The robotics industry is undergoing a significant transformation. There is a need to learn from the past, as multiple times, robots failed to behave as expected because of mechanical failure, power disruption, software issues, and environmental factors.
Standards, Guidelines & Industry Best Practices for Industrial & Collaborative Robots
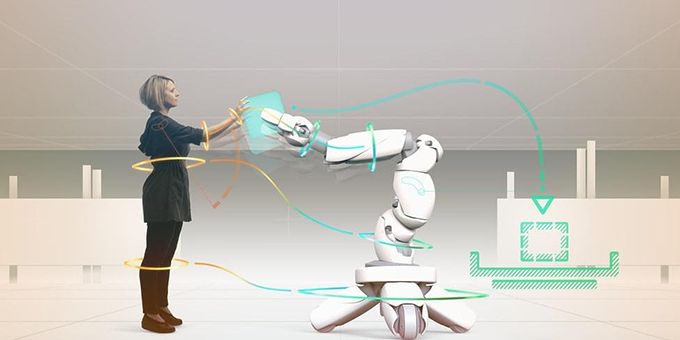
Shubham Pratap Singh, Field Application Engineer | LDRA India
When we think about robotics, the first picture that comes into our mind is either a humanoid robot or a robotic arm, but robotics is not limited. It has applications in every binding domain, like aerospace, defense, space, automotive, medical, industrial, etc. Most of these applications are safety or mission-critical. Therefore, we should focus on the safety and security of these robots; otherwise, a malfunction can cause severe harm to humans or a colossal capital loss.
Robots classified based on their application types include industrial robots (such as logistics, manufacturing) and service robots (robots that assist human beings in Defence, Educational, Household, etc.). In this article, we will focus exclusively on industrial robots.
-
Industrial robots are the machines used for industrial automation that can automatically control, move/rotate around multiple axes. These robots can be either mobile or fixed—for example, hand-guided robots, serial manipulators, etc.
-
Collaborative robots (Cobots) are the enhanced versions of industrial robots. These robots work along with humans and interact with them using end effectors. An end effector is a device that interacts with the environment.
Market Dynamics – India & Worldwide: Robotics is one of the emerging fields in India, IndustryARC's forecast1 predict a 13.3% compounded annual growth rate for the Indian industrial robotics market from 2019-2024. And if we talk about the worldwide scenario, then according to Mordor intelligence2 report, the robotics market was valued at $23.67 billion in 2020, and it is expected to reach $74 billion by 2026 with a compound annual growth rate of 20.4% over the forecast period (2021-2026). Moreover, it will cause a big transformation to other sub-industries like agriculture, defense, etc., due to the advancement & adaptation of robotics in these areas.
Why are software standards important?
The robotics industry is undergoing a significant transformation. There is a need to learn from the past, as multiple times, robots failed to behave as expected because of mechanical failure, power disruption, software issues, and environmental factors. We must consider ways to avoid robot malfunction because it can lead to human injury and other serious problems.
Many a time, silly mistakes cause a system to fail. For example, in an observation3, the robot's software crashed immediately after it started; and the robot stopped when it has to perform a specific operation. The root cause of this behaviour was the error caused by not checking the range of allocated memory in the object's constructor, and the developer used "sprintf" instead of "snprintf".
Even during debugging, this error went undetected. Unfortunately, such software issues are not rare, and various studies/surveys conclude that software is more prone to failure than hardware. Therefore, there are many safety- and security-based issues addressing which a developer needs to build reliable software. One way to make the robotics software more reliable is by following standards, which help developers follow best practices and avoid bugs while writing robotics software.
Safety and Security Standards for Industrial robots and Collaborative robots
When we consider safety standards for robotics, there are different standards for different applications. For example, for industrial robots' safety standard is ISO 10218:2011, for personal care robots' safety standard is ISO 13482:2014, and for collaborative robots' (COBOT) is ISO/TS 15066:2016. If we talk about security standards, then IEC 62443 is one of the essential standards to be followed.
COBOTs share the workspace with humans and interact with them, and hence, their safety is much more critical because any malfunction in these robots can cause severe harm to humans. For example, on 13 February 2019, a worker of Omnipure Filter Company in the U.K. accidentally entered the cycling area for a robotic arm, and the arm censor was tripped. The employee was pinned against a 400 Fahrenheit degree mold that was exiting the oven, and he sustained severe burns4. So, some guidelines should be followed while developing machines that work with humans so that such cases can be avoided. Thanks to the efforts of TC 299, an ISO committee that is very active to develop high-quality standards for the robotics domain, excluding toys and military applications. Let us try to understand the content of ISO 10218:2011 and ISO/TS 15066:2016 standards.
