The aim is to develop robotics technology that could be deployed at waste recycling facilities to make them more efficient, but also to improve conditions for workers who sort mixed recyclables by hand.
Worcester Polytechnic Institute Researcher Leads $2.5 Million Study to Develop New Robotics for Recycling Centers
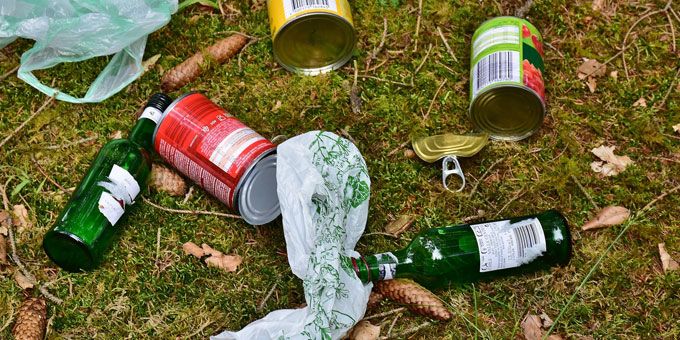
Research from | Worcester Polytechnic Institute
A robotics scientist at Worcester Polytechnic Institute will lead a team of researchers at three universities on a project to develop robotics technology that could help recycling center workers sort waste in a safer, cleaner, and more profitable manner.
Berk Calli, assistant professor in the computer science department and robotics engineering program at WPI, and rk Calleight other researchers will use $2.5 million in funding from the National Science Foundation’s Future of Work at the Human-Technology Frontier program for the four-year project, which will include building a mock recycling line at WPI.
The aim is to develop robotics technology that could be deployed at waste recycling facilities to make them more efficient, but also to improve conditions for workers who sort mixed recyclables by hand.
“What we are trying to do is to introduce robotics technology in such a way that the working conditions of these employees improve,” Calli said. “We approach the problem from a worker-centric view and aim for a human-robot collaboration-based robotic system in which the dirty and dangerous aspect of the job is minimized. Such an approach includes understanding the needs and demands of the workers together with the challenges of the recycling industry, and our interdisciplinary team will cover all these aspects while developing the robotic system.”
The U.S. scrap recycling industry accounts for more than 530,000 jobs and generates $117 billion in annual economic activity while handling large amounts of materials. Americans recycle nearly 68 million tons of waste a year, according to the Environmental Protection Agency.
Editors Recommendation "Artificial Intelligence Drives Advances in Collaborative Mobile Robots"
Yet recycling centers nationwide face challenges in selling sorted materials to processors. China, historically the largest consumer of U.S. recyclables, has imposed tariffs on imports of recyclable waste, while Taiwan has proposed restrictions on imports of recyclables, and Malaysia stopped issuing import licenses for recyclable plastics in 2018 (National Waste and Recycling Association). In addition, workers at recycling centers rapidly sort plastic, paper, metal, glass, and other materials while being exposed to noise, dust, toxic materials, odors, sharp objects, and other hazards.
Robotics Technology Could Help Improve Sorting Operations for Recycling Industry
Improving sorting operations at recycling centers is a difficult technological challenge, Calli said. Because objects of different materials, shapes, and appearances move along sorting lines, often in cluttered piles, the researchers aim to develop object-detection technologies, robotic manipulation algorithms, and robotic arms and effectors to help sort waste.
“We need to basically use everything that we have in the state of the art of robotics, plus push it even further so that we can actually start solving the problem,” Calli said.
Under the collaborative research project, Calli will lead teams at WPI, Yale University, and Boston University. WPI assistant professor of computer science Jacob Whitehill is a co-principal investigator.
“This grant will provide opportunities to study how human workers and robots can work together collaboratively in a physically challenging work environment,” Whitehill said. “Material recycling facilities are not only an important workplace in their own right for environmental reasons, but they also can serve as a research model for how humans and technology can cooperate in the future of work."
Three undergraduate students at WPI are participating in the project by developing a mock sorting line. A master’s degree candidate and two doctoral candidates at WPI will also be involved in the project.
Calli is leading the research with colleagues at two other universities, including five Yale researchers (Aaron Dollar, professor of mechanical engineering and materials science; Marian Chertow, associate professor of industrial environmental management; Brian Scassellati of the Yale Robotics Lab; Amy Wrzesniewski, the Michael H. Jordan Professor of Management at the Yale School of Management; and Barbara Reck, an industrial ecologist) and, from Boston University, Kate Saenko, associate professor of computer science, and Vitaly Ablavsky, senior research scientist in computer science.
About Worcester Polytechnic Institute
WPI, the global leader in project-based learning, is a distinctive, top-tier technological university founded in 1865 on the principle that students learn most effectively by applying the theory learned in the classroom to the practice of solving real-world problems. Recognized by the National Academy of Engineering with the 2016 Bernard M. Gordon Prize for Innovation in Engineering and Technology Education, WPI’s pioneering project-based curriculum engages undergraduates in solving important scientific, technological, and societal problems throughout their education and at more than 50 project centers around the world. WPI offers more than 50 bachelor’s, master’s, and doctoral degree programs across 14 academic departments in science, engineering, technology, business, the social sciences, and the humanities and arts.
If you like this article you may like "Smart Gripper for Small Collaborative Robots"
The content & opinions in this article are the author’s and do not necessarily represent the views of RoboticsTomorrow
Comments (0)
This post does not have any comments. Be the first to leave a comment below.
Featured Product
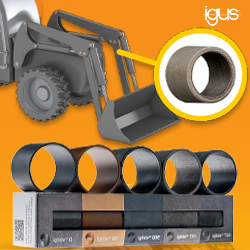