Wedge Conveyors are used to take products from production floor level to a higher level or vice versa. Products are wedged between opposing conveyors aligned vertically or horizontally and are moved swiftly but securely.
Everything You Want to Know About Wedge Conveyors
Contributed by | Dorner
Introduction to Wedge Conveyors
In most facilities, space is a premium, and conveyor location is often dependent on machinery and facility design. At Dorner, our goal is to simplify your processes rather than impede them. We have several solutions designed to give you more floor space and easy access to machinery and other areas of your facility.
Our Wedge Conveyors are used to take products from production floor level to a higher level or vice versa. Products are wedged between opposing conveyors aligned vertically or horizontally and are moved swiftly but securely.
Wedge Conveyors are easy to construct, lightweight and have compact footprints. Its rapid transfer rate makes it ideal for use in continuous, high capacity operations such as packaging lines. Built with aluminum or stainless steel, it meets the stringent hygiene standard required for medical and cosmetic packaging.
They can be configured differently for a variety of uses, such as a transition between different levels, depucking operations, inverted rinse operations, and even for creating a passage way on the production floor.
How a Wedge Conveyor Works
- Constructed with two parallel FlexMove conveyors utilizing a urethane gripper chain that wedge the sides of the product to lift or lower it vertically
Products are fed into the Wedge Conveyor from a horizontal conveyor with at least a product length gap to avoid hitting each other while going through the vertical transition. Products then exit onto a horizontal conveyor
- Can be used with products of various sizes and shapes including boxes, totes, cans, plastic containers and bottles. Product must be able to withstand some side pressure
- Vertical transfer can be through a wheel corner or plain bend corner. Wheel corner is generally limited to product less than 100mm in length
- Can be configured with a manual adjustable conveyor positioner for quick product size changeover. Various configurations can also change product orientation
FlexMove Wedge Conveyor Configurations
Typical configurations for Wedge Conveyors form the following shapes – S, C, N (U) and O.
S Type Configuration
The product is elevated or lowered along a straight path. This is the most common wedge configuration.
C Type Configuration
The product is elevated or lowered while changing the orientation or flipping over the product.
N (U) Type Configuration
The product is elevated and lowered (opposite for U shape) to allow for clearance below the conveyor. This clearance may be needed to allow for traffic through the conveyor or if there is another conveyor or piece of equipment to pass over.
O Type Configuration
The product follows the loop, tipped upside down and conveyed back to near the infeed. This can be used to dry product, or to empty bottles/containers before the next process.
Width Adjustment Actuator
If moving various size products width adjustments can be made using a manual mechanical adjustment system. The system is adjusted by a hand crank at one location that moves each side of the Wedge Conveyor equally about the centerline. System consists of adjustment actuator, angle gear units and connecting shafts.
Width adjustment actuators are required at each mounting location.
Angle Gear Units
Angle gear units connect actuators to move conveyor mounts together.
Application Considerations:
Product Size and Weight
Wedge Conveyors are ideal for transporting metal containers, plastic bottles, paper rolls, boxes or other products that can handle the pressure of the wedge. They are not suitable for wet or heavy products.
Individual product weight generally is less than 4.5 kg (10 lbs) each. However with very sturdy product this can be increased to 9 kg (20 lbs). See page 5 for the various chain types and the recommended product type for each. Total product weight on the Wedge Conveyor should not exceed 90 kg (200 lbs).
The width of the Wedge Conveyor is available in 45, 65 and 85 mm. Generally the width should be at least 1/3 of the height of the product. 85 mm wide wedge units should be use for larger weight/size products.
Products must be fed with at least a product length gap to avoid hitting each other while going thru the vertical transition.
Product height and length affect the wheel type and size to be used. The wheel bend radius is 160 mm. These are limited to small bottle’s generally less than 51 mm (2″) in diameter and 102 mm (4″) tall.
For plain bend corners with a 500 mm radius, which is most commonly used, work best for product up to 457 mm (18″) long and about 305 mm (12″) tall.
For plain bend corners with a 700mm radius, larger product over 457 mm (18″) long can be transported.
Chain Type/Product Capability
Various Wedge finger types are available supporting different product types and weights.
Chain | Specifications | Description | Products |
-5B | Rectangles, round and irregular shaped products up to 3kg (7 lbs)* | Heavy duty angled fingers | For firm grip of various products including irregular shapes |
-5C | Rectangular shaped products up to 4.5kg (10 lbs)* | Heavy duty block wedges | Larger surface area for grabbing larger, heavier products |
-5D | Rectangles, round and irregular shaped products up to 1.5 kg (3.5 lbs)* | Light duty angled fingers | Fingers gently grab lighter products or products that are not rigid surfaces |
*Weights shown are for 85 mm chain. Contact factory for 45 or 65 mm wedge applications.
Chain
Tall or Round Products
Tall or round products need to be gently fed into the wedge and gently released from the Wedge to ensure they do not fall over. This is typical with products such as aerosol cans. To accomplish this, a 5° vertical bend is added to the infeed section and exit section as shown. This allows the grippers to gradually release the product. Round products require a 5º section on the exit. Square or rectangular products use 5º section on the infeed.
Speed Control
The speed of the two opposing conveyors needs to be matched in order for the product to move smoothly through the conveyor. While precise speed matching is not needed, speed control should be done by using two motors with two variable frequency drives. Adjust the frequency to each one so the conveyors are as close in speed as possible. Measuring speed with a tachometer is suggested.
Wear Strip Selection
The pinching action of the wedge put higher loads on the conveyor wearstrip. UHMW-PE wearstrips (FASR-25U) should be used whenever possible. In extreme applications, special low friction, FASR-25X or PVDF, FASR-25P can also be used.
General Specifications
45 mm, 65 mm and 85 mm
- Minimum lower height: 457 mm (18″)
- Maximum upper height: 6096 mm (240″)
- Maximum individual product weight: 4.6 kg (10 lbs)
- Maximum total weight: 90 kg(200 lbs)
- Speeds: Up to 52.2 m/min (171 ft/min)
- Slight variation in product size is compensated for by the flexible wedge fingers without having to adjust the conveyor
Purchasing Wedge Conveyors
Dorner offers three solutions for purchasing a Wedge Conveyor.
- The first solution is to order all the necessary parts and components to build your FlexMove Conveyor on site. This will require the proper tools for cutting, bending and installing the conveyor. Consult our installation guide for FlexMove Conveyors for more details.
- The second solution is to have a complete conveyor provided through our FlexMove Solutions. With Flexmove Solutions you can have the conveyor built in our facility, tested, broken down into shippable sections and ship to the end site for installation.
- The third solution is to work with Dorner to have your FlexMove Conveyor assembled at the final site. The Conveyor will be purchased similar to option 1, but will be shipped as pre-cut and sized components. The Dorner installation team will then assemble and test the equipment at your location. Contact a Dorner representative for a quote on this service.
The content & opinions in this article are the author’s and do not necessarily represent the views of RoboticsTomorrow
Comments (0)
This post does not have any comments. Be the first to leave a comment below.
Featured Product
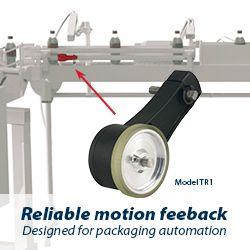