Integral to, and supporting RoboFS is unique technology for automated receiving of incoming goods and their reconfiguration into SKU-specific containers and trays for subsequent high-bay storage and picking.
A look Into HDS Global's Ultra-Lean, Hyper-Personalized eCommerce Fulfillment Model
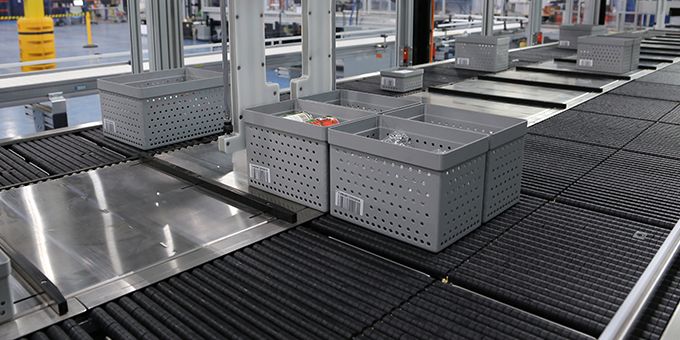
Jim McMahon | ZebraCom, Inc.
Integral to, and supporting RoboFS is unique technology for automated receiving of incoming goods and their reconfiguration into SKU-specific containers and trays for subsequent high-bay storage and picking.
Designed and built by Shuttleworth, the 100-percent modularized unit consists of highly-specialized functions connected by 350-linear feet of smart conveyor packed into a tight footprint.
HDS Global's robotic receiving module for automated handling and preparation of incoming products for high-bay storage and picking.
Home Delivery Service (HDS, also known as HDS Global) is redefining the retail eCommerce experience. According to Louis Borders, CEO and Founder of the company, and co-founder of the Borders bookstore chain, “We’ve worked relentlessly to ready a new kind of eCommerce service, leading with fresh grocery, and including a wide selection of general merchandise, around what consumers always hoped it would be – highly personalized, convenient, exceptionally fresh, eco-friendly, and with no-cost home delivery.”
Hyper-Personalization
HDS is designed to provide a highly-personalized eCommerce customer experience built around each individual shopper’s dietary needs, preferences, and brand favorites. In addition to packaged items, this includes customization of items such as made-to-order meats, poultry, seafood, produce and other prepared foods to exact customer specifications.
Called hyper-personalization, the consumer will be able to order a custom steak, for example, requesting a particular type of marbling, thickness and age. Or, they can order just one banana, and choose how ripe they want that banana to be for breakfast early the next morning.
Approximately 100,000 fast-moving SKUs – chilled, frozen and ambient temperature – will be available for same day delivery, or express one-hour delivery, if desired, supplied by HDS' 150,000-square-foot fulfillment centers (FCs) located throughout urban and suburban areas. Slower-moving non-stocked SKUs will be filled as part of the customer's next order, which may be for next-day or two-day delivery.
Orders are will be delivered in reusable delivery totes that are sanitized after every use, eliminating the need for paper and plastic carrying bags. HDS' temperature-controlled courier vans will deliver orders free-of-charge to the customer’s doorstep, and pick up empty totes and any returned items. A high level of in-person contact with its customers is a key part of HDS’ service and delivery strategy.
Online Mall
HDS Global is designed to be, essentially, an online mall that enables ordering and in-house door-to-door delivery for not just its own ultra-personalized grocery store, but also for many other retailers.
Products from branded retailers like apparel shops, pharmacies, department stores, confectioners, auto parts stores, and any shops that might be found in brick-and-mortar shopping malls, will also be available to be purchased through the HDS mall website.
Items can be selected from different stores, put into the customer's same HDS grocery shopping cart and checked out, with timely delivery by HDS courier vans.
Imagining an Ultra-Lean eCommerce Fulfillment Solution
Although not yet online, HDS Global has been in the making for more than five years. Much of the company's evolution revolves around the adaptation of existing technology to support its unique offering, as well as the development of new technological solutions.
