In the following white paper, we explore four conveyor options that fit our modular automation system, enabling you to design a full integrated conveyor system for your application.
Exploring the Design and Benefits of Modular Conveyor Systems
WhitePaper from | RobotUnits
Most extrusion systems feature fasteners and other hardware that loosen over time, opening these structures up to vibration. To avoid these harmful effects, machine designers tend to reach for steel when designing and assembling conveyor systems. Although steel does have its advantages, it can easily drive up costs — especially where handling is concerned. It also doesn’t offer the flexibility of other material systems.
While aluminum extrusions can overcome these issues, it’s important to select systems with the right geometry and modular features. For example, Robotunits aluminum extrusions integrate fasteners, standard screws and centering insertion pieces that keep the screw from loosening when tightened. This interaction between the extrusions and fasteners achieves high tensile strength — up to 4 tons per fastener — and prevents the hardware from loosening. The ability to mix-and-match extrusions also minimizes material costs and assembly time.
The benefits of this kind of modular automation system easily extend to conveyor systems, which require durability, as well as design flexibility in drive options, motor positions and other variables. Seamlessly integrating various conveyor styles and options into a modular automation system can also save you cost and valuable design and assembly time.
In the following white paper, we explore four conveyor options that fit our modular automation system, enabling you to design a full integrated conveyor system for your application.
A JUST-IN-TIME BELT CONVEYOR SYSTEM
If you need to get a conveying system up and running quickly, then the Belt Conveyor series will get the job done. Not only are these conveyors compatible with our modular automation system, but they come with a wide selection of dimensions, belt features, belt speed and drive options, making it easy to configure a system according to your unique application requirements. Choose from frame heights of 40, 50 and 80 millimeters, as well as frame widths of 40 to 1,200 millimeters. Depending on the model, Belt Conveyors can also handle loads up to 800 kilograms.
Other features and benefits include:
- Belt speeds up to 67 meters per minute
- Drive power up to 0.37 0.55 kilowatts
- Quick setup and implementation
- Front-end timing belt drive, front-end direct drive or center drive with timing belt options
- Belt types: low or high friction, as well as foodgrade, oil-resistant and cleated options
- Compatible with conveyor stands, made from clear anodized aluminum, galvanized gadolinium-zinc, galvanized steel and rubber
BUILD SINGLE OR MULTI-LANE SYSTEMS WITH THE TIMING BELT
A second conveyor option that is compatible with our modular automation system is the Timing Belt Conveyor series. These units, which feature a V-guided timing belt to better handle lateral forces, are available as single lane or as multiple lane systems.
They also maintain consistent belt tension due to their unique belt tensioner. With this design, these reliable, adjustable conveying units can achieve perfect belt tracking and handle products of various shapes and sizes — up to 400 kilograms of load. In addition to their simplicity, reliability and excellent price-toperformance ratio, Timing Belt Conveyors offer a number of advantages:
Customizable. The standard frame width of a singlelane conveyor is only 40 millimeters. You can achieve custom widths with multi-lane systems that are connected with a connection shaft with integrated self-aligning couplings. Multi-lane systems can also convey larger and wider products, such as pallets. Conveyors come with optional height-adjustable legs and a wide variety of belt options for applications that involve low to high friction, abrasion or corrosion.
Flexible and fast. To help you meet your requirements, Timing Belt Conveyors come with several drive and motor position options, including space-saving direct drives and front-end timing belt drives with double and triple lanes. In terms of idlers, units include roller diameters of 40 or 80 millimeters. Standard speeds range from 3 to 58 meters per minute, and speed controllers are available for your individual speed adjustments.
In addition, all Timing Belt covers come with a window for visual inspection, which means you can preemptively track wear and tear on your belt, as well as stay ahead of maintenance. And each conveyor comes fully tested and assembled, reducing your setup time.
COMBINE STRAIGHT, CURVED AND INCLINED SECTIONS
A third option is the Modular Belt Conveyor series, which can handle tough applications. Featuring straight sections, as well as curves and inclines, these conveyors can transport heavy loads or sharp-edged parts, such as stamped metal, with speed and safety. Like the other conveyors, these units come with a wide range of belt options and accessories.
