If a robot is dealing with electronics, it needs to know whether its hand is sliding along a wire or pulling on it. If the robot needs to hold a medical instrument, it needs to know if the object is slipping or in a firm grip.
Len Calderone for | RoboticsTomorrow
Softer than human skin, gentler than a baby’s touch, able to feel temperature changes. It’s a sensor. . . it’s a polymer. . .It’s artificial skin for robots. (Sorry, Superman)
Robots are becoming more human-like every day. They are getting artificial intelligence, flexibility, and human appearances. Now, the researchers from UCLA and the University of Washington implanted flexible sensors into artificial skin, which is extended over robotic fingers or prosthetics to improve a robots’ ability to feel.
Robots can perform human gripping and manipulating tasks by sensing the item, with which they come in contact.
Our skin is the body’s largest organ, and it is full of nerve endings that provide us with instantaneous information of temperature, pressure and pain. Robotic skin will be made of a smart polymer core, which expands, depending on the humidity and temperature, and a piezoelectric shell, which generates an electric current when pressure is applied.
The SmartCore project, funded by the European Research Council and at the Graz University of Technology in Austria, is working on a material that reacts to multiple stimuli. This requires working at a nanoscale, creating embedded arrangements of microscopic sensors that could be 2,000 times more sensitive than human skin.
The smart core would be inserted between two small nanoscale grids of electrodes, which detect the electrical charges produced when the sensors feel an object and then they transmit this information to the central processor. The biggest challenge is being able to distinguish between the different senses.
Researchers looked to human biology when designing the skin. They developed sensors that make it uncomplicated when performing human tasks, such as opening a door, playing musical instruments, and shaking hands. The researchers have achieved a degree of sensitivity that’s consistent with human hands.
This technology incorporates stretchable circuit devices and implants them into a flexible material. The electronic materials are comprised of semiconductors that operate as a suitable medium for the control of electric current. These semiconductors can either be carbon-based or non-carbon based.
The problem is that neither type of semiconductor can be stretched. At one time, researchers designed structures to relieve some of the strain caused by stretching stiff materials.
Rubber electronics and sensors that operate as normal even when stretched to up to 50% of their length could function as artificial skin on robots. The material is able to sense strain, pressure and temperature just like human skin.
Humans want to work near robots, but for that to happen safely, the robot needs to be able to fully sense its surroundings. A robot could work side by side with humans without endangering them, if they have a soft, flexible skin that can feel its surroundings.
Rather than inventing complicated polymers from scratch, researchers are using low-cost, commercially obtainable alternatives to produce a stretchy material that functions as a stable semiconductor and can be scaled for manufacturing.
This stretchable material is made by mixing tiny, semiconducting nanofibrils, which are fibrils with diameters less than 100 nm, into a solution of an extensively used, silicon-based organic polymer, called polydimethylsiloxane. When dried at 140 degrees Fahrenheit, the solution hardens into a stretchable material implanted with millions of tiny nanowires that carry electric current.
Applied to the fingers of a robotic hand, the electronic skin works as a sensor that produces diverse electrical signals when the fingers are bent. This places a strain on the material, which changes the electric current flow that can be measured.
Soft robotics involve machines designed to look like biological systems. Although not very practical today, soft robots could prove invaluable in the future.
Hard robots, made of rigid limbs, are used in manufacturing and require very careful programming. These machines are programmed to do just one job and to complete that task. These robots are useless once placed outside of their work environment. Soft robots, on the other hand, are made from elastic and flexible materials, which permit them to mold to the environment, just like their biological counterparts. Such machines can perform tasks impossible by rigid robotics standards.
They are much more versatile, as they have sensors in the hand that can measure the shape of an object; and using an algorithm, the hand can distinguish one object from another, such as a DVD, an egg or a glass.
A soft hand is a lot simpler for a robot to handle an object. A rigid hand needs complicated planning to decide how it is going to pick up an object, such as where to place its fingers so that it doesn’t drop the object. A soft hand can just grab an object, by bending around the object and picking it up.
Researchers have given artificial skin the ability to detect vibrations and forces, attaining a level of sensitivity and accuracy similar to human hands. Robots can perform delicate operations without human operators because of this ability.
When meeting, humans obtain important information from touch. By touching, we learn a lot about the other person. A handshake, for instance, can tell if a person is strong or weak, nervous or outgoing. A robot must be able to have the ability to understand the intended meaning of touch. The enhancement of a similar capacity in a robot has the potential to substantially improve the future success of instinctive human and robot interaction.
If a robot is dealing with electronics, it needs to know whether its hand is sliding along a wire or pulling on it. If the robot needs to hold a medical instrument, it needs to know if the object is slipping or in a firm grip. For these and other actions, a robot needs the ability to sense shear force. Impulses must be decoded to get a sense of the shear forces that are involved when fingers slip and slide when handling different items.
Researchers believe that artificial skin for robots could have other uses because the skin is soft, bendable, stretchable and twistable. Artificial robotic skin will impact future development in soft wearable electronics, including health monitors, medical implants and human-machine interfaces.
For additional information:
-
http://citeseerx.ist.psu.edu/viewdoc/download?doi=10.1.1.653.575&rep=rep1&type=pdf
-
https://pdfs.semanticscholar.org/d3f7/99799219f45290ae4ed3e6bd814caa08a033.pdf
The content & opinions in this article are the author’s and do not necessarily represent the views of RoboticsTomorrow
Comments (0)
This post does not have any comments. Be the first to leave a comment below.
Featured Product
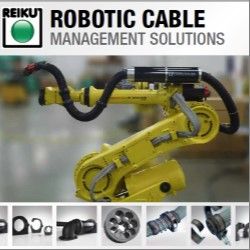