As the labor pool continually changes and work environment standards become higher, it is becoming more difficult to attract and retain employees that are willing to perform repeatable, monotonous tasks.
Increase Manufacturing Efficiency with MiR Robots | AHS

Article from | AHS
As the labor pool continually changes and work environment standards become higher, it is becoming more difficult to attract and retain employees that are willing to perform repeatable, monotonous tasks. The MiR robots can accomplish non-value added tasks and non-rewarding tasks that allow workers to focus on high-value work and increase manufacturing efficiency. There are many different models of MiR robots, and each of them serve a unique purpose.
Inbound Logistics
Inbound logistics is the movement of inventory from a supplier or manufacturer to a distribution or a fulfillment center. The inventory can come in the form of raw material, ready-to-ship products, packing materials, etc. which then needs to be transported to storage.
Typical Manual Workflow:
The traditional process of handling inbound logistics inventory typically consists of the following processes and equipment. An employee offloads multiple pallets from a truck by using a forklift or pallet jack. Once the pallets are offloaded, a worker then transports the individual pallets one-by-one to the appropriate inventory storage area or to a cross dock if the shipment is ready for outbound shipment. The pallets may contain over-sized or oddly shaped items which make it more difficult to transport and can potentially pose a safety hazard. The worker will either put the material into a storage rack or drop off the pallet in a designated area signaling to another worker that it is ready to be put into material storage.
By implementing MiR robots, AHS can optimize the inbound logistics workflows and increase manufacturing efficiency to consist of something more like the following.
Automated Workflow:
A worker, or an automated truck unloading system, offloads the pallets using a traditional forklift or an automated guided vehicle like Nipper. The pallet is placed on a Pickup and Dropoff (P&D) stand in a designated pick-up area where a MiR robot can drive under the pallet to pick it up. The MiR robots capable of transporting pallets are the MiR600 and MiR1350 and have carrying capacities of 1,200 lbs. and 2,975 lbs. respectively. The MiR robots then take the pallets to either the material storage area or a cross dock for outbound shipment. This completely replaces the need for manual handling and forklifts. MiR robots are very effective in transporting oddly sized material, so it increases safety during truck unloading.
Benefits:
- Reduce labor hours and spend on non-value adding material transportation
- Help overcome labor shortage by autonomously handling non-rewarding, repeatable tasks
- Reduce the number of forklifts needed
- Increase flexibility and availability by having on-demand transport
Raw Material Storage
Raw material storage is a sector of a manufacturing facility that is essential to production operations. Depending on the business, it can consist of steel, lumber, stone, plastic, grain, oil, chemicals, etc. Raw material storage is the holding area before the material is put into production.
Typical Manual Workflow:
The raw material is dropped off in the storage area to then be put away by a fork truck or AS/RS. When the raw material is needed for production, the WMS signals for the material to be retrieved and delivered to production. The raw material is retrieved, and a worker must use a fork truck or pallet truck to move the material to the designated manufacturing cell.
Automated Workflow:
When the raw material is needed for production, the pallet is retrieved, and a MiR robot can deliver the material to the designated manufacturing cell. The MiR robot will autonomously navigate to the required location in manufacturing and drop off the pallet in a staging area.
The MiR Shelf Carrier 250 top module is a standard module, which fits to the MiR 250, enabling the robot to collect and deliver shelves, carts and other applications. This robot can be used to transport small pieces such as hardware from cell to cell.
Benefits:
- Optimized use of specialized forklifts
- Reduce the number of forklift-related accidents
- Employees can focus on value-adding activities
- Same robot can deliver many different loads including pallets, containers, carts, etc.
- Just-in-time delivery of raw material to production
Once material enters the production and assembly lines, the material and partially assembled products move between cells, lines, or departments frequently.
Production and Assembly Lines
Typical Manual Workflow:
When the material arrives to a cell (or line), the worker completes their task with the material, and he/she will then often put the product in a cart or bin to move to the next cell while discarding any extra material. Either that worker must take the cart to the next cell, or the worker from the receiving cell must retrieve it and bring it back to their production cell. If this is not the case, then there is typically a designated person whose sole purpose is to move material around the manufacturing facility.
Automated Workflow:
MiR offers a wide range of robots for quick delivery of in-process goods. The MiR robots transport raw material from the strorage area to the production and assembly lines. The worker completes their task with the material and then puts the finished good into a cart while discarding extra material or waste into a separate cart. Once the carts are full, MiR robots will come retrieve them and take them to either the next production cell or the waste disposal area. The MiR robots used for such tasks have a carrying capacity of 550 lbs.
Benefits:
- Infrastructure free robots add flexibility for the dynamic factory layout and changing workstations
- Eliminating human-prone errors and mishaps
- Increase safety among workers as forklifts are removed from the area and replaced by safe collaborative AMRs
- 24/7 reliable and automated production line feeding
- Space optimization by eliminated local storage at production
- Able to drive in forklift or human quarantined areas such as clean room environments
Finished Goods & Outbound
This is where a manufacturing company collects the finished goods and stores them to then be later picked, packed, and shipped to distributors, retailers, or the customer. The management of inventory and orders as well as arrangement of freight carriers can often be a daily challenge for workers in this area.
Typical Manual Workflow:
A worker delivers the finished goods to the area using a forklift and puts them into the designated storage area until they are ready to be picked, packaged, and shipped. Once an order for that product is received, a worker picks the product(s), delivers it to the packaging station, and discards the pallet into a pallet magazine dispenser. Once packaged, a worker will arrange a pallet for an outbound shipment and load it onto the truck when it arrives.
Automated Workflow:
A MiR robot will autonomously deliver the finished goods to the storage area where they can later be robotically (or manually) picked, packaged, and shipped. When an order is received, the MiR robot will retrieve the product from the storage area and deliver it to the packaging area. Once the pallet is empty, the MiR robot can deliver the empty pallet to a pallet magazine dispenser, and when the dispenser is fully, the MiR robot can empty it and take the pallets to the required destination(s).
Benefits:
- Safe around employees doing value-added services like packaging and gift wrapping
- Replace order picking trucks for mixed pallet stacking
- Optimized use of forklift
- Scalable and customizable internal logistics solution
Summary
Implementing MiR robots can drastically change and improve manufacturing efficiency by automating non-value added tasks such as material, hardward, and pallet movement. One of the challenges that manufacturers have reported is getting the MiR interface to seamlessly integrate with current operations and systems since each operation is uniquely different. Our team of experts at AHS will ensure that MiR integrates with existing systems and fully test the operation to make sure everything flows as it should.
Contact AHS to start optimizing your manufacturing workflows!
The content & opinions in this article are the author’s and do not necessarily represent the views of RoboticsTomorrow
Comments (0)
This post does not have any comments. Be the first to leave a comment below.
Featured Product
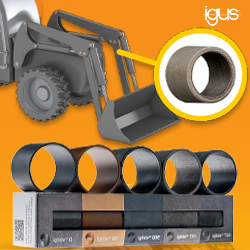