Manufacturers have the choice of robotic grippers, depending on the handling application and the type of material that is being used. There are four basic types of robotic grippers: vacuum grippers, pneumatic grippers, hydraulic grippers and servo-electric grippers.
Looking for a Robotic Gripper?
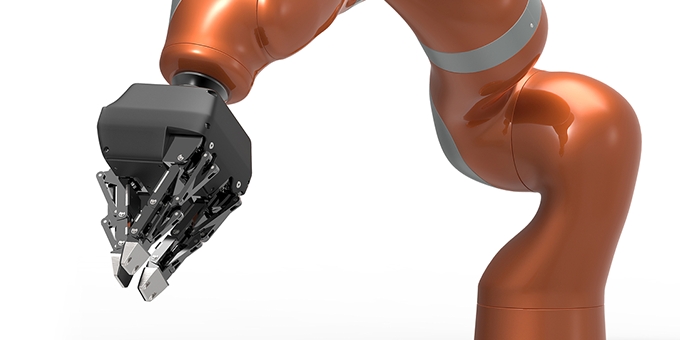
Len Calderone for | RoboticsTomorrow
Manufacturers have the choice of robotic grippers, depending on the handling application and the type of material that is being used. There are four basic types of robotic grippers: vacuum grippers, pneumatic grippers, hydraulic grippers and servo-electric grippers.
Photo by Jeff Green/Rethink Robotics
As robotic applications go beyond the usual high-speed pick and place, robotic functions call for the capability to pick fragile or unusually-shaped items. Grippers provide position, force, and speed control to accomplish the task. A gripper is just one element of a robotic system. Like a human hand, a gripper allows the holding, tightening, handling and releasing of an item.
For non-ferrous items, vacuum grippers use vacuum cups as the gripping device, which are commonly identified as suction cups. When you hang something on a glass window or pick up a sheet of glass, you use a suction cup. Suction cups will stick with quite a bit of force if utilized correctly. The force of air pressure causes them to stick to a surface. To work properly, they need to have a cup shape with a concave center and flat spreading sides. They must stick to to a flat, non-porous surface, and be made of an air-tight material.
The suction cup is pressed against a flat surface while the air trapped inside of the concave area is pressed outwards. A vacuum is formed when the air is forced out. Atmospheric pressure will constantly try to equalize itself. Therefore, air naturally fills in any openings. The internal pressure pushes against the air outside of the suction cup. Since air is unable to penetrate the suction cup surface, it forces the cup against the flat surface. When air gets under the edges of the suction cup, or through the surface, the suction seal will be interrupted and the suction cup will come off.
Pneumatic grippers come in a wide range of sizes, jaw styles, and gripping forces for most industrial applications. These grippers range from miniature to units that have a heavy gripping force. The three major types of pneumatic grippers are parallel grippers, angular grippers, and custom grippers.
With parallel grippers, the two slides either close parallel to the workpiece to grip its outside edges, or opening out to put pressure on inside walls. Parallel grippers are by far the most common design. It’s easy to convert the power of a piston/cylinder system into a gripping force since pneumatic grippers have no motors or gears. Since most manufacturing facilities already have compressed air, little effort is needed to add a pneumatic gripper in a cost-efficient manner.
Angled grippers contact the sides of a workpiece from various angles, such as 30°, 40°, or 80°. Angled grippers can be adjusted to various angles to hold larger workpieces and those with odd shapes. When the space is too tight for a parallel gripper to open wide enough to hold a workpiece, an angled gripper can be used.
A radial gripper is a version of the angled gripper that can be used where vertical space is limited, as their fingers open a full 180°. Fully open, the radial fingers can lie just over or under the workpiece and close when in position.
The hydraulic gripper is often used for applications that require a substantial amount of force. These robotic grippers produce strength from pumps that can deliver up to 2000psi. There are hydraulic grippers that are a cost savings alternative to pneumatics. The main advantage of a hydraulic actuator is its gripping power, which is perfect when there is a need for extra gripping force because hydraulic fluid is not a compressible medium as is air.
Pneumatic grippers have a high pressure of maybe 150 pounds per square inch, while the maximum rating for a hydraulic gripper would be 750-2,000 pounds per square inch. This extra gripping force is put to work handling heavy loads.
Hydraulic grippers cost more and are less accurate than pneumatic grippers; plus, they are not suited for cleanroom applications. Pneumatic grippers are favored because they are clean, compared to hydraulics, which are messy and more costly to maintain. If gripping strength is important, then a hydraulic gripper is the way to go.
Electrical grippers are better for making measurements while manipulating an object, and for finer positioning. If a microprocessor is used, an electrical gripper can measure a part to see if it is the correct size and shape. Such a system can determine if the part is too large in microseconds. If so, the chuck won't release. The disadvantage of electric grippers is they tend to be larger because of the motor, and they also are likely to have less force than pneumatics.
The advantage of electric grippers is that there is the flexibility to only use the minimum necessary clearance to approach a part, and then use a minimum stroke to pick it up. A wider range of part sizes can be picked because of the ability of partial opening and closing without compromising the cycle time.
Error-proofing at the gripper level avoids putting other sensors in the loop, which simplifies integration and reduces cost. This is extremely important in many applications. Both the grip force and the closing speed can be controlled, which is useful when handling fragile parts.
In a clean room environment where air leakage could cause contamination, electric grippers are the only feasible solution to picking up parts. Another plus is by using electrical grippers rather than pneumatic operating costs are reduced.
Robot grippers with 2 fingers are the simplest grippers, and the most applicable for many industrial uses. Different types can be found, such as those with opening control, pressure control, with distance control in the opening and closing, and with picking up pieces by inserting the two fingers inside a hole. Their actuation can be pneumatic or electric.
Robot grippers with 3 fingers are not used that often since most automation situations can be solved with a two-finger gripper. When it’s necessary to pick up delicate objects with strength and accuracy, three finger grippers are the suitable solution. They also adjust better to non-flat surfaces with articulated fingers.
We will see robot grippers being developed using 3D printing as the industry grows. No matter what your need is, you can find a robotic gripper to handle the workload.
The content & opinions in this article are the author’s and do not necessarily represent the views of RoboticsTomorrow
Comments (0)
This post does not have any comments. Be the first to leave a comment below.
Featured Product
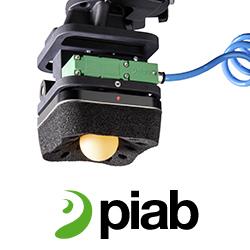