is occurring due to the repetitive labor of moving heavy products in the distribution center. To solve this problem, the need for robot automation emerged to tackle efficient workforce assignment and unloading of the warehoused product boxes in areas of high staff turnover, and CMES participated in this project.
CHALLENGE
The first process of the e-commerce distribution center starts with the process of putting product boxes received from various suppliers into the distribution center in the form of pallets. The operator moves the product boxes on the pallet to the conveyor belt. At this time, the product boxes are not uniform in size, the position on the pallet is not regular, and there are a lot of boxes that are heavier than 10 kg.
“Currently, conveyor belts are responsible for transporting products from one process to another, but the majority of the other work, especially the handling of millions of boxes of goods of varying weight and shape, is often done by humans.” explains Operation Manager of a logistics company, one of our clients.
As the existing robotic automation could only handle boxes of consistent size and with certain conditions, there was a limit to realize full automation in reality. It stems from the fact that the robot could not take boxes of irregular sizes. Considering these limits, CMES offers advanced automation to reach new levels of output and performance.
Continued in this CMES Robotics whitepaper.
About CMES Robotics
Powered by AI, CMES Robotics 3D Vision provides the depth, angle, and contour data needed to guide a robot in more complex tasks. Our system enables robots to recognize unstructured, flexible, deformed objects, and deliver a reliable solution from depalletizing to assembly. CMES Vision software has been deployed worldwide for random de-palletization and palletization together with void filling purposes. CMES Robotics automates your warehouse, logistics and supply chain. CMES Robotics is the North American subsidiary of CMES Inc.
The content & opinions in this article are the author’s and do not necessarily represent the views of RoboticsTomorrow
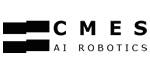
CMES Robotics Inc.
Powered by AI, CMES Robotics enables 3D vision for factory robots. CMES AI vision software enables robots to recognize unstructured, flexible, or deformed objects, pick them up, and loading and unloading. CMES Vision software has been deployed worldwide for random palletization and depalletization along with void filling applications. CMES Robotics automates your warehouse, logistics, and supply chain.
More about CMES Robotics Inc.
Comments (0)
This post does not have any comments. Be the first to leave a comment below.
Featured Product
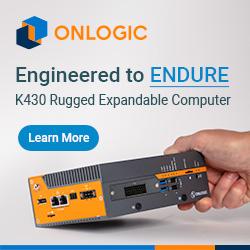