It is true that a collaborative robot is designed to work without additional physical guarding like fencing. But the robot is rarely a lone component in a system.
Benefits of Collaborative Robots

Kelly Chalmers | Applied Manufacturing Technologies, Inc.
Tell us about Applied Manufacturing Technologies.
AMT was founded 30 years ago as an engineering services company and has grown over the last three decades to become a full-scale automation solution provider. Our capabilities offer the ability to engage with our customers at every point in their manufacturing process from front-end consulting, through concept and design, and build and field start-up. We are often focused in robotic automation but our engineers are experienced in many areas of automation technology to allow the solution to best fit the needs of the customer.
How do you define a collaborative robot in your discussions with customers?
Robots that have been labelled as “collaborative” are those devices that have been specifically designed to directly interact with humans without the use of additional safety equipment and components. This is typically through the use of force limited joints and special safety sensors. Other standard industrial robots can be designed into a collaborative workspace but they require other components as part of that system in order to create a protected working environment for humans.
Are there areas of human-robot-interaction that do not fall under your definition of a collaborative robot?
There definitely are. For the purposes of industrial safety analysis there have been four types of collaborative systems defined by how the components of that system work together. Collaborative robots fall into just one of these types of systems. These different ways of monitoring space and tasks allow work areas to be designed with the method best suited for the particular process and functionality. In fact, some systems may still involve standard industrial robots but not the specific collaborative robot models.
What are the most common misconceptions customers have about collaborative robots?
I would say the most common misconceptions have to do with how collaborative robots affect safety considerations for a work space. There are some customers that may see these types of robots as a means to quickly eliminate safety challenges that they are seeing with implementing traditional automation. It is true that a collaborative robot is designed to work without additional physical guarding like fencing. But the robot is rarely a lone component in a system. For example some end of arm tools may not be appropriate with working in close proximity to a human regardless of being mounted to a collaborative robot. So collaborative robots can have some benefit in this aspect but may not alleviate all such concerns. All parts of a system need to be evaluated as part of a risk assessment process.
What are the largest benefits of collaborative robots that you have seen?
There are several benefits of using collaborative robots when the application and process are a good fit. One of the most talked about is floor space. Standard industrial robots tend have buffer space and physical barriers to keep humans separated from automation hazards. Comparatively, a properly designed area for collaborative robots will typically be “fenceless” and not require additional space between automation and human workspaces. This use of collaborative robots takes up less valuable real estate in an industrial environment.
Another benefit of collaborative robots is to create truly collaborative processes where automation and humans work not only alongside but actually with each other. Consider an assembly area today where a human may perform many tasks to get parts, fit them together, and test function. With collaborative robots we can separate these tasks to assign repetitive monotonous tasks to automation and have the humans assigned to tasks that are more dexterous or those that require decision making.
How are your customers using collaborative robots?
We have implemented collaborative robots in a variety of applications for our customers. Really the range of applications is wide, particularly as different industries get introduced to the technology. Many of the systems have focused on testing applications, pick and place material handling, and packaging handling -- driven by finding opportunity in traditionally manual workspaces.
There are still some limitations that can be a roadblock. For example, collaborative robots have inherent speed restrictions that may impact the productivity of using this type of automation. The devices often have payload and accuracy limitations that can affect capability for a task. And there are some tasks that require non-collaborative tools to complete. But these are all pretty recognized challenges that many companies are trying to provide options for.
What do you think are the most promising developments coming in collaborative robots?
Most of the development that I think will have widespread impact has to do with application of the technology. When collaborative robots were first released people were excited but still unsure of how to really implement them. As use cases become available they quickly become adopted around an industry. One example of this is tire handling, which often happens in a highly manual workspace but is very cumbersome for actual manual activity. Large collaborative robots are now common place in automotive plants for this process. Another area of development is collaborative robot tooling. Several companies are working to provide this type of design solution to companies that want to implement collaborative robots so that they can realize the most benefit from the “fenceless” capability.
Finding solutions like these can have exponential impact. Once a company or industry has some understanding of how to implement the technology then they will use that same methodology to replicate the value over and over again.
Are today’s safety standards for collaborative robots adequate?
There has been a lot of emphasis over the last several years to address collaborative robots and collaborative technology in general, so it is moving forward. There still seems to be a general lack of clarity/understanding of how safety reviews and risks assessments are carried out. And this definitely gets more complicated with a collaborative system. The lack of consistent global standards is also a challenge as we deal with companies that work in different countries but want to create consistent automation processes.
Collaborative robots have helped open some doors to industries and customer segments that are new to robot automation. This is a great thing but it also means that there are people with less experience in these standards who need assistance walking through some of these considerations.
About Applied Manufacturing Technologies, Inc.
Applied Manufacturing Technologies, Inc., is a member of the Control System Integrators Association (CSIA). For more information, visit the company profile on the Industrial Automation Exchange.
About Kelly Chalmers
Kelly Chalmers is a project manager at Applied Manufacturing Technologies, Inc. She leads systems integration projects at AMT along with many internal initiatives within the company. Her experience in automation has been largely focused on operations optimization and manufacturing process analysis. Kelly brings over 15 years of automation experience to AMT and holds a BS in industrial engineering from the University of Michigan and an MBA from Kettering University.
The content & opinions in this article are the author’s and do not necessarily represent the views of RoboticsTomorrow
Comments (0)
This post does not have any comments. Be the first to leave a comment below.
Featured Product
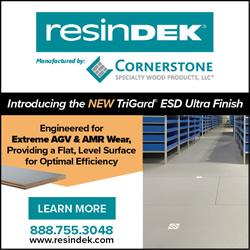