"We reimagined eCommerce fulfillment technology from the ground up, so it gave us the opportunity to pause and think," said Aravind Durai, Vice President of Automation and Founding Member at HDS Global. "When we did our early due diligence, including a considerable number of factory visits and planned audits with subject matter experts, we found there was significant inefficiency built into existing eCommerce fulfillment systems. Boxes and containers moving at a very high velocity to their destinations arrived there, and just sat for the next downstream process to take over. Running systems at high speed consumes more energy, and requires increased maintenance and support to keep these systems running. Many of the systems we evaluated fell into this mode of operation."
"We were not planning to move orders at a frenzied pace," added Durai. "Instead, we were interested in systems that would allow us to potentially move items at a much more controlled and slower pace, but still accomplish a very high throughput. By using software-defined processes, over time, we could squeeze a significant amount of efficiency out of utilized hardware."
"Using highly-flexible systems, like mobile robots and virtual conveyors, and employing software to predict exactly when each box or container is required to arrive at specific locations and times, the conveying systems, and the speed and path of mobile robots, can be adjusted for precise downstream coordination to keep throughput moving smoothly," continued Durai. "If a box or container arrives at a location too early, then queueing problems result, if it arrives too late then it holds up throughput. If it arrives just in time, then a very lean system ensues."
The realization of this eCommerce model has resulted in a unique and proprietary artificial intelligence-based warehouse management system. Designed to direct mobile and articulated robots, and smart conveyors, it processes orders by SKU and serialization, providing highly-personalized fulfillment as a 100-percent automated, lights-out operation.
RoboFS
These automated systems, combined, are referred to as RoboFS®, a proprietary technology of HDS Global. Except for receiving and shipping dock activities, all other functions within the HDS Global fulfillment model are integrated systems of RoboFS.
"RoboFS is a sophisticated, end-to-end robotic fulfillment system for large-scale distribution operations," explained Durai. "Featuring integrated hardware and software, the system is fully modular, scalable and configurable. Designed to enable quick, touchless order fulfillment, it can efficiently pick, pack and ship a high volume of items in varying shapes and sizes."
Standardized Transport Containers
Forming a building block of this efficiency is the utilization of a standardized transport container within RoboFS. This is a 400 x 600 millimeter tray, which carries customer orders and picking resupply throughout the fulfillment center.
Pallets and cases are decanted upon entry into RoboFS, and put into as many as eight separate bins within each tray. Each bin represents a separate SKU or serialized SKU. Suppliers may ship goods in these RoboFS trays which further increases sustainability and reduces labor.
The system utilizes standardized trays with form-fitting bins within.
RoboFS automatically stores these trays in high-bay via its autonomous storage and retrieval system (AS/RS), then pulls trays from these locations for picking. Autonomous articulated robotic arms pick products from the trays to fill orders.
Autonomous Mobile Robots
Another key system of RoboFS is its fleet of autonomous mobile robots (AMRs), which access inventory and carry it from station to station, process to process, throughout the fulfillment center.
"Instead of thousands of feet of conveyor traversing the facility to transport inventory and orders, it is the AMRs that do the transporting between receiving and the induction/receiving stations of the AS/RS, and the movement of picked orders to be packed, labeled and moved to staging locations for shipping, where the packages are manually loaded on to carrier trucks," said Durai.
Automated Tray Filling for High-Bay Storage and Picking
A very critical system to the success of RoboFS is the automated receiving of incoming goods and their reconfiguration into SKU-specific containers and trays for high-bay storage and picking. This system was designed and manufactured by Shuttleworth, a leading designer and manufacturer of integrated material handling solutions. The company began engineering the automated tray filling inventory receiving system for HDS Global in 2012, and has been continually streamlining the system's operation.
"The RoboFS model incorporates receiving modules for automated handling and preparation of these incoming products," said Ken Tinnell, Vice President & General Manager of Shuttleworth. "Each module consists of a collection of receiving cells that perform different operations relating to receiving and product positioning for optimized storage and picking. These systems integrate unique technology designed to execute highly specialized functions."
"The induction system optimizes the entire tray storage and picking processes," continued Tinnell. "It is where the inventory trays are configured in a way to maximize density and significantly improve storage and picking efficiency."
A combination of using unique inventory receiving module technology – an automated tray-maker system, tray-breaker system, and smart-conveyor system – facilitates the optimum performance of the receiving module and enables the high-performance operation of RoboFS.
