The defence sector is a valuable contributor to the economy, providing a large number of jobs and investing in a number of industries. However the relationship is mutualistic, with advancements in industry benefitting the defence sector.
Precision Micromotors in Defence Robots
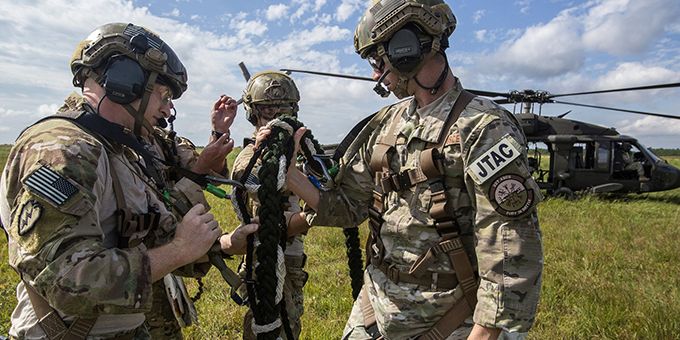
Stewart Goulding, Managing Director | Electro Mechanical Systems Ltd
In medieval times, castles were built with a number of defence systems to protect inhabitants, such as moats, draw bridges and tower lookout points. Security measures have since progressed, and advancements in technology have allowed the development of electronic defence and intelligence systems. Here, Stewart Goulding, managing director at precision drive system supplier, Electro Mechanical Systems Ltd, explains how precision micromotors are aiding the advancement of defence electronics.
The defence sector is a valuable contributor to the economy, providing a large number of jobs and investing in a number of industries. However the relationship is mutualistic, with advancements in industry benefitting the defence sector. In particular, powering electronic defence equipment, such as remotely operated vehicles, with high precision motors aids the sector’s success.
Remotely operated vehicles
Remotely operated vehicles (ROVs) are used to carry out dangerous tasks or activities in hazardous environments. On land, ROVs may carry out missions such as exploration, mine reconnaissance or even explosive ordnance disposal (EOD).
ROVs can also be used in underwater environments to eliminate the need to endanger a diver or to reach areas that are difficult to access. Underwater, ROVs may carry out additional tasks, such as hull inspections and retrieval of lost equipment. ROVs feature robotic arms to hold equipment and handle explosives, and possess a rotating camera for the operator to see the surrounding environment and the task being performed.
Using a compact, highly efficient yet powerful ironless rotor motor allows precise and agile movements of the arms and camera, while adding minimal weight to the vehicle. A lower weight allows the vehicle to move through water or across rough terrain with ease and in combination with the high efficiency reduces load on the onboard battery, which in turn increases the usable operating time of the vehicle.
Wearable equipment
Exoskeletons are wearable suits powered by a combination of electric motors, levers, hydraulics and pneumatics, which assist limb movement. Sensors are installed into the suit to record the movements of the user, with the information collected being fed to the electric motors that power the movements.
Applications of exoskeletons in the defence sector are still in the development stage but are being trailed out in a number of nations. Defence exoskeleton prototypes are showing the potential to allow users to go beyond their physical capability, performing with higher strength and endurance.
Exoskeletons may also protect the wearer from physical strain, which is a common problem in the defence sector. These qualities may help with tasks in the defence sector such as long-distance trekking, but the full potential of using these exoskeletons in a combat sense is not yet certain.
The motors in these suits used must be lightweight to allow quick and agile movements, and powerful to propel limps forward. The motors must also have high precision to work to together to create synchronised movements.
Moats and walls may have protected populations in medieval times, but the increasing complexity of global safety threats calls for more sophisticated defence technology. Electronic defence equipment designed with durable, precision motors perform with accuracy and reliability, helping to keep defence personnel and public citizens safe.
The content & opinions in this article are the author’s and do not necessarily represent the views of RoboticsTomorrow
Comments (0)
This post does not have any comments. Be the first to leave a comment below.
Featured Product
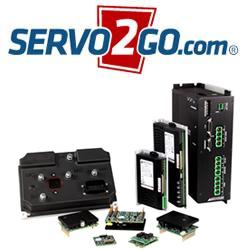