Integration is about adding value for customers by designing products that include multiple parts of the solution into a single instrument. For motion control hardware, this can mean combining the mechanics along with a motor, encoder, limit sensor, driver, and controller.
Simplifying Motion Control through Integration of All System Components

Q&A with Mike McDonald, Applications Engineering | Zaber Technologies Inc.
Tell us about yourself and your role with Zaber Technologies Inc.
I’ve been an Applications Specialist at Zaber Technologies for 8 years. Zaber designs and manufactures motorized positioning products, such as linear stages and actuators, with a focus on Simplifying Motion Control. We serve a number of industries, including photonics and optics and lab automation, which often require high accuracy and precision.
Our Applications Specialists assist our customers with any pre-sale or post-sale technical support, from helping select the best solution for a requirement to troubleshooting any problems down the road. We also work with Product Designers to help make the best solutions to tomorrow’s requirements.
You said, "Zaber focuses on Simplifying Motion Control." How are you working towards this and why?
We make this our focus because many people, especially in scientific and laboratory industries, have a need for automated motion but either don’t specialize in automation and controls or don’t have the time to devote to it. For them, having a simple solution with a shallow learning curve adds a lot of value.
This principle of continually simplifying is applied across all aspects of our company. For example, we keep the ordering process simple by listing prices on-line, offering fast lead times and no minimum quantities, and allowing access to information with no log-ins. We simplify the support process by making it easy to talk to a technical expert to discuss applications and by offering comprehensive specifications and test data for our products. Controlling the devices is often one of the most challenging and complex pieces of the puzzle, so we offer an intuitive and user-friendly command set, comprehensive APIs and examples for programming, and free, open-source software for basic control.
The number one way that we are simplifying motion control is that we sell an integrated solution, which is something that helps us to offer a lot of the previously mentioned benefits.
What does integration mean for Zaber, and why is it important?
Integration is about adding value for customers by designing products that include multiple parts of the solution into a single instrument. For motion control hardware, this can mean combining the mechanics along with a motor, encoder, limit sensor, driver, and controller. This level of hardware integration is coupled with firmware and software designed specifically for the device to provide a complete, cohesive experience.
Integration is important for Zaber because it supports the goal of simplifying motion control. Each component we build into the device is a decision that the customer doesn’t need to make. For example, when Zaber offers a linear stage with a built-in motor, the customer doesn’t need to have the expertise in choosing the best coupler style for the system or doesn’t need to know what motor torque is optimal to get good performance from the system without reducing lifetime. These design decisions are made by Zaber’s motion control experts, and each decision is one that we are offloading from the customer so they can instead focus on applying their expertise where it will add the most value to their system.
We’re also able to offer a comprehensive list of performance specifications of our devices because we know the complete set of parts that will be working together. A supplier only selling a motor driver may be able to give a theoretical peak motor speed, but without knowing the traits of the specific motor and the adjoining mechanics, it’s impossible to give the empirical linear speed limit, which the end user cares about.
Not only is the implementation of the product into a design simplified, the process of purchasing the parts that follows is also simplified. The effort and time working with several different suppliers adds up (navigating several websites and product manuals, setting up accounts with different vendors, managing different lead times and payment terms); bringing it all under one company can make it much easier (as long as that company is easy to work with, which Zaber strives to be).
Finally, having a single technical support contact who is an expert at all aspects of the product also allows a more holistic troubleshooting process. Otherwise, a user would need to contact multiple support people from different companies that are only experts at only one aspect of the system.
Can you describe the process to set up and install a Zaber motion control device?
Integration helps make set-up extremely easy. For devices that have the controller and driver built-in, almost all settings (such as the motor current, limit sensor behaviour, and travel limits) are ready to go out of the box. The user just needs to plug in the power supply and a USB connection to start controlling from software. A knob is included on many models, which allows the user to move the device even before software is involved. If there’s more than one device in the system, they can connect in a daisy-chain to share a single power supply and USB connection.
We also offer models that don’t have the controller and driver built-in. These can either be used with third-party drivers or with Zaber’s multi-axis X-MCC controllers. When used with an X-MCC controller, we continue to simplify the experience by including a feature called Auto Detect. Memory on-board the motor allows the controller to detect when it’s plugged in and identify the model so that optimal settings can be established automatically.
Are there trade-offs in sourcing an integrated solution?
When comparing options, it’s useful to think of the level of integration as a spectrum. On one end is the do-it-yourself option, where you select, source, and assemble each individual component yourself to build a system. On the other end you can contract a systems integrator to design, build, and deliver a customized system for you. In the middle are options where you use components that come built together (for example a motor with an encoder and drive built-in, or a stage with the motor and ball screw included), but you also take some responsibility for the design.
The DIY end can be cost effective when considering the price of the parts, but will require by far the most time investment in designing the system. Conversely, by working with a systems integrator you offload all of the design time but end up paying for it on the overall system cost. When considering either the time or price investment in isolation, the integrated option doesn’t look optimal; you still end up with some design time, and you’re likely paying a higher price than sourcing the parts individually. When considering them together though, using integrated components is often the most attractive option.
One trait that the DIY and systems integrator options share though is that you are getting a solution that is more tailored to the specific application requirements. A trade-off of using integrated parts is there are typically a limited number of standard options, and you need to choose the one that’s the closest fit. This may result in a solution that’s larger or heavier than a completely customized one would be, or it may have more features or performance than you otherwise need.
At the end of the day, the best option will depend on a number of factors about the application requirements and the capabilities of the design team. What level of automation expertise is available? What is the budget for the system? How many systems need to be built? How quickly it needs to be deployed? Are there aspects of the system that require a high level of customization? Suppliers at all points along this spectrum should be able to assist in answering these questions and making recommendations about what kind of options make the most sense.
What role does integration play in expanding the field of robotics and automation?
What drives the continued growth of the robotics and automation industries is a continued lowering of the barrier to entry. More and more applications make sense to automate as technological advances make more complex processes possible, while costs continue to decrease. A barrier to entry for some people continues to be the expertise required to implement a solution though. Many otherwise straightforward requirements for motion control are still done manually, not due to the cost of the solution, but the cost from the complexity of figuring out how to implement the solution. By offering a wide range of integrated solutions that end users without an automation background can quickly and easily deploy, Zaber is playing an active role in expanding robotics across new industries.
The content & opinions in this article are the author’s and do not necessarily represent the views of RoboticsTomorrow
Comments (0)
This post does not have any comments. Be the first to leave a comment below.
Featured Product
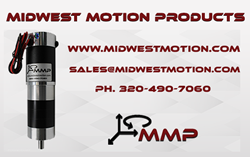