Industrial inspections, regardless of the reason for inspection, can be a very dirty and dangerous job. While not necessarily dull, industrial inspections definitely cover two of the three Ds of robotics deployment (dull, dirty, and dangerous).
5 Reasons To Consider Robots for Industrial Inspections
John Santagate | IDC
There are a lot of emerging use cases for non-traditional robotics. What makes industrial inspections one that organizations are tacking today?
Industrial inspections, regardless of the reason for inspection, can be a very dirty and dangerous job. While not necessarily dull, industrial inspections definitely cover two of the three Ds of robotics deployment (dull, dirty, and dangerous). Industrial inspections can range from inspecting operational assets and operational facilities to inspecting defunct facilities during the decommissioning process or evaluating the health and risk of nonoperational holding tanks. Doing this job is necessary, but it is often very expensive and very dangerous. Robotics is helping organizations to improve safety during these inspections and also helping to drive down the cost and resources required to conduct the inspections.
So, are there robots then that can autonomously conduct industrial inspections?
For this particular use case, it is more about taking human inspectors out of harms’ way by augmenting their skills through robotics. Automation is indeed something that can be valuable in certain scenarios, but I think that the use of robots for industrial inspections is really about using guided systems that can safely reach and operate in places that are difficult and dangerous for people. For example, inspecting a nonoperational holding tank that had been used to store hazardous waste might traditionally require a well-equipped team of human operators to physically enter the space, capture samples of any remaining material in the tank, and visually inspect the interior walls and elements of the tank for signs of corrosion or depredation. But, with the help of modern robotic technology, a device can be deployed into the tank to capture samples and video and relay this information without the need for a human to set foot in the hazardous environment. This approach can help to reduce risk, reduce the time it takes to complete the inspection, and improve the ability to capture and analyze data relative to the inspection.
A recent report you published was titled "Five Key Reasons to Consider Robotics for Industrial Inspections.” What are those five key reasons?
The report explored five areas that are helping to make the case for organizations to invest in robotics for industrial inspections. This is not to say that they are the only reasons, but each of the five areas are points of value for robotics in industrial inspections today. They are: safety, time, analytics, access, and cost.
- Robots for industrial inspections are helping to improve safety by taking humans out of hazardous environments and scenarios and using robotic technology to perform the traditionally manual task.
- They are helping to reduce the time it takes to conduct industrial inspections by reducing the number of humans that must be involved in the process (reducing man hours) but also reducing the number of change overs and repositioning required to conduct such inspections.
- Improving analytics is about allowing an organization to create a digital alignment to the physical space and processes, the devices are also able to capture information in real-time and accelerate the process of conducting analysis.
- The use of robotics for industrial inspections is also improving access to difficult to reach and inspect areas by using robotics that have a much smaller and more nimble footprint than having to put a human in a confined space.
- Finally, reducing cost is a key consideration as industrial inspections can be very expensive. Not only does robotic technology help to reduce the number of people required for an inspection, it can also help to mitigate the cost of safety equipment required. This is last point is not to say that people are no longer necessary, rather it is about making better use of human resources and allowing an organization to redeploy those that would otherwise be tied up doing inspections to focus on other things.
There are different categories of robotics, industrial and commercial service robotics, where do these devices that are performing industrial inspections reside?
This is an interesting question, because we often define robots by the use case and those used for industrial manufacturing would be considered industrial robots. However, with the rise in non-traditional robotics the lines are indeed blurring. Industrial robots are those robotic arms, like you expect to see in an automotive manufacturing plant. For inspections, we are talking about mobile robots that are quite flexible and have a very small footprint (mostly). So, from my perspective, robots that are used for industrial inspections (such as inspecting a facility, duct work, tanks, etc.) these would be commercial service robots being used within an industrial manufacturing environment. The other thing that really sets these apart is that they are operated by humans, where traditional industrial robots are autonomous. That said, growth in the availability and capabilities of robotics and the emergence of collaborative robots is resulting in the ability to use industrial robots in non-industrial manufacturing environments as well as the ability to use commercial service robotics within industrial manufacturing environments.
So, who is buying and using these industrial inspection robots?
I would say there are several ways this technology can be deployed. First, is obviously the ownership and use robotics directly by the operators of an industrial manufacturing facility. If the organization is conducting its own inspections, then it would make sense for them to have robotic tools available for its employees to keep them out of harms’ way, reduce the cost and disruption of conducting inspections, and enhance the capabilities of the people doing inspections. Additionally, there are businesses that operate specifically in the space of performing industrial inspections, and of course these organizations would consider this technology. Not only does it address the five key reasons mentioned before, but it can also help to increase capacity by requiring less humans to perform certain inspections, the company would have the ability to redeploy its people and essentially cover more ground with the same base of human resources. I think it is also reasonable to expect to see organizations that perform site audits and insurance companies using robotic technology to improve their ability to create a complete perspective of a facility. Overall, there is an abundance of opportunity for this technology and the benefits make robotics for industrial inspections something that is very hard to ignore.
For More Info Read John's Full Report
About John Santagate
John Santagate is a Research Director at IDC responsible for the service robotics market. Mr. Santagate’s core research coverage includes market trends and forecasts for service robotics, business process evolution through the use of service robots, and the integration of robotics into business processes and business IT architecture. Mr. Santagate’s research looks across industries and seeks to deliver actionable intelligence to organizations around the deployment and use of robotics as well as related technology areas that are helping to enable wide spread adoption of robotic technology.
The content & opinions in this article are the author’s and do not necessarily represent the views of RoboticsTomorrow
Comments (0)
This post does not have any comments. Be the first to leave a comment below.
Featured Product
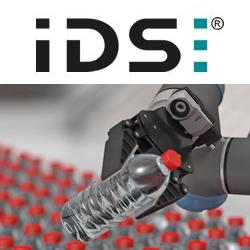