Meet the new colleague for the crew of the International Space Station (ISS): an autonomous camera drone. The small sphere films the astronauts at work and this drone could potentially save about ten percent of their valuable working time.
Meet the Free-flying Camera on the ISS

Contributed by | maxon motor
Reposted with permission from the maxon motor's blog:
Meet the new colleague for the crew of the International Space Station (ISS): an autonomous camera drone. The small sphere films the astronauts at work and this drone could potentially save about ten percent of their valuable working time.
An astronaut of the International Space Station (ISS) moves weightlessly from one module to the next. As soon as they has finished one experiment, the next one is waiting. Mission control gives him exact instructions on which steps he has to perform, one after the other. The astronaut films his every move so that the experts on Earth can see in real time whether he is doing everything right. This is sometimes tedious and consumes a lot of time. Valuable time, because the program on the ISS is tightly scheduled. Experiments under conditions of weightlessness give revealing results and are much sought after by research institutions worldwide.
Drone looking over the astronaut's shoulder
A possible solution now comes from the Japan Aerospace Exploration Agency (JAXA). It has developed the Int-Ball: a camera drone that shoots videos and photos aboard the Japanese Experiment Module, known as “Kibo”. The drone can move autonomously or be controlled directly from Earth, has a diameter of only 15 centimeters and looks over the shoulder of the astronaut while he works - without distracting him.
JAXA estimates that astronauts spend about ten percent of their time for the ISS photographing work. The Int-Ball could thus save a lot of time in the future, leaving the astronauts with more time for experiments or repairs. The goal is to reduce the photographing work of the astronauts to zero and to increase their freedom of movement. Ground-based researchers in turn get the same view as the crew members of the ISS through the Int-Ball.
Inside the Int-Ball drone, there is a cubic control unit equipped with a 3-axis reaction wheel to control the drone's attitude and stabilization. Each reaction wheel is driven by a brushless EC 10 motor from maxon motor under the cubic inside control unit. The control unit in turn is connected to twelve small fans, with which the drone controls its position.
Inside the drone, a navigation camera developed by the Tokyo University, called Phenox which estimates its own position by processing the image of a 3-D marker installed on the “Kibo”, is also installed.
The system is still evolving. In fact, JAXA is already planning further improvements to its Int-Ball drone. "We hope that a future version of Int-Ball will also work with the astronauts even outside the space station," says a JAXA staff.
After all, maxon drives have consistently shown that they only need small modifications to work reliably in a vacuum.
The content & opinions in this article are the author’s and do not necessarily represent the views of RoboticsTomorrow
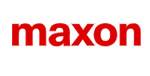
maxon group
maxon is a leading supplier of high-precision DC brush and brushless servo motors and drives. These motors range in size from 4 - 90 mm and are available up to 500 watts. We combine electric motors, gears and DC motor controls into high-precision, intelligent drive systems that can be custom-made to fit the specific needs of customer applications.
Other Articles
Automate 2025 Q&A with maxon group
Understanding Torque and Speed in Electric Motors
How Parvalux Is Helping to Develop the Next Generation of Conveyor Systems
More about maxon group
Comments (0)
This post does not have any comments. Be the first to leave a comment below.
Featured Product
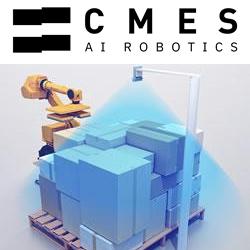