Without tool changers, we have to manually detach the tool from the robot with bolts and thumbscrews, wheel the tool away on a cart, and attach a new tool the same way. This is tedious and not possible for one person to do by themselves.
Case Study: ATI Tool Changers Transform Schmalz's Design-Test Center
Contributed By | Schmalz And ATI Industrial Automation
Schmalz recently deployed ATI’s Robotic Tool Changers in a new, sustainable, automated design-testing application. The results bring more comprehensive concept proofing and decreased project turnaround time for customers. It is widely known that ATI products can increase the productivity of automated systems, but at Schmalz, this reaches a whole new level.
Each project at Schmalz is unique and begins with a full-scale evaluation of the customer’s existing application. Historically, this is one of the most time-consuming tasks in the project timeline due to its heavy reliance on manual labor. Since the addition of ATI Tool Changers to their Robot Test Cell, Schmalz experiences more comprehensive design testing and an increase in project throughput. Together, these process improvements enable a higher level of customer service.
The new Robot Test Cell includes one QC-310 Master and three QC-310 Tools mounted to different Schmalz Layer Grippers–which can weigh up to 130 lbs each before any product is handled. Due to the wide breadth of customer material used in vacuum gripping applications, they needed a system to accommodate anything from featherweight plastic sheets to extremely heavy automotive components. ATI’s Heavy Duty QC-310 Tool Changer suited both the size of their 600 kg FANUC robot and the unpredictable loads of their customers’ test material.
The first step in automating their proof-of-concept process included installing a large FANUC robot for material handling. This provided some initial benefits, but they still had to change tools by hand, which created downtime. Schmalz Applications Engineer Lee Strahler reports, “Without tool changers, we have to manually detach the tool from the robot with bolts and thumbscrews, wheel the tool away on a cart, and attach a new tool the same way. This is tedious and not possible for one person to do by themselves.”
Integrating ATI’s Heavy Duty Tool Changer products gave Schmalz the ability to handle the variable payloads of customer material and seamlessly transition between each of the different Layer Grippers in a single test run. If needed, they can perform multiple trials to narrow down and select the best equipment for the job. The new process cuts down on the non-value added time in the application and enables quicker turnaround of designs. Strahler also noted that the use of ATI’s Tool Changers in the application provides an additional measure of safety by keeping employees out of the robot cell.
The biggest obstacle for Schmalz’s Robot Test Cell was the lack of a dedicated robot programmer on-site. Strahler comments, “In order to set this up and make it work for us, we needed the tool change process to be quick and easy for one of our application engineers to program.” She goes on to say that the built-in Fail-Safe Locking Mechanism, easy-to-use Lock and Unlock sensors, and the high repeatability of ATI’s Tool Changers made these products simple for a less-experienced programmer to implement. “Losing air-pressure and dropping a multi-thousand dollar tool was not an option,” says Strahler, and the inherent features of the ATI Tool Changer helped Schmalz avoid this.
The installation was a critical investment that has lead to savings of time and money. With the new robot test cell, Schmalz can design and test more custom systems in a shorter amount of time and evaluate each customer sample more thoroughly. The new system falls in line with the company’s sustainability goals as well; it is contained in a single work cell, and additional tools can be added quite easily to further increase productivity. In fact, Schmalz is developing a special bag gripping tool specifically to serve the US customer market.
About Schmalz, Inc.
Schmalz is the global market leader in vacuum automation and ergonomic handling solutions. Schmalz products are used all over the world in applications in the logistics, glass, metal, automotive, packaging, and wood industry sectors.
With comprehensive consulting, a focus on innovation and first-class quality, Schmalz offers its customers long-lasting benefits. Schmalz's intelligent solutions make production and logistics processes more flexible and efficient, while also preparing them for the increasing trend toward digitalization.
Schmalz is represented in more than 80 countries and in all important markets. The family-owned company has over 1,100 employees at its headquarters in Glatten (in the Black Forest region of Germany) and its 17 international subsidiaries.
The content & opinions in this article are the author’s and do not necessarily represent the views of RoboticsTomorrow
Comments (0)
This post does not have any comments. Be the first to leave a comment below.
Featured Product
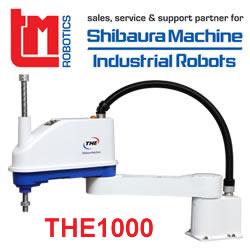