Ultrasonic uses energy from microscopic vibrations of a blade to pass easily through the material and offers a more effective solution for cutting cheese and other food products. When paired with automation, ultrasonic technology can deliver precise and accurate cutting.
Making “cheddar” With Industrial Automation - Achieving 83 Per Cent Waste Reduction in Food Manufacturing
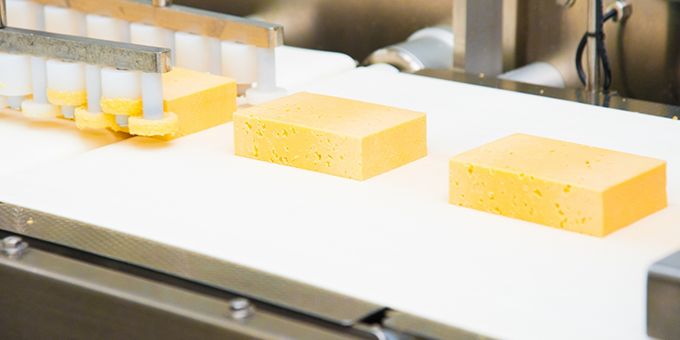
Case Study from | TM Robotics
Cheese. It crumbles, it cracks, it gets pressed out shape. Cutting the perfect slice is no mean feat — especially in manufacturing applications. Food machinery manufacturer, Elliptical Design, designed a new ultrasonic cutting system to solve this challenge and turned to industrial robot supplier, TM Robotics, to increase efficiency and cut waste.
Robots are a familiar sight in food manufacturing plants, but usually only in end-of-line (EOL) or packaging functions. Elliptical Design, a British design and manufacturing company, creates bespoke machine solutions for the food industry and wants to help food manufacturers use automation in food handling too.
Elliptical Design was approached by a leading UK cheese manufacturer to create a cutting system to help them reduce waste and increase throughput.
Cheese is traditionally hard to cut in manufacturing. Cutting with a knife can result in breakage, and even the drag of the knife can cause damage. Ultrasonic cutting provides a method for manufacturers to complete product-worthy cuts, without damage. Precise cuts when portioning cheese are important, not just to reduce the amount of cheese wasted due to damage, but also to improve aesthetics. For the food sector, product uniformity is also essential to pass quality checking and meet legislation related to food quantity.
Ultrasonic uses energy from microscopic vibrations of a blade to pass easily through the material and offers a more effective solution for cutting cheese and other food products. When paired with automation, ultrasonic technology can deliver precise and accurate cutting for cheese manufacturers.
To deliver this precision Elliptical Design bought industrial robots into the process, using machinery from TM Robotics.
TM Robotics is the UK distributor for Shibaura Machine, formerly Toshiba Machine. With over thirty years’ experience in the robotics industry, TM Robotics offered the expertise Elliptical Design needed to ensure this complex project was a success.
Robots: Functional, flexible, fast
For this particular cheese manufacturing system, robots were installed for three different functions.
The first two are pick and place applications with vision and conveyor tracking capabilities. One application involves the robot picking up a large, half moon piece of cheese and putting it into a plastic packaging, while in the other, the robot picks up three small pieces of cheese at once and putting them into packets. For these applications, TM Robotics supplied its THP700 SCARA robot — the strongest and fastest option in Shibaura Machine’s SCARA range.
The THP700 SCARA robot is a powerful robot that can work at full speed without thermal overload. The THP700 has a fast cycle time of 0.3 seconds and is capable of 120 cycles per minute in 24-hour continuous operation. It has an arm length of 700mm and a maximum payload of 10kg — ideal for the demands of food production.
As these applications involved handling raw food, the THP700 robots delivered have an IP65 rating, meaning they are suitable for food production.
The final robotic application was the ultrasonic cutting system. Within this process, the robot picks up a ten-kilogram piece of cheese and moves it onto a weigh station, and then a cutting station. There, it is cut in half using precise and accurate ultrasonic technology.
