Successful manufacturing companies are combatting the skilled labor shortage by investing in automation and software to complement their existing workforce, meet production requirements, and attract new talent.
Using Technology to Combat the Skilled Labor Shortage

Article from | Robotmaster
The labor shortage issue has been around for years. As the previous generation of skilled laborers retires, the next wave of laborers entering the workforce is not nearly of the same scale. To further add to the complexity, manufacturing is not slowing down. The state of skilled labor has been below equilibrium for some time.
A 2020 study by the Workforce Institute, a workforce and human resources management company from Ultimate Kronos Group, found that prior to the COVID-19 pandemic, there were already projections of a 6 million-worker shortage in manufacturing by 2030.
The additional labor shortages and the move to reshoring because of supply chain issues adds another layer of pressure to already an overburden system.
Recruiters and manufacturing leaders are spinning their heads as the skilled labor pool continues to shrink. Production demands are difficult to meet and production quality is suffering.
The same Workforce Institute study found:
- 62% of hiring decision-makers had difficulty recruiting skilled talent.
- 44% of hiring decision-makers experienced higher-than-average voluntary turnover in the year leading up to COVID-19.
How can you tackle these issues?
Invest in a new workforce
Over the last couple years, a higher-than-average amount of individuals lost their jobs (think hotels, tourism, non-essential businesses, or businesses that couldn’t financially endure the pandemic). Others re-evaluated what they really want to do from 9-5 and are considering new career paths.
Evaluate tapping into these individuals with little or non-traditional experience. Offer training and apprenticeships that can help create and alleviate your labor gap.
Increase retention / create a favorable environment
With low supply and high demand comes the element of choice. Skilled laborers have the upper hand in this dynamic situation—if they aren’t satisfied at their workplace, they can and will leave.
To be an employer of choice, offering professional development and educational opportunities is critical. In addition, the pandemic has highlighted for many the importance of a more favorable work-life balance. Employees are looking for predictable and flexible schedules. Now is the time to get creative with shift scheduling!
Introduce technology
Many manufacturing companies are taking the leap into automation and software systems that can help them meet production and quality requirements—making up for the labor gap. As a result, they are more profitable, allowing for higher wages and benefits to their laborers, making them an employer of choice.
The type of technology that is providing a competitive advantage to these organizations is not out of reach for the rest of the manufacturing industry. With investments in automation, you can start small, investing in one or two robots to complement your existing workforce. Robots can handle tedious and/or repetitive tasks while your existing workers can upskill or reskill to perform other processes.

To achieve an exceptional ROI from your robotic investments, offline programming software is the key.
For those who might not be familiar with the concept, offline robot programming makes it possible to program industrial robot arms from a computer, away from the teach pendent, reducing the robot downtime that is required when programming the points manually. The software enables you to unlock the full potential of your robot cells for greater efficiency, reduce cycle time, and increase production.

The ideal offline programming software to help solve the labor gap dilemma is one that is user-friendly and powerful—one that does not require skilled programmers, but rather enables process experts or users without any robotics expertise to be able to program a robot. It also has embedded process knowledge and flexibility to allow for process specific parameter customization.
Offline programming software has become a differentiator in the manufacturing industry. It is a requirement to innovate and remain competitive, from a recruitment perspective as well. The new workforce is attracted to companies that embrace transformation and modernization. Employees take pride in making an impact in an organization. By adopting new technology, like automation and offline programming software solutions, you become an employer of choice, differentiating from the rest of the manufacturing facilities who are resistant to change.

If adopting automation and offline programming software allows you to leverage your existing workforce to meet production requirements, remain competitive, increase profitability, and attract new talent, what’s holding you back?
Learn more about offline programming software, the best use cases for this technology, and how to get started here. Want to chat with Robotmaster experts? Contact us!
The content & opinions in this article are the author’s and do not necessarily represent the views of RoboticsTomorrow

Robotmaster
Robotmaster, a Hypertherm Associates brand, is an offline, is an offline robot programming software that helps manufacturers maximize their robot's productivity with easy and efficient robot programming for a variety of applications such as cutting, trimming, milling, welding, spraying, polishing, sanding, grinding, deburring, and more. Robotmaster uses integrated CAD/CAM functionality to make robotic programming easy and intuitive for everyone, even first-time users.
Other Articles
Have You Looked at Automating Fabrication Tasks in the Past? Why Didn’t You?
Trane® Saves Over 80 Hours of Robot Programming Time
3 Benefits of Working With a Robotic Integrator
More about Robotmaster
Comments (0)
This post does not have any comments. Be the first to leave a comment below.
Featured Product
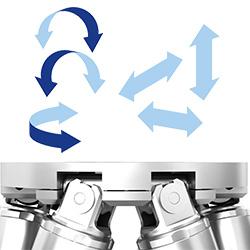