CRG Automation and its team of engineers — with specialties such as mechanical, electrical and controls —began devising custom engineered solutions, often incorporating advanced robotics.
2021 Top Article - How a Team United in Just 18 Months to Overhaul How America Destroys Its Most Dangerous Chemical Weapons
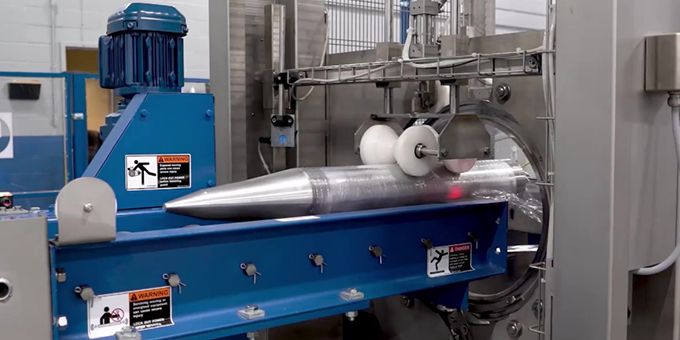
Case Study from | CRG Automation
The last and most deadly of their kind, the military’s M55 rockets, filled with VX and sarin nerve agents, numbering approximately 70,000 at Central Kentucky’s Blue Grass Army Depot, almost double the population of the small college town where they’ve been safely stored and aging for decades.
Designed in the late 1950s and rushed into production, the chemical-filled rockets earned the moniker of “difficult animals” from Jeffrey Brubaker, technical adviser for the U.S. government’s Program Executive Office — Assembled Chemical Weapons Alternatives (PEO ACWA). As the name suggests, the program’s origin dates to a decision by Congress in 1997 to seek alternatives to the then ongoing incineration of America’s chemical weapons stockpile, as mandated by international treaties, because initial efforts had prompted environmental and community concerns.
“With them being rushed into production, it gives you an idea that they weren’t going to do well over time, and that’s what the program has shown,” Brubaker said, describing how many of the M55 rockets have warped over the decades and become prone to leaking their deadly chemical agents.
Staring down an aggressive 2023 destruction deadline, PEO ACWA took an unprecedented step in mid-2019. The organization’s leadership, which had approved a destruction plan, decided to rethink the entire process, seeking to create more efficiencies and enhance safety for those involved.
With an ambitious timeline in mind, the government activated a contracting mechanism first established in NASA’s 1950s race to space to bring in privatesector industry leaders known as an Other Transaction Authority (OTA).
Seeking automation expertise to make the process more efficient and enhance the use of robots and newer automation technologies, the government turned to a Louisville, Ky., engineering firm best known for building packaging lines for the likes of Coca-Cola, Kellogg’s and Kraft. CRG Automation earned its reputation over two decades as it developed, built and optimized packaging and processing equipment for the food, beverage and consumer products industries. As the company expanded over the years, its repeat customers approached with more and more complex problems.
CRG Automation and its team of engineers — with specialties such as mechanical, electrical and controls — began devising custom engineered solutions, often incorporating advanced robotics.
While the company continues to offer cartoners, case packers and other secondary packaging equipment, it has increased its focus on advanced offerings such as robotic integrations and custom design-build equipment. Its expansive Louisville headquarters with its on-site modern machine shop includes space to conduct full assembly and testing.
“As a past member of the military, this project took on a special importance for me,” said CRG Automation President James DeSmet. “The perplexing engineering problems to solve, the rapidly approaching deadline and the severity of the chemical agents involved all added up to a challenge we wanted to tackle.
"We’ve often talked here at CRG about how our engineers like the kind of problems that leave other R&D teams scratching their heads or banging them against the wall. We knew this was an opportunity unlike any other, and, even staring down the pandemic, we knew we could do it.”
Challenge No. 1: Creating a safer, more efficient destruction process.
To speed up the disposal and further prioritize worker safety, PEO ACWA sought a way to break down the disposal process into different steps, essentially draining the chemical agent and disposing of it in a separate way. To understand the benefit involves understanding what was required when workers encountered issues during the initial version of the destruction plan.
While the original process was entirely remotely controlled by workers, the system included a number of moving components, sensors and waste streams, so maintenance concerns were top of mind. Maintenance requires wearing the most stringent of personal protective equipment — the level A suit. Just putting on the suit, which includes respirators and air hoses, typically takes up to four hours, said Ken Ankrom, OTA project manager for Amentum.
The reactors used in the destruction process measure three stories high. “You have a two-hour maximum time in the suit,” Brubaker added. “By the time you get to your workstation, you’ve expended 30 minutes. So how much can you really get done in an hour?”
In developing the new system, the goal of CRG Automation and the full team was to reduce these maintenance efforts by workers as much as possible.
