As the continued e-commerce wave drives industry-wide pressure to deliver orders on time, there has been an explosion of cobot startups focused on improving the efficiency of picking and packaging boxes of mixed items.
Next-Gen Robots Powered by Data Fueling Manufacturing Efficiency

Tsipora Cohen | Magic Software
Collaborative robots, or cobots for short, are a new generation of smaller robots that can be integrated into any production line and rely on human hands to guide them instead of complex programming. Relatively inexpensive (starting at as little as $24,000), cobots can help manufacturers, including medium-sized businesses experience a quick return on investment by automating simple, repetitive processes. With the average factory worker currently earning $14.98 per hour in the US, according to salary comparison website PayScale, the return on investment can be achieved in just a few months.
Cobots Are Already on the Job
Due to their flexibility, ease of use, and affordability, cobots can be used for food processing, manufacturing, construction, retail, healthcare, pharmaceutical, the hospitality industry and more. According to a report from ABI Research, the global market for cobots will increase tenfold from 2015 to 2020, reaching over $1 billion.
Able to safely handle hot or awkward work pieces that would be unsafe for humans, cobots can work side by side with workers and be assigned to low-value tasks so that technicians can take care of more important jobs. For example, in an automobile factory, a human worker can place the tools in front of a cobot so it can tighten a bolt to the exact level of tension required. Joe Shelton, a manager at car maker Nissan’s plant in Tennessee, says the time needed to reconfigure a new car model has been cut from more than a year to a matter of days thanks to the use of more flexible robotic systems.
As the continued e-commerce wave drives industry-wide pressure to deliver orders on time, there has been an explosion of cobot startups focused on improving the efficiency of picking and packaging boxes of mixed items. Amazon now has more than 100,000 robots in its warehouses across the globe and plans to add more. DHL piloted fully automated trolleys that follow pickers through the warehouse, carry the weight and automatically drop off orders once fully loaded.
Due to the strong return on investment, smaller sized companies are also bringing cobots on board. Stenner Pump, a Florida-based company employing 90 people, acquired Baxter, a two-armed cobot to feed parts directly from manufacturing into packaging, reducing human handling by 75 percent. In March 2018, Southern California restaurant chain CaliBurger tried out Miso Robotics‘ burger-flipping cobot arm dubbed “Flippy.”
But these examples are just the beginning. Cobots are continuously improving with respect to their abilities. As the safety and capabilities of the cobots increase, the demand will also increase, which will most probably attract startups to develop even more advanced cobots, creating a loop for continuous innovation with opportunities for more uses.
Cobots Leveraging Data
In addition to performing difficult, repetitive, or monotonous processes, cobots can become an important source of data to optimize end-to-end business processes. They can collect details on the number of units produced in a given period of time and share this data with logistics, warehouse management, and finance systems, for more effective material, inventory and supplier management.
In order to leverage information created by cobots, a steady stream of performance and production data needs to be collected, stored, analyzed and shared efficiently and reliably. In addition, throughout the entire process, all the information needs to be secure to protect a manufacturer’s intellectual property and its customers’ personal data.
Initially, point-to-point system integrations can be less costly, because the projects are more bounded and often internal resources can be used. But, in time, these projects can multiple rapidly and become unwieldy as more and more cobots are added and become an integral part of a factory’s information network. A more resource efficient and practical solution can be a multi-point third party software platform that provides scalability and unified data handling when sharing data between back office and shop floor systems.
Cobots are becoming an integral part of the factory of the future providing not only more labor- efficient and reliable manufacturing processes, but also valuable data for improved efficiency. More than a way to speed up repetitive and mundane tasks, the data they generate and share can introduce new efficiencies across the entire organization.
The content & opinions in this article are the author’s and do not necessarily represent the views of RoboticsTomorrow
Comments (0)
This post does not have any comments. Be the first to leave a comment below.
Featured Product
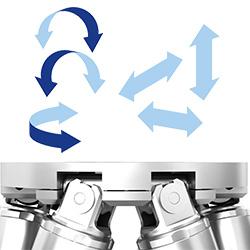