One of the most often overlooked parameters of direct current motors (both brush and brushless) is the Km or motor constant. The motor constant (expressed as Km) defines the ability of a motor to transform electrical power into mechanical power.
Understanding the Motor Constant in DC Motor Sizing
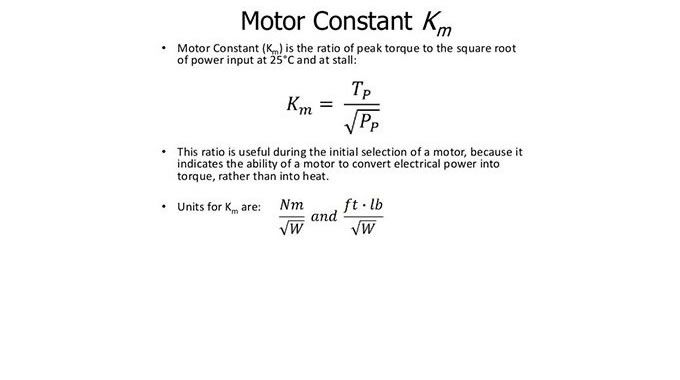
Warren Osak | Servo2Go
One of the most often overlooked parameters of direct current motors (both brush and brushless) is the Km or motor constant. The motor constant (expressed as Km) defines the ability of a motor to transform electrical power into mechanical power and is a valuable tool for any project or application engineer looking to recommend a “best fit” replacement for an existing motor. Although the motor constant does not address thermal or other viscous losses, it is still useful for selecting a replacement motor that’s in the “ballpark.”
The motor constant defines the ratio of the motor torque (mechanical power) to motor input power (electrical power). Why is the motor constant important? Because, physical motor size can be deceiving! Although it may be intuitive to think a larger motor will be more powerful than a smaller motor, this may not always be the case. How can we then determine which is the more powerful motor? By calculating and comparing the motor constant of both motors.
Many times it is not possible to provide complete motor specifications to a vendor making it difficult, if not impossible, for the vendor to recommend a best fit alternative. However if the customer can share the Kt and Rt of their existing motor, then by using the equation for calculating motor constant, a relatively good recommendation can be made.
The Motor Constant is calculated by the following equation (in English units): Km = Kt/√Rt - where Kt is the torque sensitivity (oz.-in./amp) and Rt is the terminal resistance (ohms)
Units for Km are oz.-in./√watts (in English units)
Summary:
- As can be seen from the above equation, the lower the motor’s resistance the higher the Km will be.
- The motor constant (Km) is the only parameter you need to determine the capacity and efficiency of a motor. It is basically the capacity of a motor to transform electrical power to mechanical power. So when looking for the most efficient motor, instead of computing the efficiency of the motor simply look at the Km value. For the same size motor the higher the Km, the more efficient the motor is.
- The Km value is not really affected by the winding selection of a motor. So in applications where multiple windings are available and the voltage is not yet selected, first select your motor by looking at the Km value then select a motor winding based on your supply voltage. The motor sizing will stay the same because winding selection changes Kt and Ke equally.
- Back EMF (Ke or Kv) is proportional to Kt. So doubling Kt will also double Ke.
- Km is equal to Kt /√Rt. So if you know the motor constant (Km) and the motor resistance (Rt) you can easily derive the torque constant (Kt).
In summary, understanding the importance of the motor constant will greatly assist in the sizing and selection of a DC motor.
The content & opinions in this article are the author’s and do not necessarily represent the views of RoboticsTomorrow

Servo2Go.com Ltd.
Servo2Go.com is an Online E-Store Distributor of Automation & Motion Control Systems & Components including: Servo Motors & Drives, Stepper Motors & Drives, Automation & Motion Controllers, HMIs, Positioning Systems & Actuators, Gearboxes, Couplings, Brakes, Encoders, Tachometers and Linear Displacement Transducers. Servo2Go.com is an ISO9001:2015 Registered Company.
Other Articles
Optimizing Servo System Performance: A Comprehensive Guide to Eliminating Electrical Noise and Enhancing Noise Immunity
The Importance of the Speed-Torque Gradient in DC Motor Sizing
Understanding Torque Ripple in Servo Motors
More about Servo2Go.com Ltd.
Comments (0)
This post does not have any comments. Be the first to leave a comment below.
Featured Product
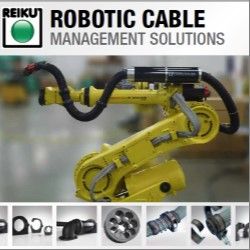