For this system, TM Robotics supplied the TV1000H 6-axis industrial robot. A strong yet flexible robot with an IP rating of IP65, or IP67 in some models, it has a maximum cycle time of up to 0.9 seconds and repeatability of ±0.03mm.
“For us, all equipment needs to be food grade,” explained Phill Thompson, managing director of Elliptical Design. “Next, we look at the functionality, speed and precision of the robot. Our projects are about improving efficiencies for our customers, so we need robots like Shibaura Machine’s, that can bolster the improved precision delivered by our own ultrasonic technology.”
Finding the right solution
The collaboration has yielded great results but was not without its challenges. One such challenge involved the fine-tuning of the robot’s vision system.
“Shibaura Machine robots are generally easy to integrate with vision systems,” explained Nigel Smith, managing director of TM Robotics. “The challenge here was to ensure that the robot was picking up cheese in the right place and being able to put it down as accurately as needed — there’s a very slim margin for error in plastic tote placing.
“When the cheese is placed on the conveyor its actually still slightly soft. Rather than a round shape, it has a slightly flat side. Using our direct partnership with Shibaura Machine, the team’s engineers found the right algorithm in the vision programme to ensure the robot could identify non-uniform shapes and pick the cheese accurately.”
“When our integrators couldn’t solve this problem, we turned to TM Robotics for support.” commented Thompson. “They drew on their extensive knowledge bank and put us in touch with experts in the US and Japan.
“The reason customers come to us is because they cannot find off-the-shelf solutions to their manufacturing challenges. Because of this, it’s vital that our partners know their stuff.
“TM Robotics is passionate about its work and get as much satisfaction from the end result as we do. When choosing a supplier, it’s essential that we can trust this level of commitment and expertise — you can’t really put a value on that.”
On the factory floor
Prior to the project, the manufacturer’s production process was almost entirely manual, and took between four and five days to produce the quota of cheese needed each week.
Now, with Elliptical Design’s bespoke ultrasonic cutting system and Shibaura Machine robots, the same production quotas are reached in only two days, due to increased throughput and reduced waste.
As for Elliptical Design, the company has since ordered another Shibaura Machine robot to build a demonstration system for their headquarters, to showcase the benefits of industrial robots to customers in the food industry.
For food manufacturers, investment in industrial automation for food handling may seem like a big step. But, with an impressive impact on productivity and waste, it’s one that’s certainly worth taking.
The content & opinions in this article are the author’s and do not necessarily represent the views of RoboticsTomorrow
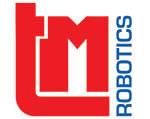
TM Robotics (Americas) Inc
TM Robotics, in partnership with Shibaura Machine, formerly known as Toshiba Machine until 1st April 2020, offers a comprehensive range of industrial robots ideally suited for high-precision assembly, machine loading/unloading and material-handling applications that can be dust proof, clean room, or IP65/67. The company's extensive product line starts with a Cartesian solution available in thousands of combinations from single actuators to four-axis solutions; six-axis solutions that can include precise vision-control; and a complete range of SCARAs from low cost to the industry-leading SCARA with 1200-mm reach that can carry up to 20 kgs. TM Robotics sells and services robots throughout Europe, the Middle East, India, Russia, and Africa, as well as North, Central, and South America, from headquarters in Hertfordshire, England and Elk Grove Village, IL, USA. For more information, visit www.tmrobotics.com or follow us on Twitter, LinkedIn and YouTube.
Other Articles
Giving lens cleaning cloths a robotic hand - Robotic automation for textile processing
Investing in the UK’s injection moulding sector - The case for all-electric machines and robotic integration
Robotic solutions for pharmaceutical packaging - Automated system addresses key limitations of manual processes
More about TM Robotics (Americas) Inc
Comments (0)
This post does not have any comments. Be the first to leave a comment below.
Featured Product
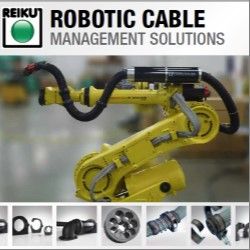