ISO 10218:2011 |
ISO/TS 15066:20165 |
It contains requirements for industrial robot and ISO 10218-2:2011 contain industrial robot system requirement along with controlling hazards specifications. |
It ensures that while robots work in the same space as humans, any accidental incident with robots should not harm humans by providing guidelines for the implementation and design of such a collaborative working environment. If a robot fulfils all requirements and follows ISO/TS 15066 then a separate workspace for humans and robots may not require6. |
It focuses on:
|
It focuses on:
|
For more detail, refer to the below table which has the list of various safety and security standards for robotics7:
Standard Number |
Domain |
IEC 61508 |
Functional safety of electrical/electronic/programmable electronic safety-related systems. |
ISO 9283:1998 |
Manipulating industrial robots - Performance criteria and related test methods |
ISO 9409:2004 |
Manipulating industrial robots – Mechanical interfaces |
ISO 9787:2013 |
Robots and robotic devices - Coordinate systems and motion nomenclatures |
ISO 9946:1999 |
Manipulating industrial robots - Presentation of characteristics |
ISO 10218:2011 |
Robots and robotic devices - Safety requirements for industrial robots |
ISO 11593:1996 |
Manipulating industrial robots- Automatic end effector exchange systems |
ISO/TR 13309:1995 |
Manipulating industrial robots - Informative guide on test equipment and metrology methods of operation for robot performance evaluation in accordance with ISO 9283 |
ISO 13482:2014 |
Robots and robotic devices - Safety requirements for personal care robots |
ISO 14539:2000 |
Manipulating industrial robots- Object handling with grasp-type grippers |
ISO/TS 15066:2016 |
Robots and robotic devices - Collaborative robots |
ISO 18646:2016 |
Robotics — Performance criteria and related test methods for service robots |
ISO 19649:2017 |
Mobile robots |
ISO/TR 20218:2018 |
Robotics — Safety design for industrial robot systems |
ISO 22166:2021 |
Robotics — Modularity for service robots |
ISO/TR 23482-:2020 |
Robotics — Application of ISO 13482 |
IEC 62443 |
Industrial communication networks - IT security for networks and systems |
Coding Standards: For safety and mission-critical applications, it is prefered to follow functional safety standards such as IEC 61508 for industrial systems. These standards recommend following a safe subset of programming language (such as MISRA C), depending on the criticality level (highly recommended for SIL 3 & SIL 4 applications as per Table A.3 of IEC 61508).
MISRA C is a language subset of the C programming language (often referred to as a "coding standard") that is developed and maintained by the Motor Industry Software Reliability Association (MISRA). It is designed to promote the use of the C language in safety-critical embedded applications, and it provides invaluable assistance to any organization looking to protect themselves from the problems inherent in the inadvertent or deliberate misuse of the C language. There are other coding standards as well such as SEI CERT C, BARR-C, etc. There are also vulnerability dictionaries like CWE and NVD.
Industry Best Practices: Additionally, a degree of confidence towards safety & security of robotics applications can be built by referring to the 7 industry best practices below.
-
NIST Framework for Improving Critical Infrastructure Cybersecurity
-
Top 10 Secure Coding Best Practices by SEI CERT
-
NASA's Power of 10: Rules for Developing Safety Critical Code
-
Microsoft's Security Development Life Cycle
-
CWE's Top 25 Most Dangerous Software Weaknesses
-
IEEE's Avoiding the Top 10 Software Security Design Flaws
-
NIST 8151: Dramatically Reducing Software Vulnerabilities
Conclusion
Addressing safety and security is a crucial step to work upon for industrial & collaborative robots. There is no single bullet to address safety & security issues; however, reference to the above-mentioned standards and industry best practices can certainly enhance the degree of confidence towards dependable robotics systems. We need to always ensure to architect safety & security into the robotics system design & development as it cannot be a bolt in later.
References:
-
https://www.industryarc.com/Report/18571/india-industrial-robotics-market.html
-
https://www.mordorintelligence.com/industry-reports/robotics-market
-
https://www.osha.gov/pls/imis/accidentsearch.accident_detail?id=113594.015
-
https://www.iso.org/committee/5915511/x/catalogue/p/1/u/0/w/0/d/0
The content & opinions in this article are the author’s and do not necessarily represent the views of RoboticsTomorrow
Comments (0)
This post does not have any comments. Be the first to leave a comment below.
Featured Product
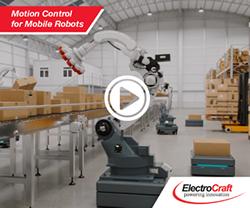