As we move toward a new normal, robots may play a big role in helping businesses recover in the post-COVID world. Three automation experts weigh in on these trends and how COVID-19 is impacting key industry segments.
The Future of Manufacturing: What to Expect
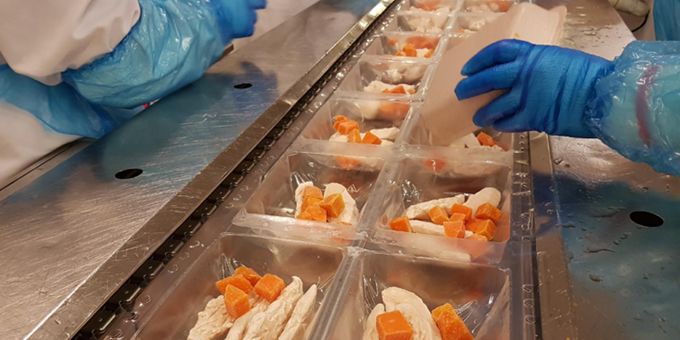
Article from Milane Haboon | Soft Robotics Inc.
In this new social distancing era, the Coronavirus is changing the way we work and sparking new trends in manufacturing. As we move toward a new normal, robots may play a big role in helping businesses recover in the post-COVID world. Three automation experts weigh in on these trends and how COVID-19 is impacting key industry segments; integrators, Original Equipment Manufacturers (OEMs), end-users, and manufacturers.
1. What are you seeing right now as it relates to these segments? How has COVID-19 most impacted these segments?
Jeff Burnstein, President of A3: End-users seem to be giving lots of thought to how automation will help them in the future. Some of the issues that the pandemic has raised include how to reduce “touches” of products and packaging, how to create more social distancing, and how to keep plants up and running when people are required to shelter at home.
Advances in grippers should help robots reduce touches in manufacturing, warehousing, and logistics going forward. Collaborative robots and mobile robots seem particularly well-suited to helping create social distancing. Adding more robots to manufacturing and logistics operations would help companies stay up and running or be more productive if we have a return to “stay at home” requirements during the next wave of this virus or in a future pandemic.
Bryan Griffen, Director, Industry Services of PMMI: For those companies considered essential [that have already automated], many are seeing production levels never before attained. This is particularly apparent in the retail food, beverage, pharma, and household care sectors where demand for production is at an all-time high. These extraordinary levels have been achieved with workforces dedicated to their business plus a focus on the highest-selling SKUs. Focusing on only the most in-demand products has enabled longer runs and reduced changeovers. OEMs, integrators, and contract packagers that cater to these essential industries are enjoying increased opportunities as well since many of the manufacturers in these sectors are actively looking for ways to increase production capability.
“In short, we are living in the next big automation boom!”
Mark Chiappetta, COO of Soft Robotics: Despite a high prevalence of robotic automation in manufacturing, widespread adoption has been relatively slow in numerous industry segments. Large companies in these segments have either been unwilling to make the upfront capital investment or have been unsuccessful to automate because current technologies have not enabled such processes. Instead, these companies are having to rely on human labor to bring their products to market.
Along with macro trends like increasing and aging of the population, upskilling of the workforce, government focus on food safety modernization, Covid-19 has strained the supply of human labor to the breaking point and has made it near impossible for food producers and processors to keep up with the demands of production. These conditions create opportunities for the manufacturers of automation technologies and for system builders. In short, we are living in the next big automation boom!
2. What are you anticipating post-COVID looks like for these segments? And perhaps, what might the transition look like?
BG: Focusing on the essential industries and the suppliers that serve this sector, the transition to a post-COVID status is expected to see some reduction in spend and manufacturing volume prior to resuming more normal levels. In general, all market segments will need to have their operations in prime condition for possible response to a new surge in demand later in 2020.
MC: Early signs point to an impending boom in automation adoption. At Soft Robotics we are already seeing a significant uptick in inquiries from end-users as well as system builders about our highly-adaptable products. There’s a unique sense of urgency at this time.
We believe that within 18-24 months we will be shipping more product than we planned for as food processors, CPG producers, and logistics providers begin transitioning from a strained human-powered operation to robotic automation. Pairing highly-skilled human workers with robots will enable higher rates of production with better quality, consistency, and all within a safer work environment.
3. What are you hearing from manufacturers/end users during this time relating to robotics and automation?
BG: There is a renewed interest by both manufacturers and OEMs in the ability to remotely access installed equipment for the purpose of troubleshooting and maintenance analysis. Manufacturer protocols prohibit most outside technicians (e.g. from OEMs and integrators) to enter their facilities during the pandemic. Remote connections to installed equipment can reduce the need for external technician intervention onsite. Both manufacturers and OEMs are realizing that remote troubleshooting and assistance can be very effective and are thus looking to increase this trend of remote access in the post-COVID reality.
Those using these technologies and tools are achieving the necessary project management steps without the risk of sending large teams to the OEM’s site. As with remote access, manufacturers and OEMs anticipate continuing to use these tools and techniques in the post-COVID reality.
4. What do you think needs to happen next?
“As experts, we need to take the fear and friction out of robotic adoption for end-users who are hesitant to automate.”
JB: What I think end-users need to do now is identify areas where they think robots and automation can help them and begin the process of reaching out to suppliers.
There are many resources available to these companies, and a great place to start would be to visit www.a3automate.org and www.robotics.org.
Experienced automation users should be examining their operations now to determine new applications for robotics. They should be contacting system integrators now to help them be ready to go once operations are at 100% again around the world. A great place to start would be by looking at the system integrator members of the Robotic Industries Association, many of whom are Certified Robot Integrators.
MC: Gripping, machine vision, and AI technology providers need to work closely with system builders to leverage robotic automation that will drive productivity.
As experts, we need to take the fear and friction out of robotic adoption for end-users who are hesitant to automate. We know that robotic automation makes sense for manufacturing–it’s easy to implement, extremely reliable, and cost-effective. It’s up to us to guide end-users and present the clear economic benefits, improved product quality, and increased worker safety that comes with automation.
The content & opinions in this article are the author’s and do not necessarily represent the views of RoboticsTomorrow
Comments (0)
This post does not have any comments. Be the first to leave a comment below.
Featured Product
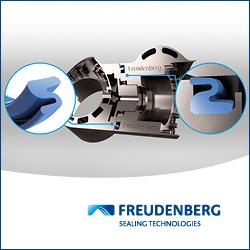