Automated Tray-Maker/Tray-Breaker System – a Fundamental Shift in eCommerce Receiving and Put-Away
The tray-maker system is designed to accept SKUs and serialized SKUs from incoming inventory which has been depalletized and removed of secondary packaging. These products are manually put into SKU-specific bins that fit geometrically into trays. Trays can have a different number and size of bins within them. Shuttleworth is currently developing an automated system, called a case-breaker system, designed to automatically open cases and fill bins.
"Filled bins are conveyed into the fully-automated tray-maker, then moved into a staging area," added Durai. "When enough bins are accumulated to fill a tray, that group of bins is carefully dropped into the tray, and the tray is then moved onto a conveyor leading into an accumulation area and out of the receiving system, where an AMR transports the tray to induction for high-bay storage."
The robotic Shuttleworth Tray-Maker system automatically fills trays at a high rate of speed.
"The tray-maker manipulates SKU-filled bins at a very high rate of speed, collating and assembling the bins into as many as eight compartments per tray utilizing gantries and specialized, custom-made automation to accomplish the tray-making process," said Durai.
When a bin is depleted of inventory, the tray that is housing that bin is sent back to the receiving module, the bin is removed from the tray and replaced with a new inventory-filled bin. The removing of that bin is automatically performed by a tray-breaker system, which operates similar to a tray-maker, but in reverse. Up to eight bins can be removed at the same time from a tray.
Once removed, the tray is routed to the tray-maker system which refills the tray with new SKU bins, then releases the tray to an AMR which transports the bin to an AS/RS induction station.By continuously recombining trays, the tray-maker/tray-breaker system defragments the tray storage space in the AS/RS high-bay, maintaining high-cubic-storage density.
This fully-automated tray-maker/tray-breaker system is completely unique to RoboFS, and represents a fundamental shift in how HDS Global is approaching eCommerce receiving and put-away, which is, conventionally, a manual process.
SKU Affinity
When inventory within bins is received into the tray-maker, instead of using the next available random tray for induction, the RoboFS software uses SKU affinity to pair products with up to eight other products within the same tray. Products that are, historically, likely to be purchased in conjunction with each other.
"This application of SKU affinity reduces the number of trips required for inventory retrieval of trays stored in the high-bay," said Durai. "The software's sophisticated artificial intelligence matches as many as 100,000 grocery SKUs for purchasing similarity, based upon RoboFS proprietary algorithms."
AS/RS crane movement, retrieving inventory in high-bay, is both time- and energy-consuming. RoboFS' SKU affinity significantly reduces the number of inventory retrieval cycles.
Smarter Conveying
"This automated receiving module of RoboFS was designed by Shuttleworth to fit into a very tight pattern to leverage space efficiency, which is critical to HDS Global's strategy to position its fulfillment operations in urban areas where space is at a premium," explained Durai. "Supporting this is the capability for careful, gentle and precision movement of bins and trays throughout the tray-maker and tray-breaker systems, as well as smoothly connecting with inventory induction into the receiving module, and connecting with AMRs as trays are released from the module."
HDS Global selected Shuttleworth to engineer and manufacture this conveying and bin/tray-movement system. The result is a 350-linear-foot system of smart-conveying technology, in which every square foot of conveyor has the capability for controlled and gentle bin and tray movement and accumulation. Additionally, every aspect of the conveyor needed to be modularized, for quick disassemble and reassemble, to accommodate inevitable eCommerce throughput modulations.
Because the need for precise control of bins and trays within the receiving module is critical, Shuttleworth incorporated high-performance smart-conveying systems, Slip-Torque® roller technology and Dynamic Accumulation.
Slip-Torque and Dynamic Accumulation
Slip-Torque roller technology utilizes individually-powered, stationary rotating roller shafts covered with loose, segmented rollers, which become the conveyor surface. When trays and bins stop on the surface of the conveyor, the segmented rollers beneath also stop, generating low back-pressure accumulation, and minimize product damage. It is the weight of the trays being conveyed, combined with the coefficient of friction between the shafts and the inside diameter of the rollers, that provides the driving force. As the weight of the conveyed trays and bins increases, there is a corresponding increase in the driving force supplied.
