Mobile robots in warehouses help companies increase their output and meet customer demands, allowing the companies to maintain a competitive advantage. Specific characteristics make warehouse environments particularly well-suited to these mobile machines.
Signs Your Warehouse Environment Needs Mobile Robots
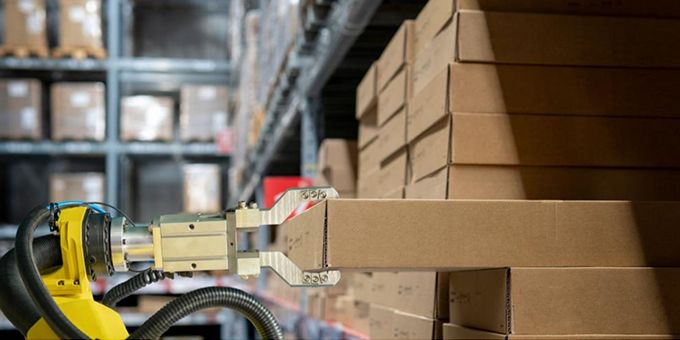
Article from | OTTO MOTORS
Here are a few key identifiers that will let you know whether mobile robotics will work well in your operation:
1. Materials Handling Is a Top Task for Workers
If your workers spend substantial amounts of time moving components and finished products within the warehouse, a mobile robot, particularly an Autonomous Mobile Robot (AMR), could help. When an AMR does the full task of transporting materials, human workers can focus on more rewarding tasks that let them use their brain power and unique human abilities to contribute to a company's success.
Ryder, a business specializing in top-down supply chain solutions, installed an assortment of new technology in one of their facilities, including warehouse robots. Internal data showed the machines caused a 25% productivity increase and 20% reduction in operating expenses by cutting employee travel time.
If you're ready to assign workers to higher-value tasks, and let mobile robots reduce operational costs, consider adopting industry 4.0 technology in your facility. Be open with employees about how robots will supplement their work, not replace it.
2. You Want to Reduce Dependence on Conventional Forklifts
Safety is a big concern in factories and warehouses, and is often a driving force behind the decision to adopt automation. Each year in the United States, nearly 100 workers are killed and another 20,000 are seriously injured in forklift-related incidents. OCEA and Industrial Truck Association report that the average life expectancy of a forklift is 9 years, and there is a 90% chance of a serious accident over the course of its life.
If your facility is experiencing safety issues with current material handling technology, such as forklifts, it is time to consider the benefits of automation.
Cabka North America purchased robots for its 400,000 square-foot facility to reduce forklift traffic on the production floor. By only using collaborative mobile robots in the staging area, Cabka increased its plant’s safety while also maximizing efficiency levels. At Cabka, a single robot travels about three miles per day while supporting a single production line.
3. Your Load Requirements Do Not Exceed a Mobile Robot's Specifications
Buying a new piece of warehouse equipment requires you to ensure the tasks you have in mind match what the machine can do. For example, if buying a boom lift, necessary height and mobility are two specifics to investigate before purchasing. If you're interested in bringing mobile robotics to the warehouse, check the payload capacity — the maximum amount the machine can safely carry — first.
For example, OTTO Motors’ OTTO 1500 can carry 1500 kilograms and has the ability to attach a lift, conveyor or interface with other technologies. Often, speaking with the robotics or automation provider is the best way to learn which products will work for you. Many mobile robots weigh several thousand pounds once loaded, and staying aware of the payload capacity will help you make the right decisions for your own operation.

OTTO 1500 is able to lift 1500 kilograms, and can attach a conveyor, lift, or other integrated robotics solution.
4. You Want a More Flexible and Efficient Operation
Mobile robots can empower companies to progress from a fixed infrastructure to a flexible one. Autonomous mobile robots (AMRs) do not need guides on the floor. They move freely around facilities and can avoid obstacles in real-time. These robots also offer a high level of flexibility and efficiency, and can help meet rising customer demands for customization and faster delivery.
Even if your facility has many barriers and blockages on pathways, AMRs can autonomously detect and navigate around these barriers, creating little need for redesigning existing infrastructure. This means AMRs and other robotics can be up and running within your facility quickly, to ensure fast ROI and that benefits are experienced quickly.
The content & opinions in this article are the author’s and do not necessarily represent the views of RoboticsTomorrow
Comments (0)
This post does not have any comments. Be the first to leave a comment below.
Featured Product
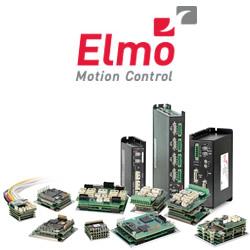