“When we can take a person out of handling a weapon, we’ve increased safety by magnitudes,” said Terry Staggs, also of Amentum. “We have a cardinal rule — expose the minimum amount of people, to the minimum amount of the hazard, for the minimum amount of time .”
Both Ankrom and Staggs have seen firsthand how advancements in chemical weapons destruction now require fewer and fewer people. Ankrom started working with chemical agents in the mid-1980s, recalling how his first project, which focused on a hallucinogenic, required sending 15 people inside “as it was all manual.” Even as recently as 2014, workers at Blue Grass Chemical Activity manually separated rocket warheads and motors and recently had to separate fuzes from warheads to support testing at the Anniston Static Detonation Chamber (SDC) disposal plant, added Staggs, who has worked with chemical weapons since 1978.
“Adding the automation with robots has assisted us with reducing people interaction with these aging chemical weapons,” Staggs said. But Blue Grass Army Depot’s original disposal system plans, even with its robots, presented problems when workers discovered leaking rockets.
“It would take multiple days to recover from a leaker munition discovered in process and re-start processing again,” Staggs said.
So the full team — PEO ACWA, Amentum, CRG Automation, Bechtel Parsons Blue Grass and additional partners DynaSafe and Crown Packaging — began devising a new system to dispose of the rockets, which measure 6 feet long and 4.4 inches in diameter.
With their newly designed rocket warhead containerization system, once a chemical-filled warhead has had its chemical agent separated from its rocket motor assembly, the all-robotic system places the warhead into a steel container with a lid that’s sealed in place using a crimp station. The automated robots, which were designed, fabricated and integrated by CRG Automation, then place the containers onto packaging skids that hold 25 containers each. These skids then are monitored in an airlock to ensure no surface contamination and moved to the next step in the process — a Static Detonation Chamber in which intense heat greater than 1,000 degrees destroys the warhead and overpacked container. The drained chemical agent is neutralized in a separate process within the Main Plant facility.
In designing the system, CRG Automation’s engineers utilized eight industrial robots, as well as six autonomous mobile robots. The system allows for the processing of more than 25 warheads per hour, improving speed and efficiency and reducing downtime.
The group continuously focused, too, on how to improve each aspect of the process. Initial tests found that the system needed even higher temperatures to create enough heat inside the warhead’s fuze to activate the deflagration process.
A series of weekend text messages between DeSmet and Bobby Phillips, a chemist and engineer for PEO ACWA, resulted in a solution they affectionately dubbed “the witch’s hat.” The pair figured out a way to modify the plug and nose end of the munitions to allow for more efficient heat transfer to the fuze area of the warhead.
“That led to a significant increase in how fast it worked,” said Phillips, noting the activation time dropped significantly to just 15 minutes. “That’s right where we wanted it to be.”
Challenge No. 2: Cutting a path to success with warped rockets
The redefined process impressed the PEO ACWA so much so that the team was presented another problem to tackle.
Because of their age and initial rushed manufacturing, a significant number of M55 rockets had warped during storage, creating the possibility that their different dimensions would not fit properly in the system. Ankrom estimates up to 12,500 of the 70,000 rockets may be warped, and each one that enters the line can conceivably stop the process, requiring workers to enter and resolve issues. The consequence? Up to two days added to the overall destruction timeline for every instance the line stops.
The former system required spinning the entire assembly and creating a horizontal cut to the rockets to separate warheads from motors. But horizontal cuts meant any warped rockets that were already leaking would spread their chemical agent instead of keeping it neatly confined. CRG Automation developed an alternative method by holding the assembly fixed and making the cut in a vertical orientation, ensuring that any leaking chemical agent would simply gather in the bottom of the containment device. Making these vertical cuts also added more precision and accuracy with the robots able to make cuts as small as one thousandths of an inch consistently, Ankrom said.
“Given the technology that CRG Automation was able to bring to the table, they developed a cutter that was very precise,” Phillips said, noting the technology will also be incorporated to improve rocket motor processing at the Anniston SDC in Alabama.
Should a leaking rocket be encountered following the vertical cuts, a new pivoting reject station is used to take the leaking rocket and place it into an overpacked container. The new design creates yet another efficiency and safety improvement, as the old system required workers to handle the overpacking.
The new technology also identifies if the cut location of the rockets has warped and adjusts the system’s hydraulics to compensate and keep the same pressure around the rocket while cutting.
“What the robots really lent themselves to was taking the small steps to see the chemical agents and make sure we don’t spread any contamination,” Ankrom said, adding that the new rocket-cutting robots also require far less maintenance than the earlier designs. “That keeps people out of the room, which is always safer.”
Challenge No. 3: Identifying leaking rockets before disposal begins
With the vertical rocket cutting design complete, the team turned to developing a system to help identify those leaking rockets long before the robots made their first cut.