"Slip-Torque’s low line-pressure provided throughout the conveyor system, and its continuous-motion Dynamic Accumulation, allows for precise product placement on the conveyor while it continues to take product flow from an upstream line for a period of time, where other conveyors would have stopped well before," explained Tinnell. "A low back-pressure accumulation buffer absorbs irregularities in the production flow and provides a smooth, even flow on the line. A servo-controlled guide provides efficient lane changing of bins and trays, eliminating backlog at the point of entry."
"The system allows the same conveyor to be split into multiple, independently-operating lanes," continued Tinnell. "For example, the middle lane can accumulate, while at the same time the right lane and the left lane can both convey, or even run in opposite directions. Each lane can act independently, if needed, but is powered by only one common motor, which also reduces energy usage."
This conveyor system has the ability to modulate the speed of different sections of the conveyor via a centrally-controlled PLC and HMI. As bins and trays are moving through the system, the rollers at the back end of the conveyor can be moving faster than the ones at the front end of it. The bins and trays can be moving at variable speeds on different sections of the conveyor as dictated by throughput requirements. This controls the bins/trays spacing on the conveyor, keeping these separated, and equally spaced from each other to minimize product contact and facilitate infeed into the tray-maker/tray-breaker systems.
"Throughout the length of the conveyor, product control devices like stops, pushers and clamps are used to modify the flow of conveyed bins and trays," said Tinnell. "These conveyors utilize the space between rollers to allow these devices to be mounted below the surface, reaching up between the rollers to effect more precise and flexible bin/tray motion control, without interfering with the line flow."
RoboFS, Exported Technology
While HDS Global continues to build out its preeminent online mall eCommerce model, its RoboFS fulfillment technology has garnered considerable attention from a number of major manufacturers and distributors for implementation within their own operations.
This interest has prompted the company to build out a center in Plainfield, Indiana to display and demonstrate its unique eCommerce model and the RoboFS technology empowering it, in a totally integrated micro-warehouse exhibit.
It is clear that HDS Global, with its ultra-lean, hyper-personalized RoboFS technology, will be capturing the attention of many more distribution professionals as the company continues to roll out its very unique approach to eCommerce fulfillment.
About Home Delivery Service (HDS Global)
Founded by Louis Borders, Home Delivery Service (HDS Global) is transforming eCommerce – end-to-end – leading with fresh groceries and including a wide range of general merchandise. Powered by the latest in AI and advanced robotics, the company’s patented automated fulfillment system, RoboFS®, enables quick, touchless order fulfillment, resulting in fresher-than-store perishables, delivered direct to the customer’s door. The company has also developed a novel user experience, customized around the dietary needs, preferences, and brand favorites of each individual customer. With its bold vision and innovative technology, HDS has secured funding partnerships from the world’s leading brands, including Ingram Micro and Toyota.
About Shuttleworth
Shuttleworth is a leading designer and manufacturer of integrated solutions that solve company’s material handling challenges. When a company needs a conveyor system that will accumulate, flip, stack, rotate, push, divert, or index its products for manufacturing or packaging processes, Shuttleworth can design, build, install and service it throughout the system's life. Year after year, Shuttleworth continues to revolutionize the material handling industry with Slip-Torque® technology, conveyor systems and equipment innovations that are as unique as the product lines that they handle. Shuttleworth has been a member of the Packaging Machinery Manufacturers Institute (PMMI) since 1967, and is a member of the Processing and Packaging Machinery Association (PPMA) in the UK. The company is certified ISO 9001 since 2008.
About ProMach
ProMach is a family of best-in-class packaging solution brands serving manufacturers of all sizes and geographies in the food, beverage, pharmaceutical, personal care, and household and industrial goods industries. ProMach brands operate across the entire packaging spectrum: filling and capping, flexibles, pharma, product handling, labeling and coding, and end of line.
The content & opinions in this article are the author’s and do not necessarily represent the views of RoboticsTomorrow
Comments (0)
This post does not have any comments. Be the first to leave a comment below.
Featured Product
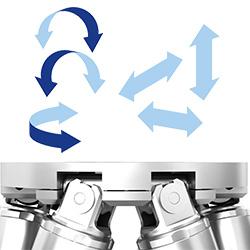