Bottomless conveyors, also called side-gripping conveyors, provide a simple solution for accessing the underside of a product for a range of applications. These applications include inspection, printing, labeling and edge sealing.
6 Ways to Use a Bottomless Conveyor
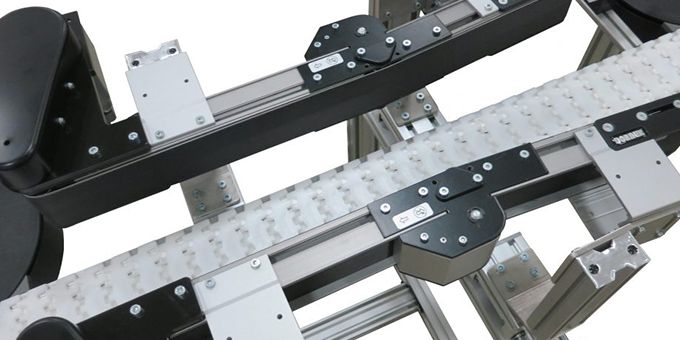
Article from | Dorner Mfg Corp
With bottomless conveyors, two conveyors—either preset or sold with an adjustable option for a variety of product sizes—are mounted on the edge. If using a conveyor with an adjustable option, once the conveyors are adjusted to the proper width, products are “locked” in place and can transfer to the next phase of your production line.
Bottomless conveyors are also used in line over another conveyor to pace product.
Here are 6 possible applications where a bottomless conveyor can enhance your production line.
1. Labelling Application
Businesses needing to add labels to boxes or inspect boxes turn to Dorner and its bottomless conveyors to create ease and speed with these critical processes. Boxes can move along the line, with labels added to the tops and bottoms of boxes.
2. Product Inspection
3. Box Sealing
Box sealing is a function that is made easy when bottomless conveyors are utilized in a facility. Boxes are conveyed with sealing tape applied to the tops and bottoms of boxes, helping ensure the production line moves along at an efficient rate.
4. Printer Coding
Bottomless conveyors are ideal when businesses need to apply inkjet or laser printer coding on the underside of bottlers or containers, for example. Oftentimes, this coding involves product freshness dates, in the case of food products, beverages and pharmaceutical drugs.
5. Product Pacing
For accumulation where product needs gapping or pacing, a bottomless conveyor can be an easy solution. The squeezing effect of the bottomless conveyor can slow the product down if they are running at a slower speed than the mainline conveyor.
6. Bottling Operations
One Dorner customer faced challenges in consistently sealing wine bottles its facility produced. This customer needed to evenly apply heat completely around the seal at the top of the bottle.
The Dorner team used a 2200 Series conveyor along with a mainline chain conveyor. Mounted on its side, the 2200 Series conveyor ran parallel with the main line conveyor.
A high-friction Dorner Type 64 belt enabled the conveyor to spin the bottle a complete revolution as it moves through a heat tunnel. This full spin enables heat to be evenly applied around the whole seal.
The content & opinions in this article are the author’s and do not necessarily represent the views of RoboticsTomorrow
Comments (0)
This post does not have any comments. Be the first to leave a comment below.
Featured Product