“If we can avoid the leakers before they ever go to the vertical rocket cutting, then we’re never having downtime,” said Ankrom, noting that less downtime is essential to the goal of completing disposal of the 70,000 rockets by 2023.
The old system used glove boxes to detect chemical agent vapor. Doing so required removing a sample plug, inserting a near real-time monitor, running a test and then restoring the plug and any discharge. The process added six minutes to the disposal of each rocket. Beyond that, “this was all going to be done locally by people at the time and had its limitations,” Ankrom said.
Over the course of a few months, CRG Automation and the full team evaluated four technologies to improve the process both in speed and accuracy.
Among them was handheld leak detection technology used in petrochemical plants, as well as iridium utilized in medical industries. But it was a chance flight and visit through a Transportation Security Administration (TSA) checkpoint that led to the solution.
TSA agents pulled Ankrom aside to inspect his backpack. “I was surprised at how much clarity there was on my backpack,” he recalled of the security system imagery. “They could tell my keys, my prescription medications. I was thinking at the time, ‘Heck, if you could look at my backpack like that, there’s got to be something we can do.’”
The team began exploring X-ray technologies similar to what TSA uses, but quickly realized that TSA’s equipment stops the line and takes a snapshot of each person’s carry-on belongings.
To keep the destruction process moving along, it needed to do justthat — keep moving.
The team devised a process to scan each rocket while it was moving and focus on the areas where there’s most likely to be leakage. The system also allows technicians to gain a closer look at those rockets that suggest they may have leaks but do not offer complete certainty. CRG Automation’s engineers crafted the ability to tilt each rocket up to 10 degrees for a better look.
“This was another example of how the team not only redefined a complex process but took it a step further to more efficiently dispose of so many chemical weapons in such a short time frame,” said DeSmet of CRG Automation.
Collaboration leads to speed
Solving the three challenges and developing the revised system took just about 18 months. Multiple tight deadlines throughout the process proved tough, of course, particularly given the ongoing coronavirus pandemic and its complications, but the team persevered.
The rocket warhead containerization system took just one year “from preliminary design to final design to actual full-scale production and factory acceptance testing and deploying to the field,” Ankrom said. “That’s fast even in the commercial world, but certainly in government. This has been one of the most cooperative teams I’ve been on.”
Added Jonathan Weitzel, engineering lead for Bechtel: “Most rewarding is just the opportunity to work on something this fastpaced and this integrated. To go from the starting point of zero to having almost the last piece of it installed now is absolutely incredible. Things don’t move that fast.”
Ankrom complimented CRG Automation’s focus on solving problems. “They’re all about bringing solutions to customers,” he said, adding the company’s attention to detail is top-notch.
He recalled how he made a comment just in passing at one point about a robot’s end-ofarm tool, and the company quickly incorporated the suggestion. CRG Automation’s engineers also designed the carts used in the system to be different colors so workers could easily identify inputs and outputs.
“That says something to me,” Ankrom said. “It says they’ve dealt with people before and know situations that may lead to mistakes and want to plan for that. To CRG, details matter.”
CRG Automation’s close proximity to the Blue Grass Army Depot in Richmond also brought advantages. In less than two hours, the team could convene on site to support the project’s needs.
“Knowing they’re just down the road builds a rapport,” said Phillips of PEO ACWA. “To come up with something that’s this effective, efficient and safe to operate, it’s just amazing that it came together this quickly. "Here’s a group in CRG who were ready to learn about chemical weapons, their specific challenges and solve the problems with a focus on safety. These guys picked it right up and turned out some great products for us.”
Looking ahead
With the challenges solved and new system designed, the chemical weapons disposal process begins anew.
For many years, there was a reluctance to talk openly about the stockpile, Brubaker said, and that led to concerns between the Richmond community and the military.
“It’s been a long time coming to destroy this stockpile. Over 30 years first coming up with the approval to go test technologies and coming up with the necessary funding. These facilities are complex — years of construction and years of testing out the process before we go into operations,” Brubaker said.
“And at the end of that, to realize that we need to do something different, that we need a more robust process — to accomplish that in just over a year’s time is just fantastic. I got here at the Blue Grass Army Depot in 2009. In 10 years, I’ve seen it go from essentially a grass field to up to 19 acres of a fully robotic, fully automated processing plant.”
The content & opinions in this article are the author’s and do not necessarily represent the views of RoboticsTomorrow
Comments (0)
This post does not have any comments. Be the first to leave a comment below.
Featured Product
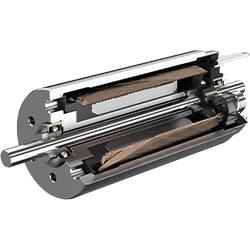