Modular Belt Conveyors are available in two shapes: straight and curved. Thanks to their flexible design, you can combine straight, curved and inclined sections — all with a single drive. This design also allows products to be pushed off laterally. In addition, each Modular Belt integrates fully guided belt edges and catenary sags that are enclosed with transparent covers.
Other notable features include:
- No pinch areas
- Direct end drive or timing belt drive options
- Standard width (straight): 150 to 2,000 millimeters
- Standard width (curved): 215 to 1,215 millimeters
- Various belt designs: flights, grip-top, side guards or fingers (combs)
- Standard speeds: 6–50 meters per minute (straight) or 6–30 meters per minute (curved)
- Fit for demanding applications like accumulation, incline, heavy loads and sharp-edged parts
ENERGY-EFFICIENT, MODULAR UNITS CONVEY PRODUCTS IN ALL DIRECTIONS
A fourth option is the Powered Roller Conveyor series. These plug-and-play conveyors transport containers, totes and boxes with precision and efficiency in straight, curved and 90-degree directions and are ideal for zero-pressure accumulation. You can also control each zone separately. There are several options to choose from: available in straight and curved models, Powered Roller Conveyors integrate a 24-volt drive and galvanized steel rollers. Transfer Unit 90° Conveyors let you transfer products at 90 degrees. You can also integrate these units into any zone of a straight Powered Roller Conveyor. And finally, the space-saving Turntable Conveyor series precisely turns products in various directions, all while maintaining the orientation of the box.
Each plug-and-play conveyor series features a variety of roller conveyor modules, as well as fully integrated controls and Poly-V belt power transmission with safety covers. Compared to 230/400-volt drives, the conveyors’ brushless DC motor reduces energy consumption, operating costs and noise levels. Units can carry workpieces up to 50 kilograms in weight and come preinstalled with sensors. They also achieve speeds up to 58 meters per minute and are available in a wide range of standard dimensions.
In addition, Powered Roller Conveyors feature zeropressure accumulation. Each conveyor is divided into individual zones that are interconnected and able to communicate with each other. If a transported product is running toward an occupied zone, then the product remains in the previous free zone until the occupied zone becomes free. Upstream zones follow automatically.
MODULAR BELT CONVEYOR
A FULLY INTEGRATED CONVEYOR SYSTEM
All four conveyors — the Belt, Timing Belt, Modular Belt and Powered Roller series — fit the Robotunits modular automation system, which consists of our patented extrusion and fastening technology. Although there are several options in both the 40- and 50-millimeter extrusion families, both sizes are compatible thanks to their 14-millimeter T-slot. Standardizing the slot in this way, reduces hardware by a factor of three.
This modular system also has assembly advantages. A drop-in T-nut (up to M8) fits both 40- and 50-millimeter extrusions, enabling you to mix and match parts while offering protection against unintended movement. And with our standardized hardware, you don’t have to worry about drilling or milling — making the connection process quick, easy and cost-effective.
Thanks to the extrusions’ concave geometry and interplay with our form-locating, play-free fasteners, you can easily connect extrusions to your conveyor with strength comparable to welded connections. This design also makes it quick and easy to attach accessories or structural elements to the machine frame.
DOING MORE WITH LESS
Lots of manufacturers have their own version of lean production — from improving the flow of goods on the factory floor, to using team-based tools to increase productivity. At Robotunits, our modular products themselves embody lean principles. One of the guiding principles of lean is reducing waste, keeping the number of parts to a minimum while still meeting quality and performance standards. Our unique extrusion and fastening technology consists of multifunctional components that minimize the number of parts you need for any given automation system. For example, one of our standardized parts can perform six different applications, whereas competitive systems may require up to six different pieces of hardware to perform each application.
The content & opinions in this article are the author’s and do not necessarily represent the views of RoboticsTomorrow
Comments (0)
This post does not have any comments. Be the first to leave a comment below.
Featured Product
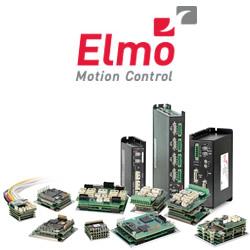