Justin R. Bessette, Manager of Technology at Parker LORD, Microstrain shares with us his thoughts on how Parker LORD is managing through the pandemic as well as insights into what the future of Robotics and Automation may be.
Business Perspectives and the Impacts of COVID-19 - Q&A with Parker LORD
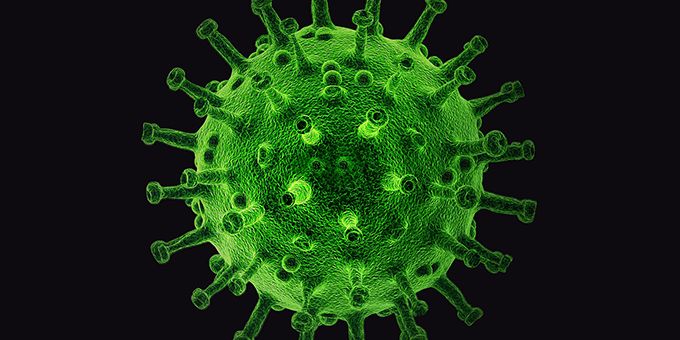
Q&A with Justin R. Bessette, Manager of Technology | Parker LORD, Microstrain
How was your workforce directly impacted by COVID-19?
Our top priority is the safety, health, and well-being of our employees, customers, and communities – we are doing everything possible to balance this while maintaining productivity and our ability to support our customers. This focus has impacted our employees’ day-to-day on many levels. For instance, our production teams have adjusted to working in staggered shifts to minimize contact; our engineering teams are utilizing video conferences and emails more; and employees are working from home where possible. While working remote has temporarily forced us to lose access to being “in the moment” with each other, we are relying on collaborating virtually with our colleagues and customers alike. Collaborating with our customers has always been a service we offer – which we believe leads to better product performance and reliability. Virtual collaboration enables us to still provide hands-on customer service, without using our hands.
How are you seeing COVID19 changing the way people do business?
Video conferencing through Teams, Skype or Zoom is the new normal. Travel has declined, and everyone is more available – in some ways, things get done faster as we can meet quickly through phone calls or video conferences. Customers are becoming more dependent on existing content on websites and paying more attention to social media, which offers a lot of value to them and showcases the opportunities we have to make an impact on their businesses.
Have you changed your use of manual assembly or production setup in the wake of COVID-19?
No – we use robotic automation as much as possible. At the end of the day, we still need humans to do critical, sometimes unpredictable, tasks. Our production teams have adjusted to working staggered shifts to minimize contact and ensure safety.
What type if any supply chain disruptions have you seen and can you share an example of how you are overcoming these?
At this time, we have not had any significant disruption to our supply chain. While we have seen increases in lead times, particularly from products manufactured overseas, we are well-positioned to serve our customers and we have contingency plans in place to address any unforeseen circumstances or disruptions.
As of now, have you seen any effects on the robotics market? If so, how?
We’re anticipating it and we are ready. With COVID-19, we predict the use of delivery drones, recon and mapping will increase and become the new norm. We design and produce MicroStrain inertial sensors that are used in robots and aid in delivery, mapping and surveillance activities. Our Inertial Measurement Units and Inertial Navigation Systems are designed to enable quick time to market development. We offer IMU/INS integration with our recently updated Robot Operating System (ROS) drivers for ease of use. By using our sensors, we have reduced development time while also offering top performance reliability.
How do you think people’s view of robotics and automation will change as a result of this pandemic?
We’re going to see more acceptance of robots delivering goods and having robots assist humans in systematic tasks. It will become the new norm.
Moving forward what are you anticipating and how are you preparing for those challenges?
As a player in the growing robotics, drones and unmanned vehicles industry, we are able to stay at the forefront of future development. This increase in demands helps us maintain our productivity. Moving forward, we expect to see an increase in demand for sensors for use in robotics and unmanned vehicles.
How do you anticipate adjusting to tradeshow cancellations? How do you anticipate continuing to reach out to prospective customers?
Lack of trade shows has led us to transition to online publications, increased electronic content marketing (including customer emails and social media posts) and more email and
Can you share what you have learned about your business and its employees from this?
Our workforce is resilient. They have adapted to forced, unpredictable changes with little complaint and minimal work output effect. I feel that some interesting changes in how we do business will come of the COVID-19 situation. At the same time, we are ready to be back in the office, collaborating and designing products that enable better data acquisition for our customers.
The content & opinions in this article are the author’s and do not necessarily represent the views of RoboticsTomorrow
Comments (0)
This post does not have any comments. Be the first to leave a comment below.
Featured Product
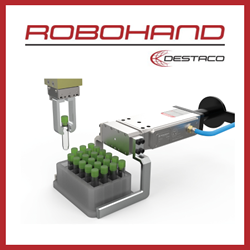