As a growing number of D & F operations embrace smart robotics, some powerful new synergies are starting to emerge. Each robotic system has strengths to offer, but when combined in an integrated workflow, the whole can be much greater than “the sum of its ’bots”.
Robots Work Smarter When They Work Together
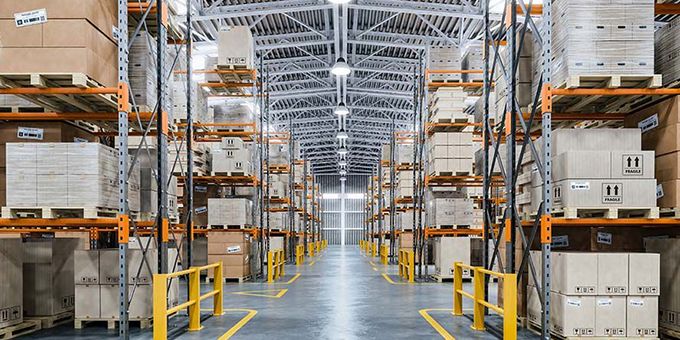
Eric Harty, Stephen Dryer | Honeywell
As an example, let’s consider two robotic systems that have been generating a lot of industry excitement lately: the smart flexible depalletizer and autonomous mobile robots (AMRs).
The smart flexible depalletizer is a long-awaited solution to an arduous and injury-prone task — one that’s traditionally been very difficult to automate. Although it’s simple for human workers to pull items off a pallet and place them onto take-away conveyors, robots have typically required specialized expertise, costly third-party solutions, and extensive pre-programming and ongoing supervision to accomplish the same thing. Today, however, breakthroughs in computer vision, machine learning (ML), artificial intelligence (AI) and gripping technology have enabled a fully automated solution capable of autonomously processing single- and mixed-SKU pallets in any sequence or pattern with no pre-programming.
While the smart flexible depalletizer has been freeing up scarce workers from many of the manual lifting and handling tasks that are among the leading causes of injuries in distribution centers (DCs), AMRs have been taking over repetitive transport tasks like moving pallets or carts through warehouses. Putting robots in charge of these dull, dirty and dangerous jobs does wonders for labor utilization by allowing workers to stay focused on jobs that require more cognitive skills — i.e., the jobs humans do best. Picking times, for example, can be reduced by nearly 50% just by having AMRs take over the transport segment of the workflow.
Both of these solutions deliver valuable benefits on their own. Now let’s look at what happens when you put them together.
Great Robots Make Great Partners
Honeywell Intelligrated’s smart flexible depalletizer offers a wide variety of automatic infeed and discharge options that enable the robot to work continuously, automatically detecting when pallets are empty and initiating change-outs. One of the most effective of these configurations is integration with one or more pallet conveyance AMRs.
In this workflow, the AMRs deliver full pallets to a pick-up and delivery (P&D) stand at the depalletizer cell. Once the pallet is broken down, the depalletizer automatically detects that the pallet is empty and initiates a change-out. It can then be stacked with other empty pallets automatically, removed by an AMR, or discharged in some other way — leaving the station clear for the next pallet to be delivered.
Automating this workflow delivers benefits on many levels. First, it addresses the all-important issue of labor availability, allowing you to elevate scarce labor resources to higher-value tasks. What’s more, relieving associates of dull, dirty and dangerous tasks like these makes them easier to hire and retain.
The second benefit of this dynamic duo is flexibility. This robotic integration can adapt at a moment’s notice to changes in SKUs or pallet processing priorities. By limiting the amount of fixed infrastructure required, it reduces the footprint of the operation. Plus the AMRs can easily be repurposed and scaled.
Last, but far from least, you’ll get predictable consistency and reliability. In addition to continuous operation, this combination eliminates touchpoints, manual errors between workflows and confusion about which pallets need to be processed in what order. Another benefit of this consistency is better visibility into your actual staffing requirements.
Let’s Get Together
On April 7 at 2 p.m. EDT (11 a.m. PDT), the two of us — Eric Harty, vice president, robotic solutions offering, and Stephen Dryer, product manager, robotics & automation, both of Honeywell Intelligrated — will present a free On The Move webinar exploring what your operation can achieve by taking a holistic approach to robotic systems, looking beyond the capabilities they provide individually to realize the greater benefits of integration.
Register today to discover more about the benefits robotic automation can provide your operation, both on their own and in combination.
To subscribe to the Honeywell Intelligrated blog and get exclusive communications and updates, click here.
The content & opinions in this article are the author’s and do not necessarily represent the views of RoboticsTomorrow
Comments (0)
This post does not have any comments. Be the first to leave a comment below.
Featured Product
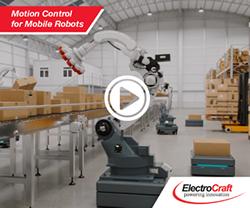